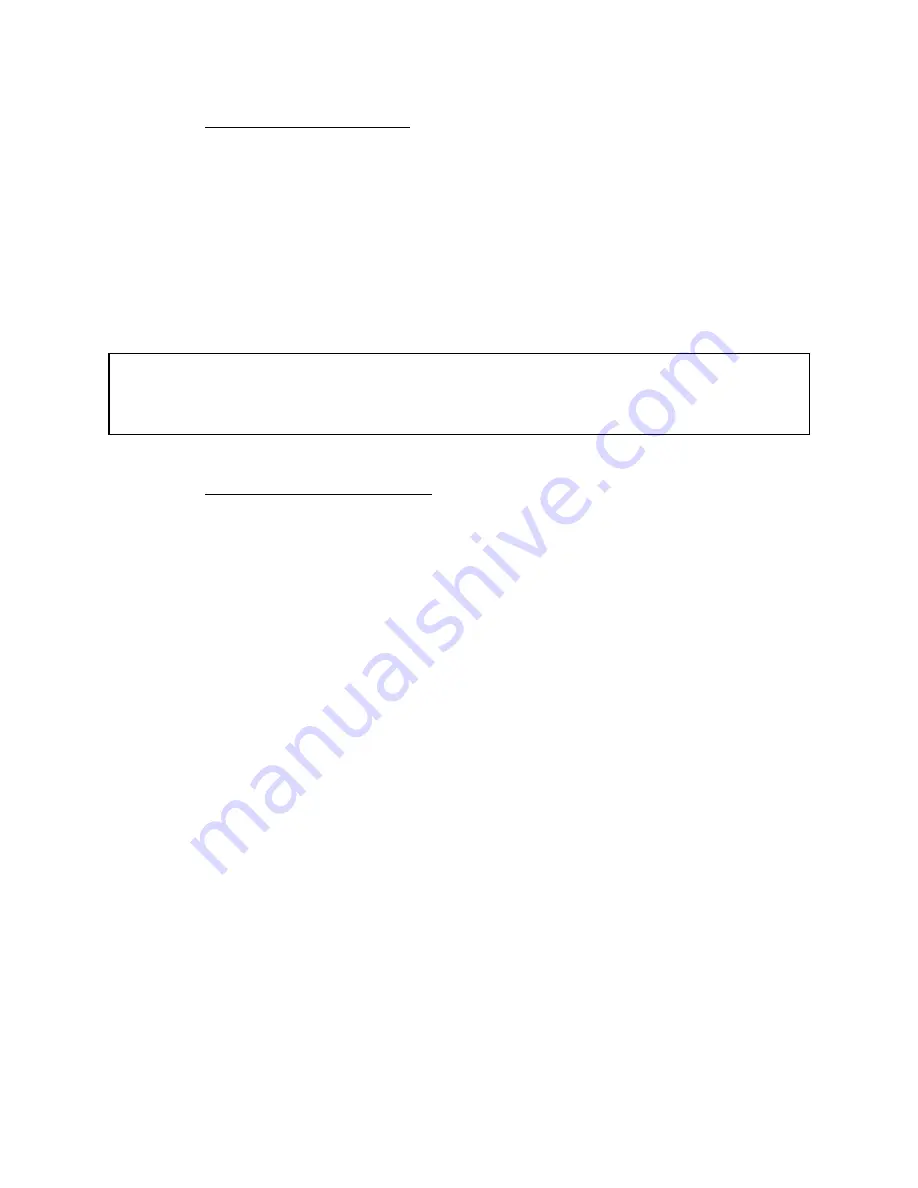
21
d.
Shutdown Procedures.
(1) Place the AC CIRCUIT INTERRUPTER switch in the OPEN
position. Allow the generator 3-5 minutes to cool down the
engine.
(2) Place the START/RUN/STOP switch in the STOP
position.
(3) Pull out the DC CIRCUIT BREAKER.
e.
After Operations PMCS
.
(1) Inspect the housing, air ducts, exhaust grills, door
fasteners and hinges for obstructions, serviceability and proper
operation.
(2) Ensure the acoustical material is free of damage or
not missing.
(3) Inspect the skid bases to ensure they are not
corroded or cracked.
(4) Inspect the fill neck strainer for damage. Inspect
vented fuel cap and auxiliary fuel connection for obvious damage
or leakage.
(5) Ensure the identification plates are secured and are
in place.
(6) Inspect the control box to ensure all switches,
meters, indicators and terminals are operational.
(7) Check convenience receptacle for signs of electrical
short and corrosion.
(8) Ensure NATO slave receptacle has no damage or shows
any signs of electrical shock or corrosion.
NOTE
GENERATOR MUST BE SHUT DOWN EVERY 8 HOURS TO SERVICE OIL AND
FUEL WATER SEPERATOR. (SEE TABLE 2-1 ITEM 16 & 17)