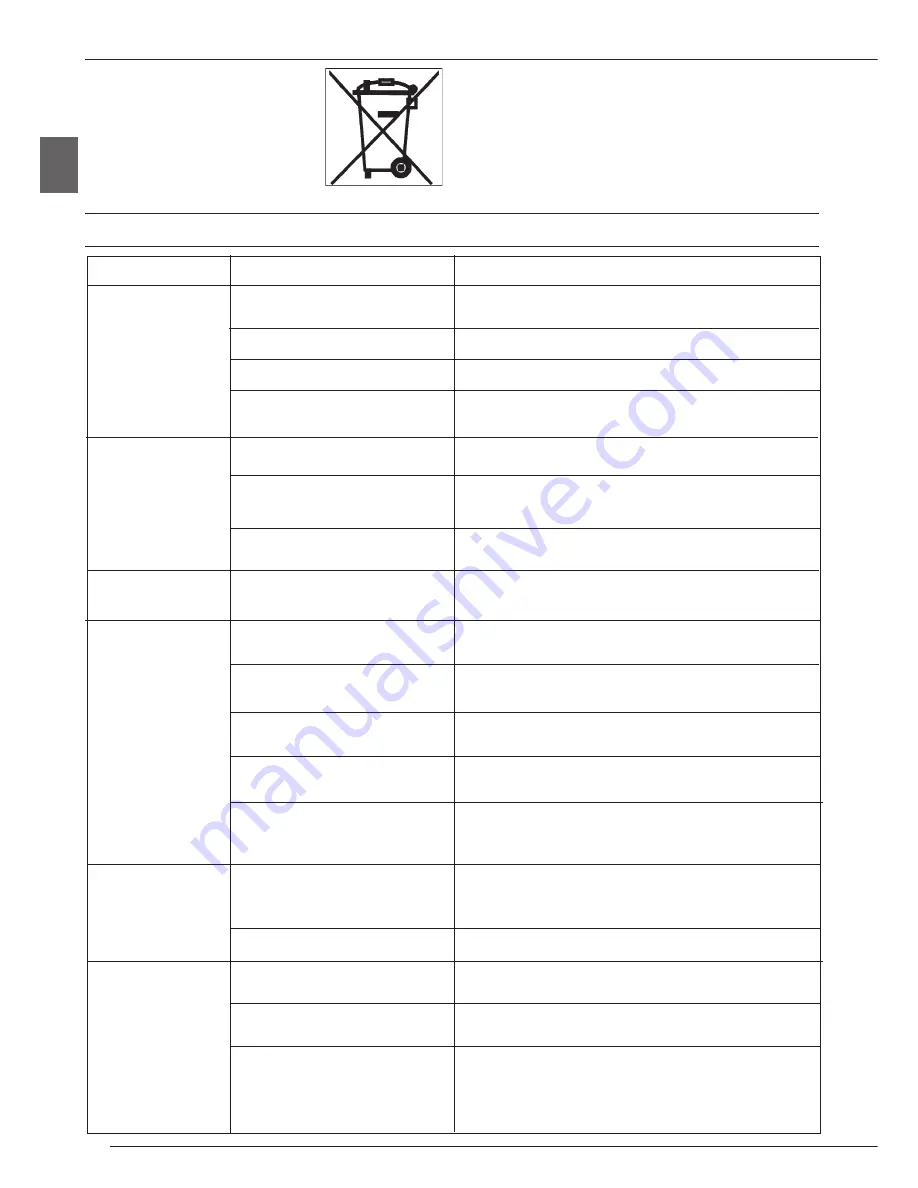
12
EN
Defective motor, power cable or
plug.
Blown electric panel fuses.
No voltage in the mains system.
The overload cutout has tripped.
Motor overheating.
Motor overload caused by
excessive cutting pressure.
Motor breakdown.
The setting of the H and K retainers
(point 3.3) is inaccurate.
Excessive cutting pressure (on
pipes and section bars).
Incorrect blade toothing in relation
to the piece to cut.
Incorrect adjustment of the
eccentric and sliding blade-guides
Incorrect cutting speed in relation
to the piece to cut.
The piece is wrongly positioned in
the vice.
Poor blade tension.
The blade is worn or its toothing is
not right for the thickness of the
piece being cut.
Excessive cutting pressure.
Incorrect eccentric blade-guide
adjustment.
Excessive wear of the pulley rubber
linings.
The blade slips on the pulleys,
caused by oil or grease required for
cutting operations.Check blade
tension (point 3.1).
The motor does not
work.
Overload cutout
tripped.
Inaccurate cutting
angle at 90° - 45°.
Inaccurate
cut squaring.
Cut finish is coarse
or corrugated
The blade tends to
protrude from the
guides.
Specialized personnel should check the machine; do not
attempt to repair the motor by yourself.
Check fuse integrity and replace, if necessary.
Check for voltage in the mains system.
Release the run button and wait a few minutes for the
overload cutout to reset.
Check that motor air intakes are clear.
Perform the cut on the piece at the correct pressure
Specialized personnel should check the machine; do not
attempt to repair the machine by yourself.
Set the retainers by unloosening the fastening screws
and re-positioning them.
Decrease cutting pressure.
Check the cutting parameters (blade toothing, cutting
speed) in the cuts table (point 4.6).
Check blade-guide adjustment (points 3.5 and 3.6).
Check piece positioning and clamping in the vice (point
4.5).
Check blade tension (point 3.1).
Check the cutting parameters (blade toothing, cutting
speed) in the cuts table (point 4.6).
Decrease cutting pressure.
Check eccentric blade-guide adjustment (point 3.6).
Specialized personnel should check the pulleys and replace
them if necessary.
Never use any type of lubricant or coolant for the cutting
operations; specialized personnel should check and, if
necessary, replace the pulleys.
PROBLEMS
PROBLEMS CAUSES
SOLUTIONS SUGGESTED
6.3
DISPOSAL OF THE
MACHINE, PACKING
At the end of the machine life, if the
machine must be scraped, contact
an authorised waste disposal centre
in order to comply with the Standards
for hygiene and environment safeguard.
The packing must be disposed of according to the ruling
standards by delivering it to authorised people for the
collection, disposal or reclaim.
Please contact the ASSOCIATION OF USED OILS near to
you.
7
TROUBLESHOOTING
2002/96/EC