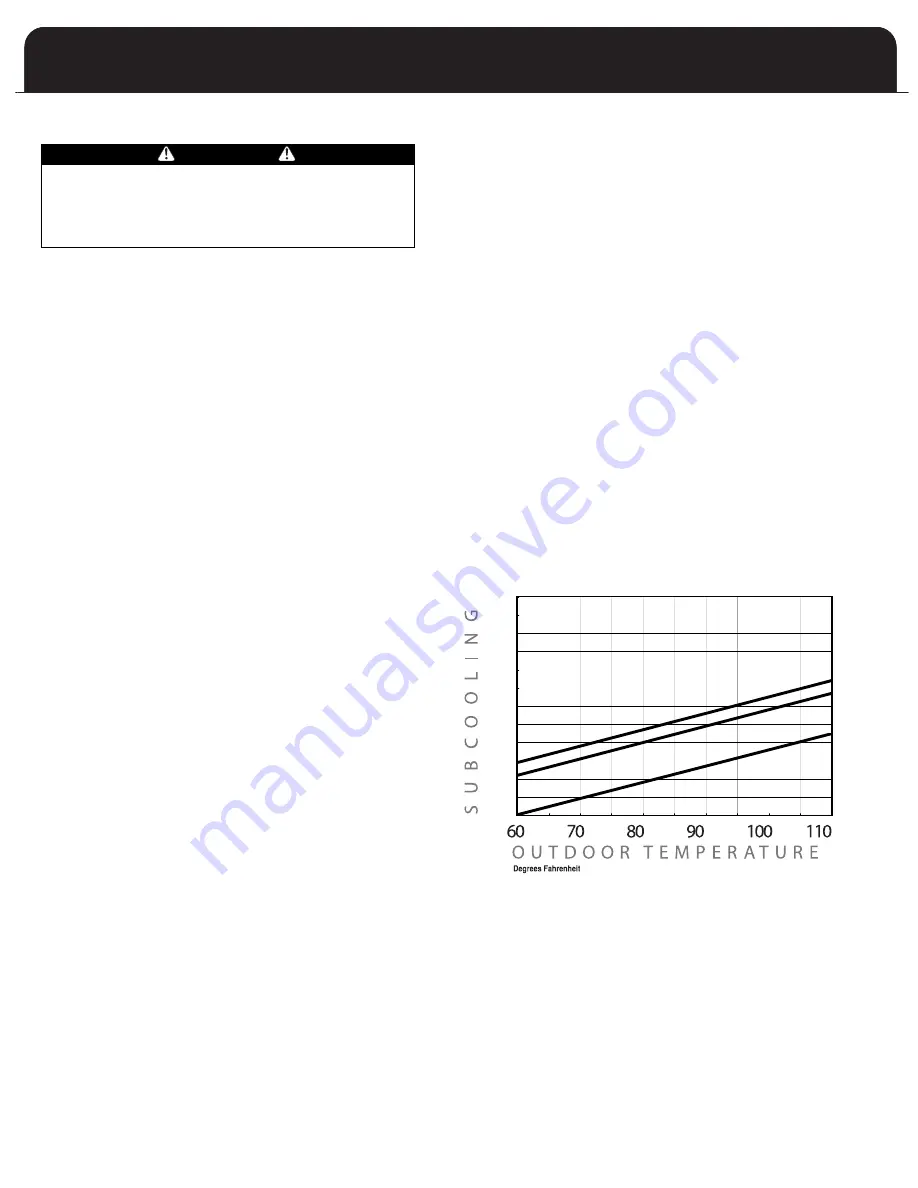
Model
5
SUB-COOLING CHARGING
Coils with TXVs should be charged 10-12 degrees (+ or – one
degree) of sub-cooling. For proper sub-cooling readings, a
standard high side gauge is required for pressure readings.
Use the chart below to determine the required sub-cooling value.
INSTRUCTIONS
1. Measure the outdoor air temperature. (T1)
2. Measure the liquid line pressure and determine the liquid
refrigerant temperature by the scale on the high side
pressure gauge. (T2) In cooling mode take reading at the
indoor coil before TXV.
3. Measure the liquid line temperature on the liquid line. (T3) In
cooling mode take reading at the indoor coil before TXV.
4. Subtract T3 from T2. (T2 – T3) This is the subcooling value.
Compare this value and the outdoor temperature (T1), to the
charts below. If the value is below the line, add refrigerant. If
the value is above the line, remove refrigerant charge. When
removing refrigerant, always use standard reclaim procedures.
NOTE: For the majority of installations no adjustment to the
TXV setting is required. However, if the measured superheat
at the evaporator is less than 4° or greater than 8° an
adjustment is required. The adjustment stem is at the base of
the valve under the flare nut. To increase superheat tighten
the stem clockwise and to decrease superheat back-out the
stem counter-clockwise. Use a 1/4” refrigeration service
wrench for this function.
NOTE: When removing refrigerant, always use standard reclaim
procedures.
FINAL CHECKS FOR INSTALLER
1. Ensure that all wiring is routed away from tubing and sheet
metal edges to prevent rub-through or wire pinching.
2. Ensure that all wiring and tubing is secure in unit before
adding panels and covers.
3. Tighten service valve stem caps to 1/12 turn past finger tight.
4. Leave Owner’s Manual with owner. Explain system operation
and periodic maintenance requirements outlined in manual.
°F
°F
°F
°F
°F
°F
SUB-COOLING CHART FOR UNITS WITH TXV
WARNING
DO NOT USE R-22 SERVICE EQUIPMENT OR
COMPONENTS ON R-410A REFRIGERANT EQUIPMENT.
FAILURE TO FOLLOW THIS WARNING COULD RESULT
IN PERSONAL INJURY OR EQUIPMENT DAMAGE.
R-410A Refrigerant Precautions
• R-410A refrigerant operates at much higher pressure
than R-22 refrigerant
• Only use service equipment and replacement
components designed to operate with R-410A
refrigerant
• Recovery cylinder service pressure rating must be 400
psig, DOT 4BA400 or DOT BW400
• Hose pressure rating must be 700 psig
• Manifold set ratings should be 700 psig high side and
180 psig low side
• Leak detectors should be designed to detect R-410A
refrigerant
• R-410A refrigerant systems should be charged ONLY with
liquid refrigerant
• Only use liquid line filter driers with rated working
pressures above 600 psig
• R-410A refrigerant is only compatible with POE oils
• POE oils absorb moisture rapidly. Do not expose oil
to atmosphere.
• Use only TXV rated for use with R-410A refrigerant
8
4
C
,
4
2
C
6
3
C
,
0
3
C
0
6
C
,
2
4
C
,
8
1
C
6
8
10
12
14
16
18