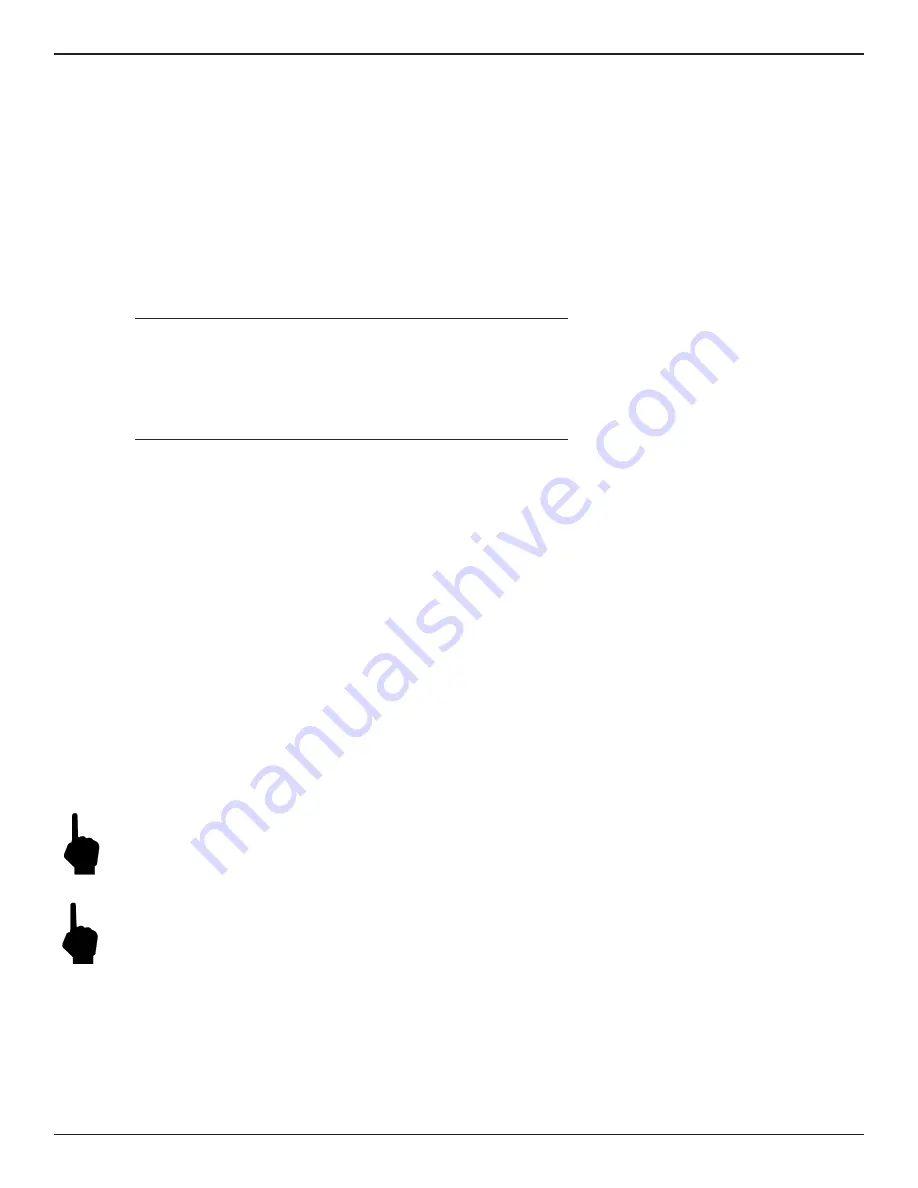
FLT93 Flow Switch Series
FLUID COMPONENTS INTERNATIONAL LLC
Doc. No. 06EN003312 Rev. D
7
This page is subject to proprietary rights statement on last page
When using the instrument for both level and temperature applications, the temperature signal can be as
much as 50
°
F (28
°
C) high when the sensing element is in still air.
Turn the heater off for temperature only applications. To turn off the heater remove the heater control
jumper from the heater wattage control. The jumper may be stored on the control circuit by plugging it
across J12 and J14. Placing the jumper here will not turn on the heater.
Ensure that the instrument has been properly installed. Apply power to the instrument and allow fifteen minutes for the
sensing element to become active and stabilize.
Establish the normal or expected temperature. Remove the enclosure cover to allow access to the control circuit.
Perform either the detecting increasing temperature or detecting decreasing temperature procedure shown below.
Detecting Increasing Temperature (high temperature alarm)
If the status LED is off, turn the alarm adjustment potentiometer clockwise until the LED turns on. With the LED on,
slowly turn the potentiometer counterclockwise one half turn past the point at which the LED just turns off. The
potentiometer may have up to one-quarter turn of hysteresis, therefore, if the mark is overshot, the procedure should be
repeated.
Detecting Decreasing Temperature (low temperature alarm)
If the status LED is on, turn the set point adjustment potentiometer counterclockwise until the LED turns off. With the
LED off, slowly turn the potentiometer clockwise one-half turn past the point at which the LED just turns on. The
potentiometer may have up to one-quarter turn of hysteresis, therefore, if the mark is overshot, the procedure should be
repeated.
Adjustment by Measurement (Option 2)
Air/Gas Flow Applications
1. Remove the instrument's enclosure cover.
2. Ensure the configuration jumpers on the control circuit are correct for this application. See tables on page 4.
3. Check to make sure the input power jumpers match the power to be applied to the instrument. See the power input
table on page 4.
4. Apply power to the instrument. Verify the yellow LED is on and allow the instrument fifteen minutes to
warm-up.
5. Verify the mode switch is in the RUN position.
6. Attach a DC voltmeter to the P1 terminal block with the positive (+) lead to position one and the negative (-) lead to
position two.
Note:
The terminal block can be unplugged from the control circuit to facilitate easy connections. The terminal
block is used in late production instruments. Early production instruments used a mating cable and
connector. If a cable and connector are required use FCI part number 015664-01 to order.
7. Establish the normal process flow condition and allow the signal to stabilize.
Note:
The output signal at connector P1 will vary inversely with changes in the process flow rate. The output
signal level is relative to the type of process media being measured and the heater wattage setting. See flow
application figure on page 5.
8. Record the normal flow signal value.
Normal Flow Signal = ________ volts DC
9. Follow either the Detecting Decreasing Flow or the Detecting Increasing Flow procedure for each flow application
alarm.