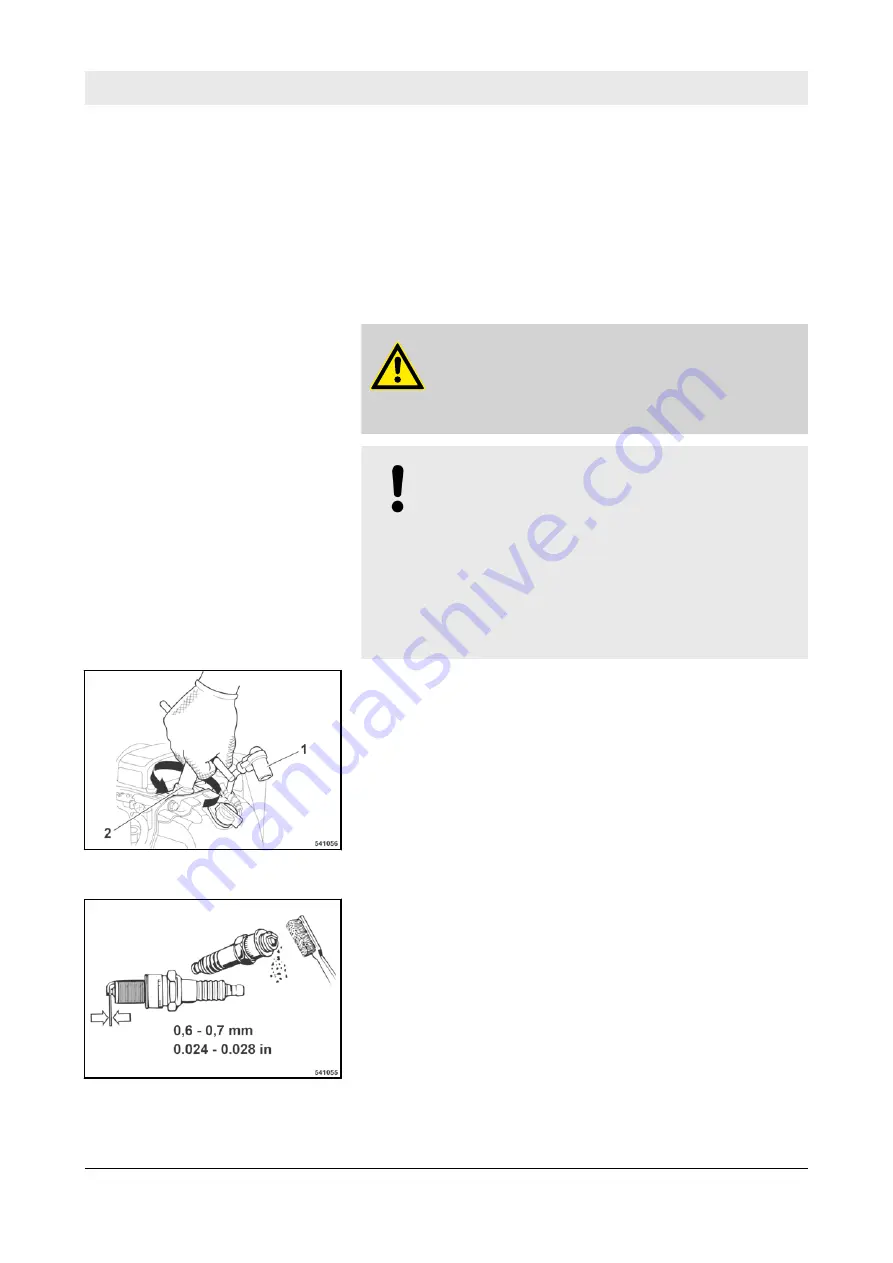
Push the oil dipstick (1) back in.
Perform a test run, inspect the drain plug for leaks and check
the oil level.
6.7.2 Cleaning, checking the spark plug, replacing if necessary
WARNING!
Danger of burning!
Let the engine cool down for approx. 15 minutes
before unscrewing the spark plug.
NOTICE!
In case of excessive combustion residues or burned
off electrodes replace the spark plug.
Do not use spark plugs with incorrect heat value. An
incorrect spark plug can cause damage to the engine.
Recommended spark plugs:
NGK: CR5HSB
Denso: U16FSR-UB
Pull off the spark plug socket (1)
Unscrew the spark plug using a 5/8 inch spark plug spanner.
Check the spark plug
Fig. 42 visually and clean it if neces-
sary.
Check the electrode gap with a feeler gauge, if necessary
adjust the gap to 0.6 - 0.7 mm (0.024 - 0,028 in).
Fig. 40
Fig. 41
Fig. 42
Maintenance
BT 60 / BT 65
53
Go to
Discount-Equipment.com
to
order your parts