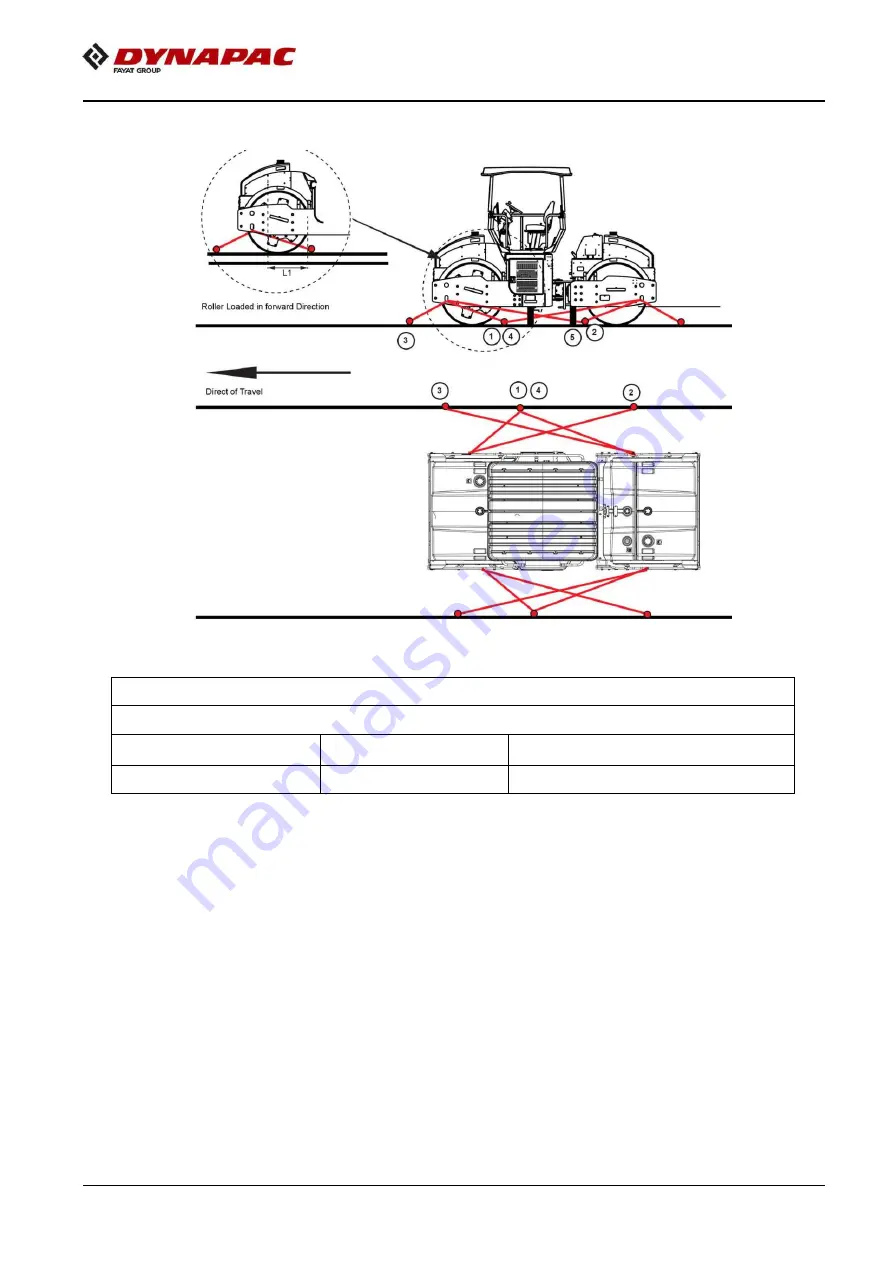
Inspections and Operations
50
Figure 6-15: Securing the Vibratory Roller For Transport
Table 6-1:Lashings' Permitted Distance
The lashings' permitted distance interval in meters
(1 - 4: Double lashings, LC at least 1.7 tonnes (1700 daN), STF 300 kg (300daN))
Double L
1
- L
2
Double L
3
- L
4
0,6 - 3,0
0,1 - 3,0
The distance L
1
above is between points D and E. D is the projected point directly at right angles
laterally in relation to the edge of the platform from the lashing mount C on the roller. E is the lashing
mount at the edge of the platform. L
2
– L
3
have a corresponding relationship.