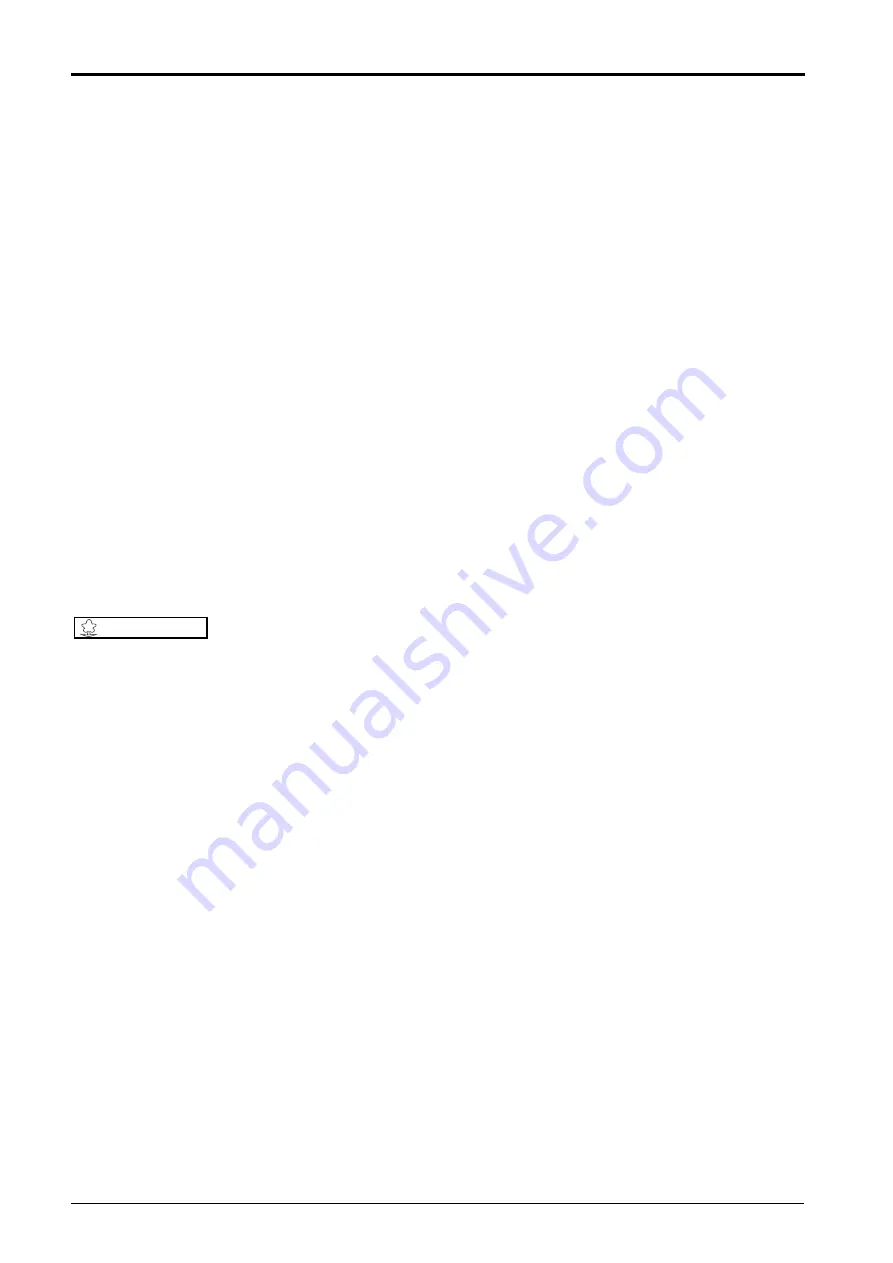
3.1
General notes on maintenance
BOMAG
40
008 921 54
3.1
General notes on maintenance
When performing maintenance work always comply
with the appropriate safety regulations.
Thorough maintenance of the machine guarantees far
longer safe functioning of the machine and prolongs
the lifetime of important components. The effort need-
ed for this work is only little compared with the prob-
lems that may arise when not observing this rule.
The terms right/left correspond with travel direction
forward.
l
Always clean machine and engine thoroughly be-
fore starting maintenance work.
l
For maintenance work stand the machine on level
ground.
l
Always remove the main battery switch for all main-
tenance work.
l
Perform maintenance work only with the motor
switched off.
l
Relieve hydraulic pressures before working on hy-
draulic lines.
l
Before working on electric parts of the machine dis-
connect the battery and cover it with insulation ma-
terial.
Environment
During maintenance work catch all oils and fuels
and do not let them seep into the ground or into
the sewage system. Dispose of oils and fuels en-
vironmentally.
Keep used filters in a separate waste container
and dispose of environmentally.
Catch biodegradable oils separately.
Notes on the fuel system
The lifetime of the diesel engine depends to a great
extent on the cleanliness of the fuel.
l
Keep fuel free of contaminants and water, since this
will damage the injection elements of the engine.
l
Drums with inside zinc lining are not suitable to
store fuel.
l
When choosing the storage place for fuel make
sure that spilled fuel will not harm the environment.
l
Do not let the hose stir up the slurry at the bottom of
the drum.
l
The fuel drum must rest for a longer period of time
before drawing off fuel.
l
The rest in the drum is not suitable for the engine
and should only be used for cleaning purposes.
Notes on the performance of the engine
On diesel engines both combustion air and fuel injec-
tion quantities are thoroughly adapted to each other
and determine power, temperature level and exhaust
gas quality of the engine.
If your engine has to work permanently in "thin air" (at
higher altitudes) and under full load, you should con-
sult the customer service of BOMAG or the customer
service of the engine manufacturer.
Notes on the cooling system
Prepare and check coolant with highest care, since
otherwise the engine may be damaged by corrosion,
cavitation and freezing.
The coolant is prepared by mixing a cooling system
protection agent (ethylene glycol) into the coolant.
Mixing with cooling system protection agent is neces-
sary in all climatic zones. It prevents corrosion, lowers
the freezing point and raises the boiling point of the
coolant.
Notes on the hydraulic system
During maintenance work on the hydraulic system
cleanliness is of major importance. Make sure that no
dirt or other contaminating substances can enter into
the system. Small particles can produce flutes in
valves, cause pumps to seize, clog nozzles and pilot
bores, thereby making expensive repairs inevitable.
l
If, during the daily inspection of the oil level the hy-
draulic oil level is found to have dropped, check all
lines, hoses and components for leaks.
l
Seal external leaks immediately. If necessary in-
form the responsible customer service.
l
Do not store drums with hydraulic oil outdoors, or at
least under a cover. Water can be drawn in through
the bunghole when the weather changes.
l
We recommend to use the BOMAG filling and filter-
ing unit with fine filter to fill the system. This ensures
finest filtration of the hydraulic oil, prolongs the life-
time of the hydraulic oil filter and protects the hy-
draulic system.
l
Clean fittings, filler covers and the area around such
parts before disassembly to avoid entering of dirt.
l
Do not leave the tank opening unnecessarily open,
but cover it so that nothing can fall in.
Summary of Contents for BOMAG BF 800-P Series
Page 2: ...Find manuals at https best manuals com...
Page 7: ...BOMAG 7 008 921 54 1 General Find manuals at https best manuals com...
Page 29: ...BOMAG 29 008 921 54 2 Technical data...
Page 39: ...BOMAG 39 008 921 54 3 Maintenance...
Page 48: ...3 5 Maintenance table BOMAG 48 008 921 54...
Page 49: ...BOMAG 49 008 921 54 4 Engine...
Page 51: ...This as a preview PDF file from best manuals com Download full PDF manual at best manuals com...