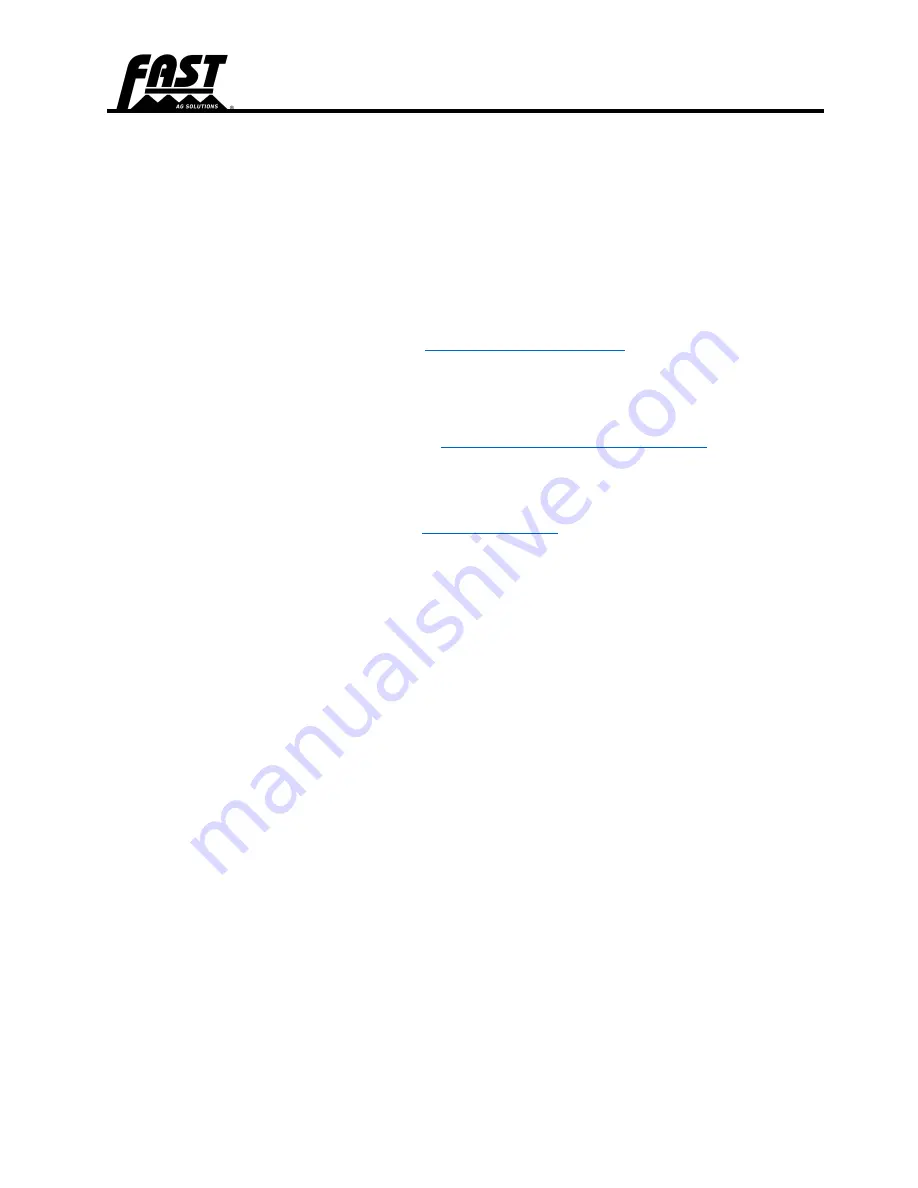
Liquid DuraPlacer DP18L / DP24L
Page ix
Inspections
Pre-Delivery
After the machine has been completely assembled, inspect it to be sure it is in good running order
before delivering it to the customer. Ensure each item is found satisfactory or proper adjustment
to the item(s) is made.
The following checklist is a reminder of points to inspect. It is neither an exclusive nor an
exhaustive list of points to inspect. See the
o
SMV
emblem is installed, protective
shipping tape
is removed from reflectors, and
lights
are installed.
o
All
grease
fittings
Manual.)
o
Inspect to be sure all
nuts
are tightened to proper torque and all
cotter pins
are spread.
o
The
tires
).
o
Wheel bolts
are tightened to their specified torque(s).
o
Fertilizer
row units
are properly adjusted.
o
Warning
lights
are properly installed and operational.
o
All customer-ordered
attachments
are installed or are available for delivery.
o
Any parts scratched in shipment are touched up with
paint
.
o
All
shipping decals
are removed.
o
Transport pins
are inserted in the transport holes.
This machine has been thoroughly checked and to the best of my knowledge is ready for delivery
to the customer.
Signed: _________________________
Date: _________________________
Summary of Contents for DP18L
Page 1: ...DP18L DP24L 40 60 LIQUID DURAPLACER OWNERS MANUAL 2023...
Page 2: ...820046 DP18L DP24L 40 60 Liquid DuraPlacer 2023 07 28...
Page 29: ...SAFETY SAFETY Liquid DuraPlacer DP18L DP24L Page 13 Wing Wing C B A A C B A B A B...
Page 30: ...SAFETY SAFETY Liquid DuraPlacer DP18L DP24L Page 14 Main Frame Wheel and Tracks...