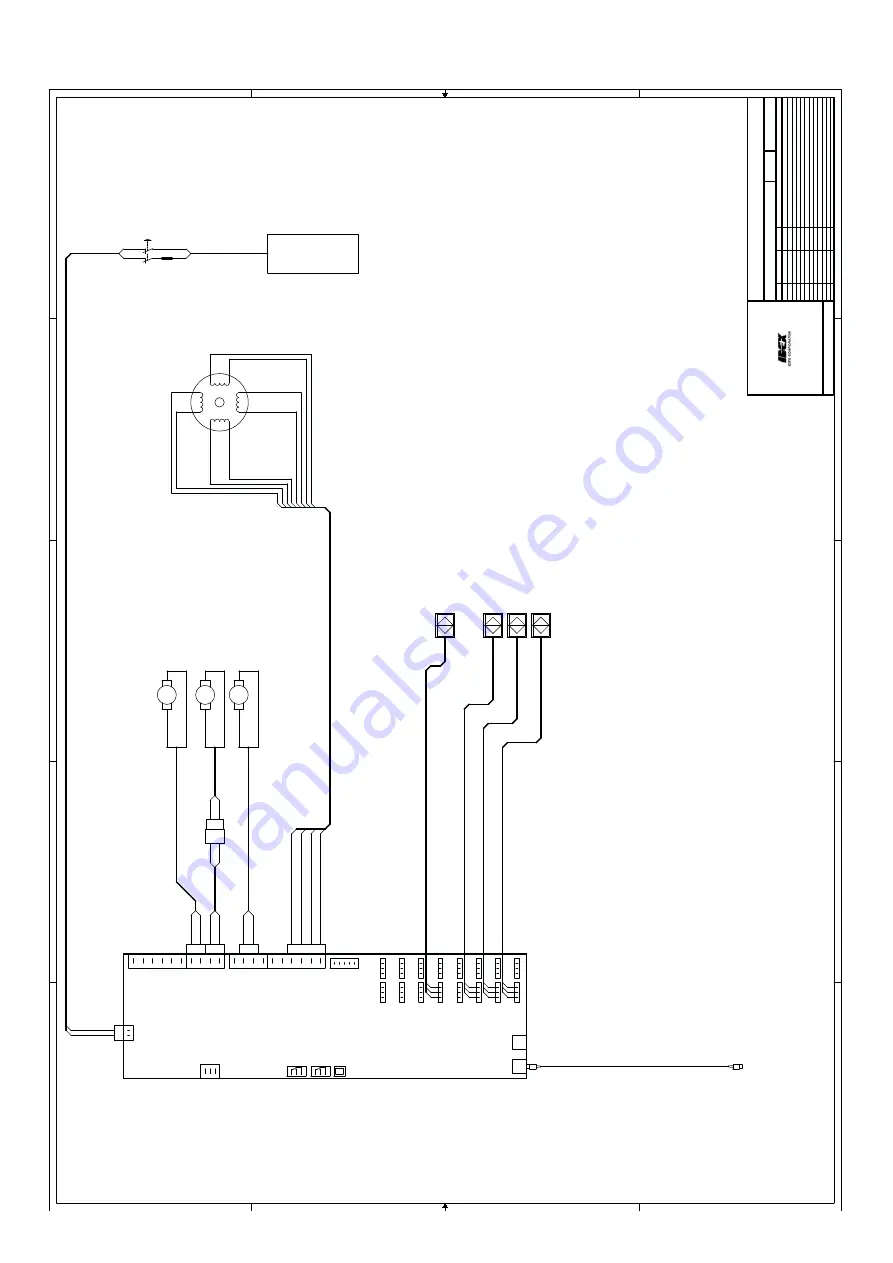
Electrical scheme
5
5
4
4
3
3
2
2
1
1
D
D
C
C
B
B
A
A
+-
-
-
+
+
SENSO
R
1
1861975
M
O
T
O
R
1
(
1
8
61988)
N
E
W
1
814540
SENSOR 4 (1
861978)
NEW: 181
4
5
6
3
SENSOR 6 (1
861980)
NEW: 181
4
5
6
7
SENSOR 2 (1
861976)
NEW: 181
4
5
6
8
CABLE
3
1
1862742
BLUE
BLACK
BROWN
BLUE
BLACK
BROWN
1
2
4
6
12722
3
0
TO RS232 PC
P
O
W
E
R
SUPPLY 24VDC
POWERSUP
P
LY
ASSY 1862749
S
U
PPLY 110/230VAC
50-60Hz, 1Am
ax
M
O
TOR ASSY
18145
4
2
M
O
TOR ASSY
11300
7
1
M
O
TOR ASSY
18145
4
1
CABLE
3
3
1862744
Friday, November
28,
2008
11
TM300
V1.1
0.1
10-3-2008
Nv
B
First
version
Added agit & t
tmotorcable
Remov
ed agitmotor ex
t.
cable
Changed name to 1.1,
change partnmbrs. t
urntablemotor.
1862618.DSN
18-11-2013
1.1
Nv
B
Nv
B
Nv
B
27-6-2008
0.2
28-11-2008
1.0
© 2001 Fluid M
anagem
ent
Hub v
an Doorneweg 31
P
.O.Box
220
2170AE SASSEN
HEIM, The Netherlands
1.1
Revnr.
Sheet
of
Title
Date
Drawn
Remarks
Filename
FLUID
MANAGEME
N
T
V
ersion
BLUE
BROWN
BROWN
BROWN
BLUE
BLUE
0
BROWN
BROWN
BR
OWN
42=
BROWN
BLUE
BLUE
BLUE
BLUE
SHIE
LD
WH
ITE
BLUE
BR
OWN
BLACK & WH
ITE/
ORANGE
or
ORANGE
ORANGE & W
H
IT
E/BLACK
or
BLUE
YELLOW & WH
ITE/
RED
or
YELLOW
RED
& WH
ITE/
YELLOW
or
RED
BLUE
BROWN
GREEN
RED
VALVE M
O
TO
R
M32
AGITATIONMOTOR
M35
TURNT
ABLE
MOTO
R
M33
MGND3
HH
B7
HH
B14
HH
B13
MGND3
HH
B12
HH
B11
HH
B10
HH
B9
HH
B8
MGND2
MGND2
HH
B6
MGND2
MGND1
HH
B5
HH
B4
HH
B3
HH
B2
HH
B1
J19
COMMUNICATION
P
ORT #1
P
ORT #2
P
O
W
ERSUP
P
LY
-
+
-S
+
S
+
-
POWERBOAR
D
2001
LK1
S1
CAN-PRESEN
T
S2
STEPPER-H
O
M
E
S4
VALVE-CLOS
ED
S6
TABLE P
O
SI
T
IO
N
1
2
3
4
M1
4P-STEPPE
R
M
O
TO
R
1
2
3
4
5
6
7
8
17