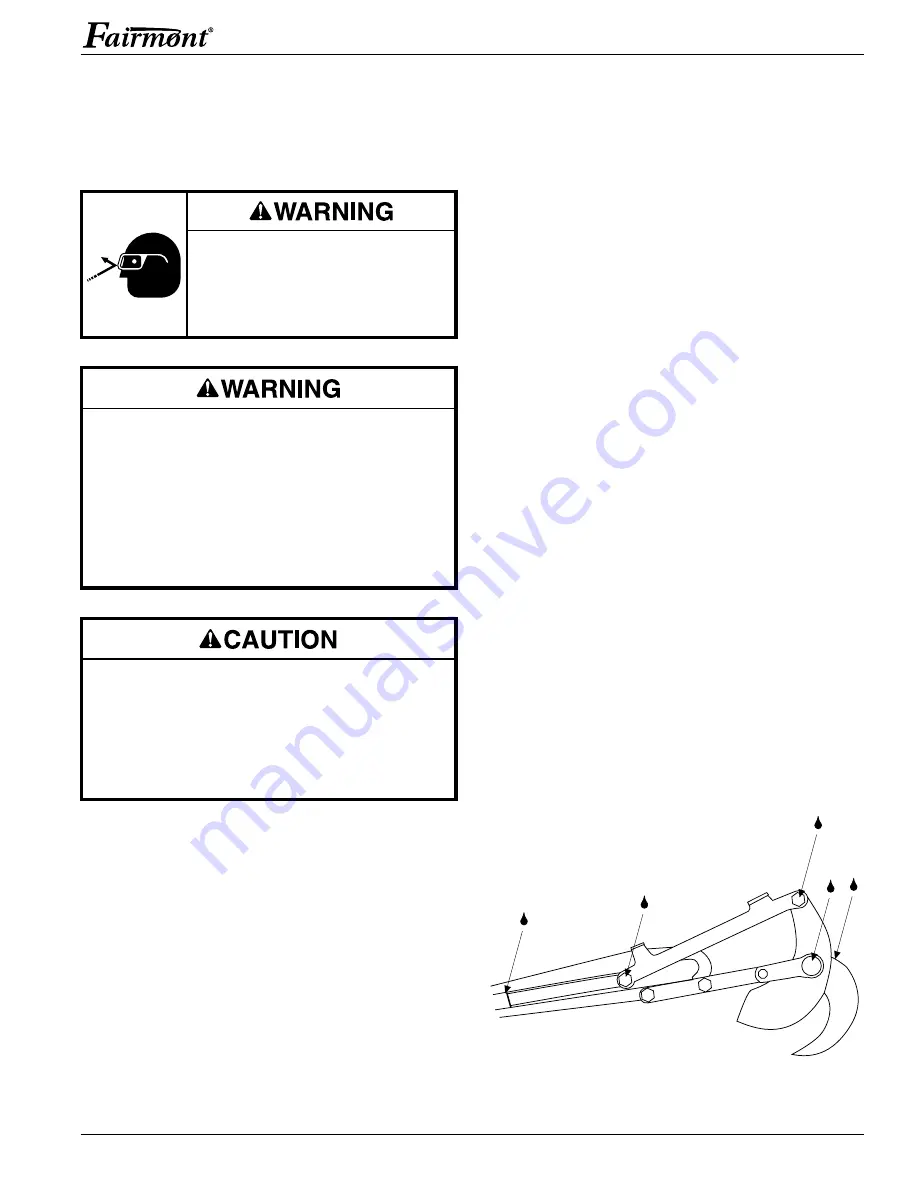
48200, 48520, and 48525 Pruners
Greenlee Textron / Subsidiary of Textron Inc.
5
4455 Boeing Dr. • Rockford, IL 61109-2988 USA • 815/397-7070
Service
The service life of the tool will be maximized by proper
care and maintenance. The maintenance schedule that
follows is recommended.
Maintenance Schedule
Daily
1.
Wipe all tool surfaces clean, especially the fiberglass
extension, of grease, dirt and foreign material. If the
fiberglass extension cannot be wiped clean, use any
approved fiberglass cleaning products.
Do not use solvents or gasoline to clean the
fiberglass extension.
2.
Inspect the cutter unit. Check for wear at the pivoting
and sliding surfaces. Repair blades with nicks or
gouges with a very fine file and a pocket whetstone.
Remove and destroy any cutter blade with
severe cracks, chips, or gouges.
3.
Lubricate the pivoting and sliding surfaces several
times every operating day with 20W or 30W oil.
Apply a heavy coating to these surfaces before
storing.
4.
Several times a day the blade and hook must be
dressed with a pocket whetstone. This keeps the
cutting edge from rolling and chipping.
5.
Make sure the extension tube connector nut and
the cutter mounting bracket bolts are tightened
securely.
6.
Inspect hydraulic system hoses and fittings for signs
of leaks, cracks, wear, or damage.
7.
To prevent contamination, always install dust caps
over couplers when tool is disconnected.
Monthly
Perform a thorough inspection of the hydraulic hoses
and fittings as described in publication 999 3032.3,
SAE J1273 (Hose and Hose Assemblies).
Lubrication
Lubricate the indicated pivoting and sliding surfaces
several times every operating day with 20W or 30W oil.
Apply a heavy coating to these surfaces before storing.
Wear eye protection when operating
or servicing this tool.
Failure to wear eye protection can
result in serious eye injury from
flying debris or hydraulic oil.
• Do not dress the blade or inspect, adjust, or clean
tool when it is connected to a power source.
Accidental start-up can result in serious injury.
• Inspect the blade every operating day. Remove
and destroy the blade if cracks, chips, or gouges
are evident. A damaged blade can break and
strike nearby personnel.
Failure to observe these warnings can result in
severe injury or death.
Inspect hydraulic hoses and couplings every
operating day. Repair or replace if leakage, crack-
ing, wear or damage is evident. Damaged hoses or
couplings can fail resulting in injury or property
damage.
Failure to observe this precaution can result in
injury.
oil