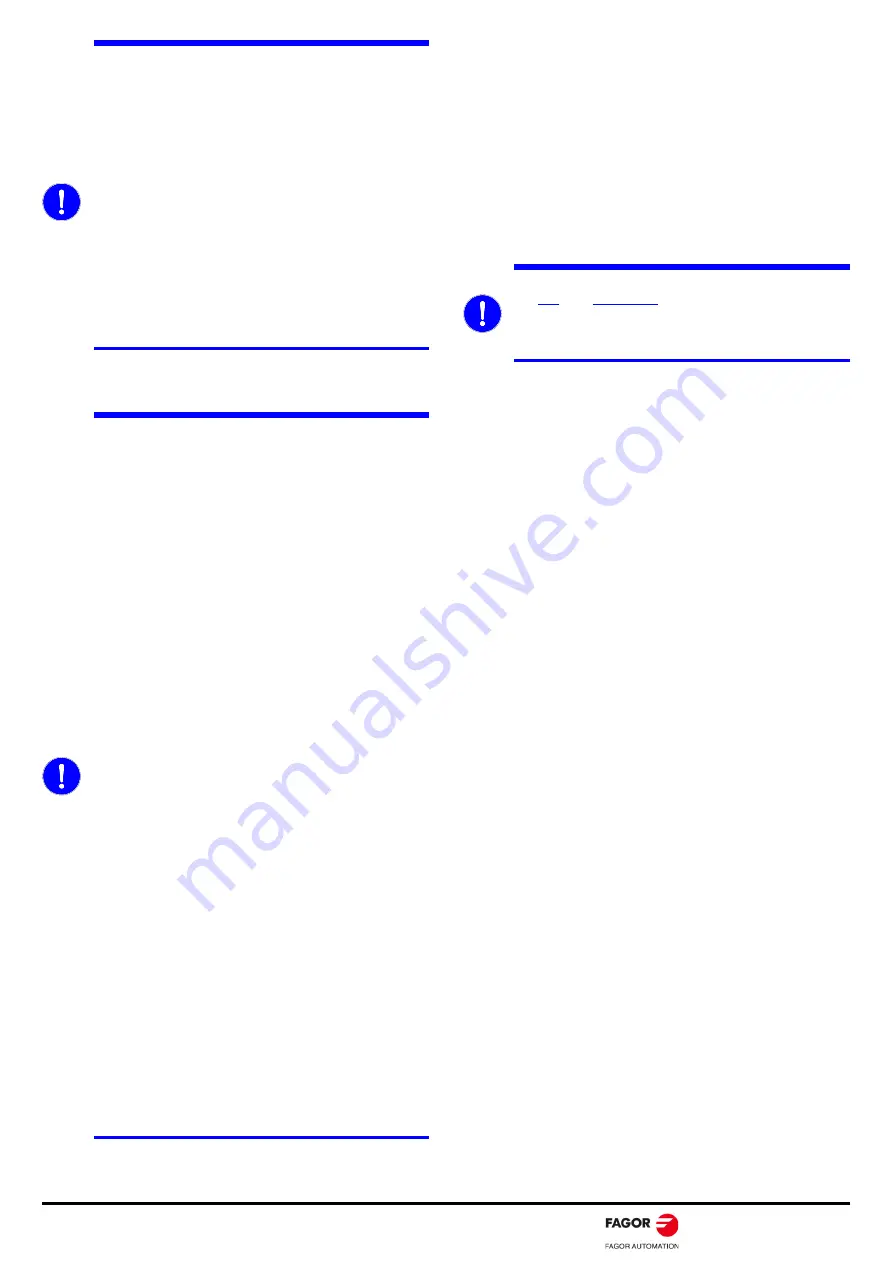
Q
uer
C
us - Power Drive System.
Q
uick
R
eference. Ref.2003
QCQR-23/36
Use equipotential wires in systems with:
Inductive components
Installing the QC-PDS system requires certain
precautions regarding the connection of the inductive
components such as contactors, relays, electrovalves,
motor brakes or, in general, any type of coil.
Thus:
All inductive circuits or components must have their
own interference suppressor that must be installed
as close as possible to the inductive component.
The mentioned interference suppressors will be RC
circuits, varystors or suppressor diodes.
Do not install the excitation cables of the inductive
components and the signal cables in the same
channel, especially when shielded cables are not
available for these signals.
Note: A typical scenario is when using inductive
proximity switches or similar usually connected with
an unshielded cable.
In extreme situations, and if the sensors on the
machine are very sensitive to the interference carried
along the (24 V DC) power supply cables, it may be
necessary to isolate or decouple them from that of
the power supply of the system elements (inductive
components, drives, etc.).
MANDATORY.
It is recommended to separate the cable installation
conduits by at least 20 cm, or make them as short as
possible. Do not install unnecessary cable loops and
use short cables from the central ground point for
connecting to a ground point outside the electrical
cabinet.
Avoid induction loops by choosing common routes
for power, signal and data circuit cables.
Use shielded cables for the power supply and motor.
For shielded cables, the unshielded portion of the
cable used to connect them to the connectors must
be as short as possible in order to reduce radiated
emissions.
Use simple shielding for the motor encoder cable.
The system complies with current regulations
regarding immunity with simple shield.
MANDATORY.
Installations in large areas.
Different voltage sources.
Mains through several buildings reducing the current
in the cable shield and the emissions. Connect to
ground the electrical cabinet, the door, the mounting
plate, with ground straps or cables with a cross
section larger than 10 mm² (AWG 6).
The digital signal wire shielding must be connected
at both ends to a large surface or through a
conductive housing of the connector. This reduces
disturbances that affect the signal cables and also
the emissions.
The analog signal wire shielding must be connected
directly to the device (signal input), reducing the
ground loops due to low frequency disturbances.
Make shield connection on the grounded side of the
equipment when a device does not have a ground
connection.
Do not use the conduits as grounding conductors;
use the ground protection conductor inside the
conduits.
Use cable and ground clamps to connect large areas
of cable shield.
Install a single uncut shielded cable. If a cable must
necessary be cut for the installation, connect it with
the shield connections and through a metal cover at
the cut (joint) point. In the worst case, if it is not
possible to use shielded connectors, keep the
shortest length possible of cable exposed to
interferences, so as to ensure a sound connection
between the shields.
Install switching devices such as contactors, relays
or electro-valves with interference suppression
elements or arc suppressors (e.g. diodes, varistors,
RC circuits).
Install power and control components separately.
Use equipotential cables when having long lines to
reduce the current through the cable shield.
When connecting power cables, the shield of this
cable should be connected to a ground bar.
MANDATORY.
Do not use fly diodes as interference suppression
elements for inductive components. These diodes can
only serve as interference suppressor of the inductance
due to the cabling itself.