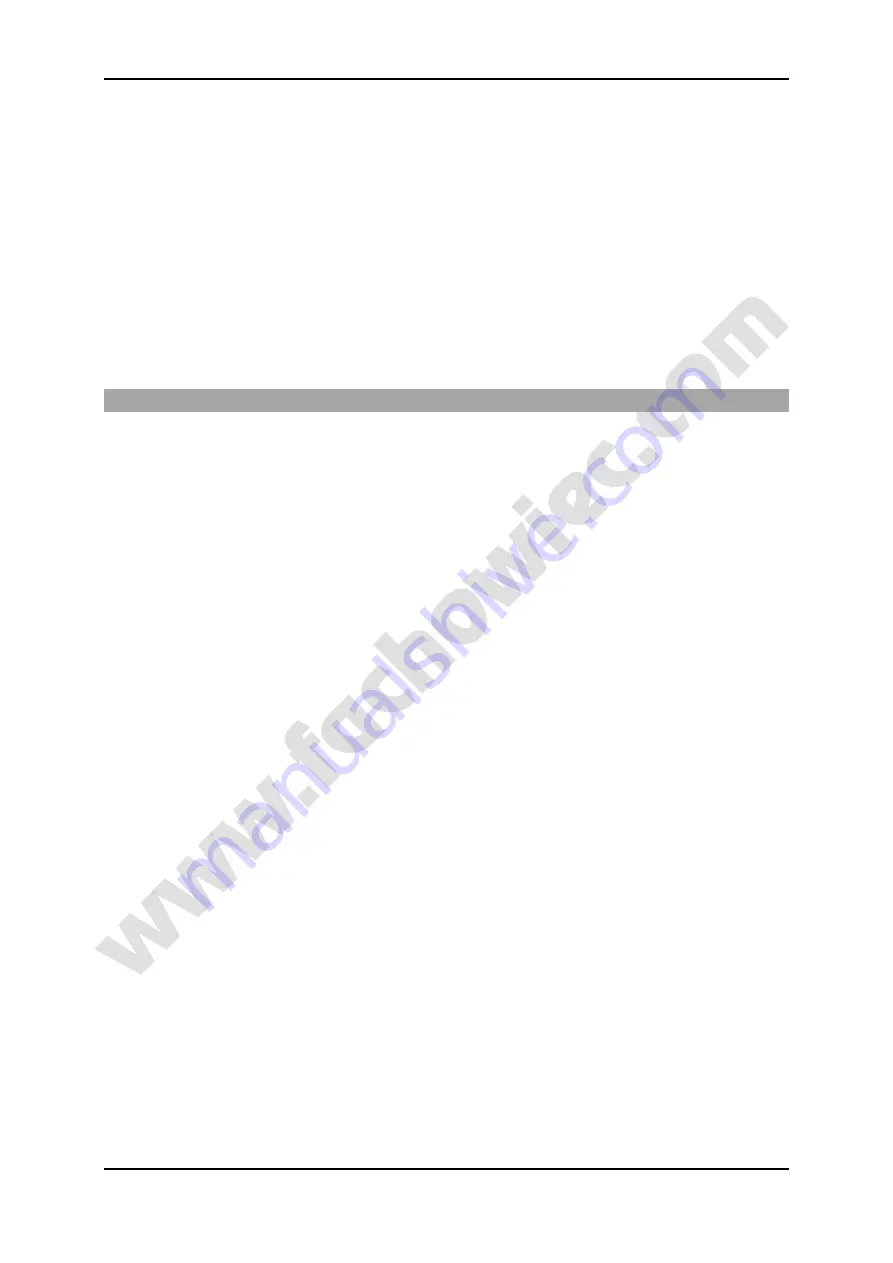
Page
13
with
23
Page
13
with
23
Page
13
with
23
Page
13
with
23
MANUAL - KRAMER Technik MIG / MMA 185
Self-shielded Flux-Cored Welding Wire
This is a method using samoosłonowego core wire for welding (all positions) of normal steel and high
strength exceeding 510 MPa. Samoosłonowy wire can be used in welding processes single and multi-layer
by using current sources of both flat and falling characteristics. The wire is designed for general production
work, also in the field, and for construction welding, where there are no requirements regarding impact.
Welding current: DC (-).
7. CURRENT OPERATING UNIT
7. CURRENT OPERATING UNIT
AND. WORKING CONDITIONS
AND. WORKING CONDITIONS
Optimum ambient temperature range from -10 ° C to 40 ° C.
Avoid welding in conditions of sunlight and the rain, do not allow the water to penetrate into the interior of the device.
Avoid working in the environment of flammable gas, dust and aggressive. Avoid strong winds, which can cause loss of
protection gas.
B. WORK SAFETY
B. WORK SAFETY
Actually the installed device with overvoltage protection, overcurrent protection and overtemperature switches off
automatically under the conditions beyond the defined as the standard. However, long-term use (eg. Surges) can
cause damage to the welder. Therefore, you should follow the instructions listed below:
C. PRECAUTIONS:
C. PRECAUTIONS:
•
They provide good ventilation
Welding is a device through which a large current is flowing, and the natural ventilation does not provide the
necessary cooling. Therefore, to maintain stability, welder equipped with an internal cooling system. The operator
should check if the vent is not blocked. The distance between the welder and the welded object should not be less
than
0,3m. The operator should always pay attention to ventilation devices, since they depend on it not only achieved
welding quality and performance, but also the life of the device.
•
Avoiding overload
The operators should follow (load designated as the maximum permissible load for a given current) or the welding
current exceeds the maximum permissible electric current to the load. Electrical overload can significantly shorten the
life of welders, and even lead to the burning of its elements.