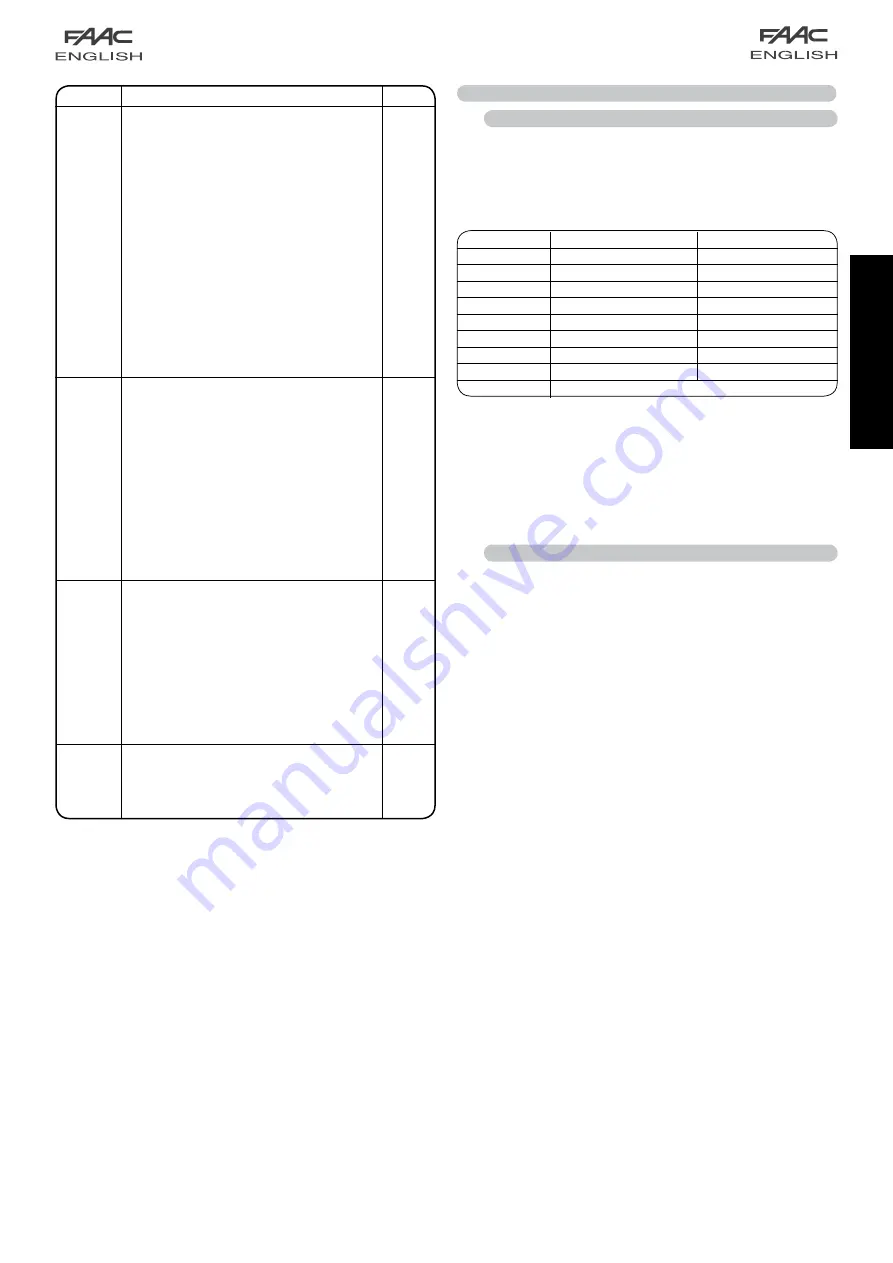
ENGLISH
ASSISTANCE REQUEST (combined with next
function):
If activated, at the end of countdown (settable
with the next function i.e. "Cycle programming")
it effects 2 sec. (in addition to the value already
set with the
PF
function) of pre-flashing at every
Open pulse (job request). Can be useful for setting
scheduled maintenance jobs.
Y
= Active
no
= Disabled
WORK TIME (time-out):
We advise you to set a value of 5 to 10 seconds
over the time taken by the gate to travel from
the closing limit-switch to the opening limit-switch
and vice versa.
Adjustable from
0
to
59
sec. in one-second
steps.
Subsequently, display changes to minutes and
tens of seconds (separated by a point) and time
is adjusted in 10 second steps, up to a maximum
value of
4,1
minutes.
Attention: the set value does not exactly matchthe
motor's maximum operating time, because the
latter is modified according to the performed
deceleration spaces.
Display Function
Default
GATE STATUS:
Exit from programming, data saving, and return
to viewing gate status (see par. 5.1.).
CYCLE PROGRAMMING:
For setting countdown of system operation
cycles. Settable (in thousands) from
00
to
99
thousand cycles.
The displayed value is updated as cycles proceed.
This function can be used to check use of the
board or to exploit the "Assistance request".
NB.:
modification of programming parameters comes into effect
immediately, whereas definitive memory storage occurs only when you
exit programming and return to gate status viewing. If the equipment
is powered down before return to status viewing, all modifications will
be lost.
To restore the default settings of the programming disconnect terminal
strip J1, press the three buttons
+
,
-
,
F
simultaneously and keep them
pressed for 5 seconds.
The table below shows the status of the LEDs in relation to to the
status of the inputs.
Note the following:
L
ed
Lighted
= closed contact
L
ed
off
= open contact
Check the status of the LEDs as per Table.
Operation of the signalling status LEDs
LEDS
LIGHTED
OFF
OP-A
Command activated
Command inactive
OP-B
Command activated
Command inactive
FC
Limit-switch free
Limit-switch engaged
FC
Limit-switch free
Limit-switch engaged
FW OP
Safety devices disengaged
Safety devices engaged
FW CL
Safety devices disengaged
Safety devices engaged
STOP
Command inactive
Command activated
SAFE
Safety devices disengaged
Safety devices engaged
ENC
Flashes while the motor rotates
N.B.:
•The status of the LEDs while the gate is closed at rest are shown
in bold.
•If the Encoder sensor is not installed, the ENC LED is always OFF.
•If you select the reverse opening direction (see par.5.1), the
operation of the limit-switches is also reversed. Therefore, in closed
status, the engaged limit-switch will be FC1 (LED OFF).
When you have made the connections between the
578D equipment and the on-board operator interface
board, and have fitted the travel-limit plates on the rack
(see operator instructions), check opening direction and
limit-switch efficiency, as follows:
•
Power up the system.
•
Select the opening direction (see par.5.1.). If you look
at the gate from the side where the operator is installed,
the opening movement should be from left to right - if
it is, select the standard direction, otherwise select the
reverse direction.
•
Set parameter EC on 00 (see parl.5.2).
•
When you made the modifications, exit programming,
return to inputs viewing and then power down and power
up the system.
•
Release the operator and, sliding the gate manually,
check the efficiency of the limit-switches, controlling the
status LEDs of the inputs (see par.6.1). If you look at the
gate from the side where the operator is installed, the
FC1 LED should go off when the stop position of the left
to right movement is reached, and FC2 should go off
when the stop position of the right to left movement is
reached (also see fig.21).
•
Lock the operator about midway along its travel.
•
Give an OPEN A command and check if the gate moves
in opening direction. If it does not, lock the movement
and, after cutting the power to the system, change over
the wires connected to terminals of MOT-1 and MOT-2.
t
4,1
A5
no
nc
00
St
6 START-UP
6.1 Inputs check
6.2 Installation using sliding gate operators
Summary of Contents for E 578D
Page 1: ...E 578D...
Page 9: ...FC1 FC2 2 1 FC1 FC2 ENGLISH Fig 21 Fig 19 Fig 20...