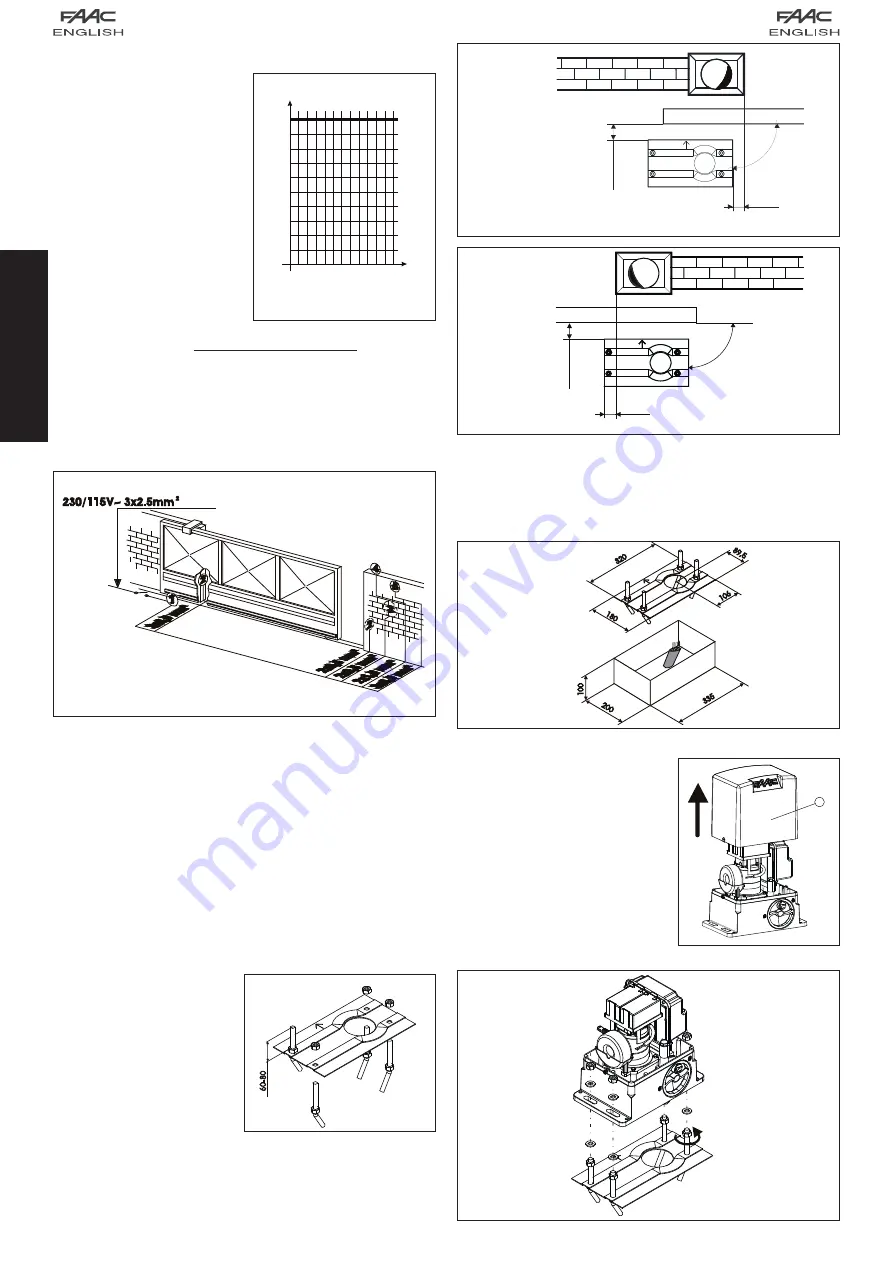
3
% Freq.
Utilizzo
% Fréq.
d’utilisation
% Benutzungs-
frequenz
% Frecuencia
de utilización
% gebruiks-
frequentie
% Duty
Cycle
0
10
20
30
40
50
60
70
80
90
100
1
2
3
4
5
6
7
8
9
10 11 12
Tempo (h)
Time (h)
Temps (h)
Zeit (h)
Tiempo (h)
werktijd (h)
1
90
°
0÷50
5
6
±
5
0÷50
90
°
5
6
±
5
ENGLISH
Fig.03
Fig.04
Fig.05
Fig.06
Fig.07
Fig.08
Fig.09
3. MAXIMUM USE CURVE
The curve makes it possible to establish
maximum work time (T) according to use
frequency (F).
With reference to IEC 34-1 Standard, the
740 gearmotor with an S3 duty, can ope-
rate at a use frequency of 100%.
To ensure efficient operation, it is neces-
sary to operate in the work range below
the curve.
Important:
The curve is obtained at a
temperature of 20°C. Exposure to
the direct sun rays can reduce use
frequency down to 20%.
Calculation of use frequency
Use frequency is the percentage of
effective work time (o closing)
compared to total time of cycle (opening
+ c pause times).
Calculation formula:
Ta
+
Tc
% F =
X 100
Ta + Tc + Tp + Ti
where:
Ta = opening time
Tc = closing time
Tp = pause time
Ti = time of interval between two complete cycles
5. INSTALLING THE AUTOMATED SYSTEM
5.1. Preliminary checks
To ensure safety and efficiency of the automated system, make sure the following
requirements are observed before installing the system:
• The gate structure must be suitable for automation. The following are necessary
in particular: wheel diameter must be in proportion to the weight of the gate,
an upper track must be provided, plus mechanical travel stops to prevent the
gate derailing.
• The soil must guarantee a perfect stability of the foundation plinth.
• There must be no pipes or electric cables in the plinth excavation area.
• If the gearmotor is located in the vehicle transit or manoeuvre area, adequate
means of protection should be provided against accidental impact.
• Check if an efficient earthing is available for connection to the gearmotor.
5.2. Masonry for foundation plate
1- Assemble the foundation plate as shown in figure 04.
2- In order to ensure that the pinion and rack engage correctly, the foundation pla-
te must be positioned as shown in Fig. 05 (right closing) or Fig. 06 (left closing).
Warning: The arrow on the foundation plate must always point to the gate, see
Figs. 05-06.
3- After determining the position of the foundation plate, make a plinth as shown in
Fig. 07 and wall the plate, providing several sheaths for routing the cables. Using
a spirit level, check if the plate is perfectly level. Wait for the cement to set.
4- Lay the electric cables for connection to the accessories and power supply as
shown in diagram of Fig. 03. To facilitate connections to the control unit, allow the
cables to protrude by at least 50 cm from the hole on the foundation plate.
5.3. Mechanical installation
1- Remove the cover, Fig. 08 ref. 1.
2- Position the operator on the foundation
plate, using the supplied washers and nuts
as shown in Fig. 09. During this operation,
route the cables through the appropriate
openings in the motor body (See Fig.01
ref.9). If necessary, the two holes can be
joined using a hammer to obtain a wider
space.
3- Adjust the height of the gearmotor and
the distance from the gate, referring to
dimensions in Fig. 10.
Attention: This operation is necessary to
ensure the rack is correctly secured and
to enable any new adjustments.
Values are expressed in mm
Values are expressed in mm
1- Operator with unit
2- Photocells
3- Key-operated push button
4- Flashing lamp
5- Radio receiver
Values are expressed in mm
Values are expressed in mm
4. ELECTRICAL SET-UP (standard system)