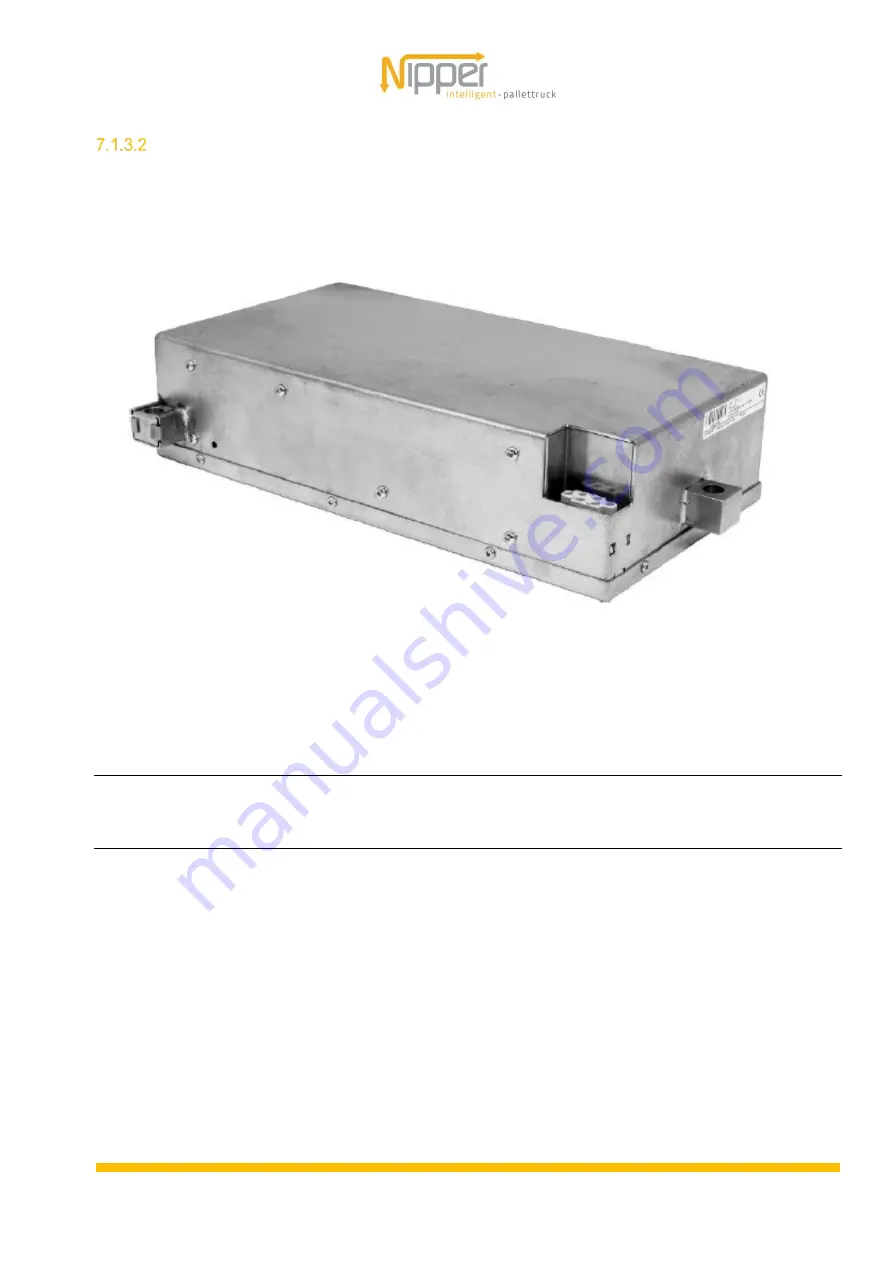
INSTALLATION INSTRUCTIONS NIPPER - JULY 2020
22
LiFePO4 battery pack
The Nipper V2 is attached with two (2) separate -LiFePO4- battery packs with a nominal power of 420 W/h.
Figure 9: W420AH battery pack
Note:
The battery must be stored with 30% charge. If the battery has been stored for more than six months, it
must be fully discharged and then recharged to 30%.
Attention:
Attention is paid to the GDV brochure about loss prevention of the German Insurance Industry.