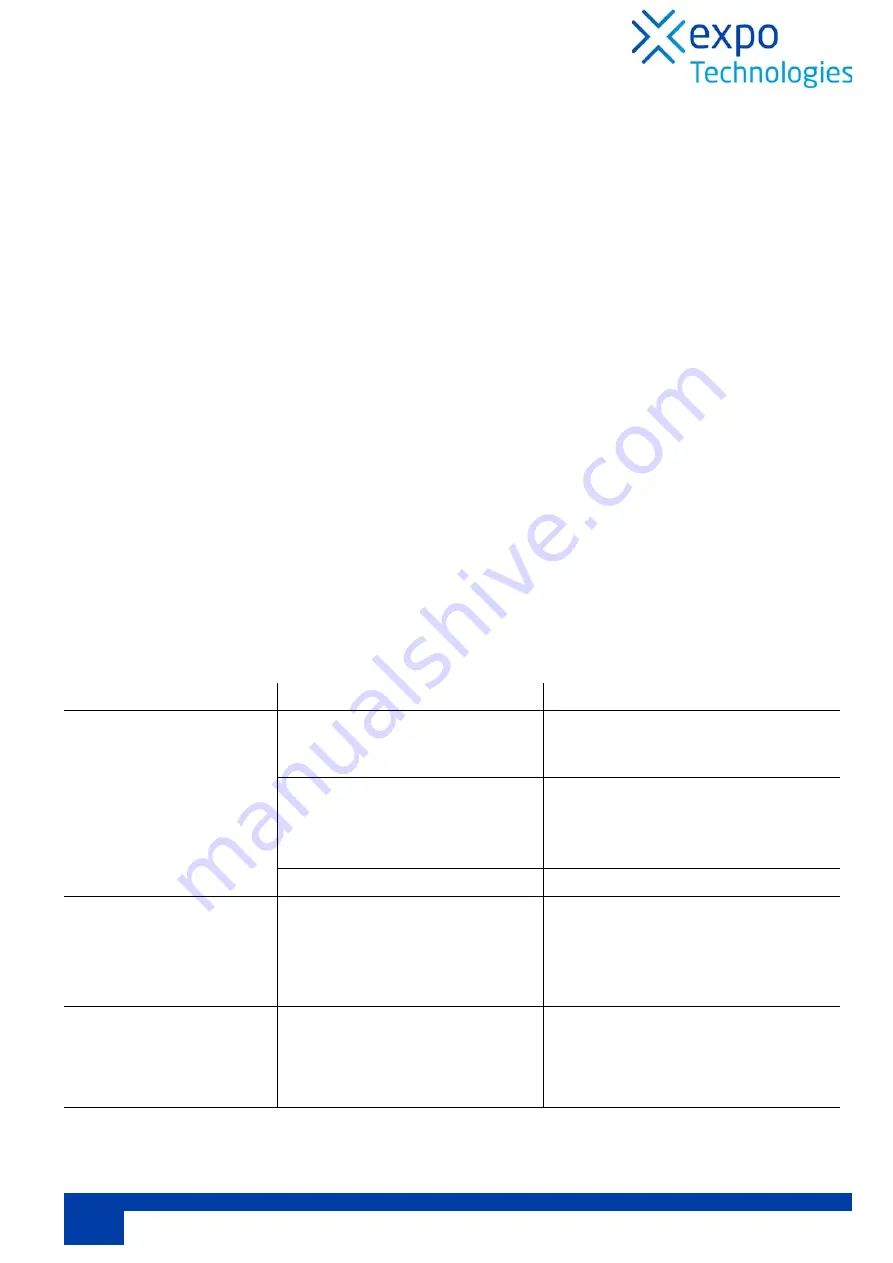
Page
17
ML488 | v19
Expo Technologies UK
T: +44 (0) 20 8398 8011
Expo Technologies US
T: +1 (440) 247 5314
Expo Technologies China
T: +86 532 8906 9858
Section 9: Fault Finding
General Information
If you are having problems that cannot be corrected using one of the methods described, please call Expo or
your supplier for further assistance. If the system is less than 12 months old, parts under warranty should be
returned to Expo for investigation. A full report of the fault and the system serial number should accompany
the parts.
It is common for problems with the MiniPurge
®
system to be caused by contamination of the air supply with
oil, water, or dirt. To prevent these problems, the air supply must contain a dust filter and a water filter. This
will ensure that the air is instrument quality and protect both the purge system and the equipment being
purged. This filtration system is not provided by Expo and must be sourced separately.
Contamination can enter the system from a number of sources. To prevent this, it is essential that the
procedures described in the Installation section are carried out prior to first use of the system. These
procedures should also be carried out following any disconnection and re-connection of the pipe work. Failure
to perform these procedures may cause damage to the system that will not be covered by the warranty.
The system has been designed for ease of fault finding and many of the components fitted are plug-in or
chassis mounted. Check components by substitution only after establishing that such action is necessary.
Before carrying out the fault finding procedures, ensure that:
• Both the main air pressure to the system and for Motor Purge Systems, the regulated pressure to the logic
manifold are as specified on the settings sheet.
• Air pressure does not drop below the minimum supply pressure during purging; most faults reported are
due to insufficient air supply during the purge cycle.
System purges correctly but trips and auto re-purges at the end of the purge time.
This is a result of the pressure within the pressurized enclosure being below the minimum pressure sensor
setting. The pressure can be checked using a manometer. The most common causes of this problem are
outlined below.
Fault Location
Cause
Solution
Pressurized Enclosure
There is debris on the face of the
Relief Valve disk held in place by
the magnet.
• Remove debris and ensure RLV disk
is clean.
Enclosure leaking excessively.
• Ensure all doors and covers are
closed and that all conduit and
cable glands are properly sealed.
• Seal any other leaks.
Pressure sensing tube damaged.
• Replace tubing.
CLAPS Regulator
The CLAPS Regulator setting is
too low.
• Increase the setting of the CLAPS
regulator to raise the pressure in
the pressurized enclosure after
purging.
• To do this, turn clockwise.
MiniPurge
®
Control Unit
the Minimum Pressure Sensor
setting has drifted above the
CLAPS setting
The Minimum Pressure Sensor needs
re-calibrating.
• Refer to Re-calibration of Pressure
Sensors in the Maintenance section