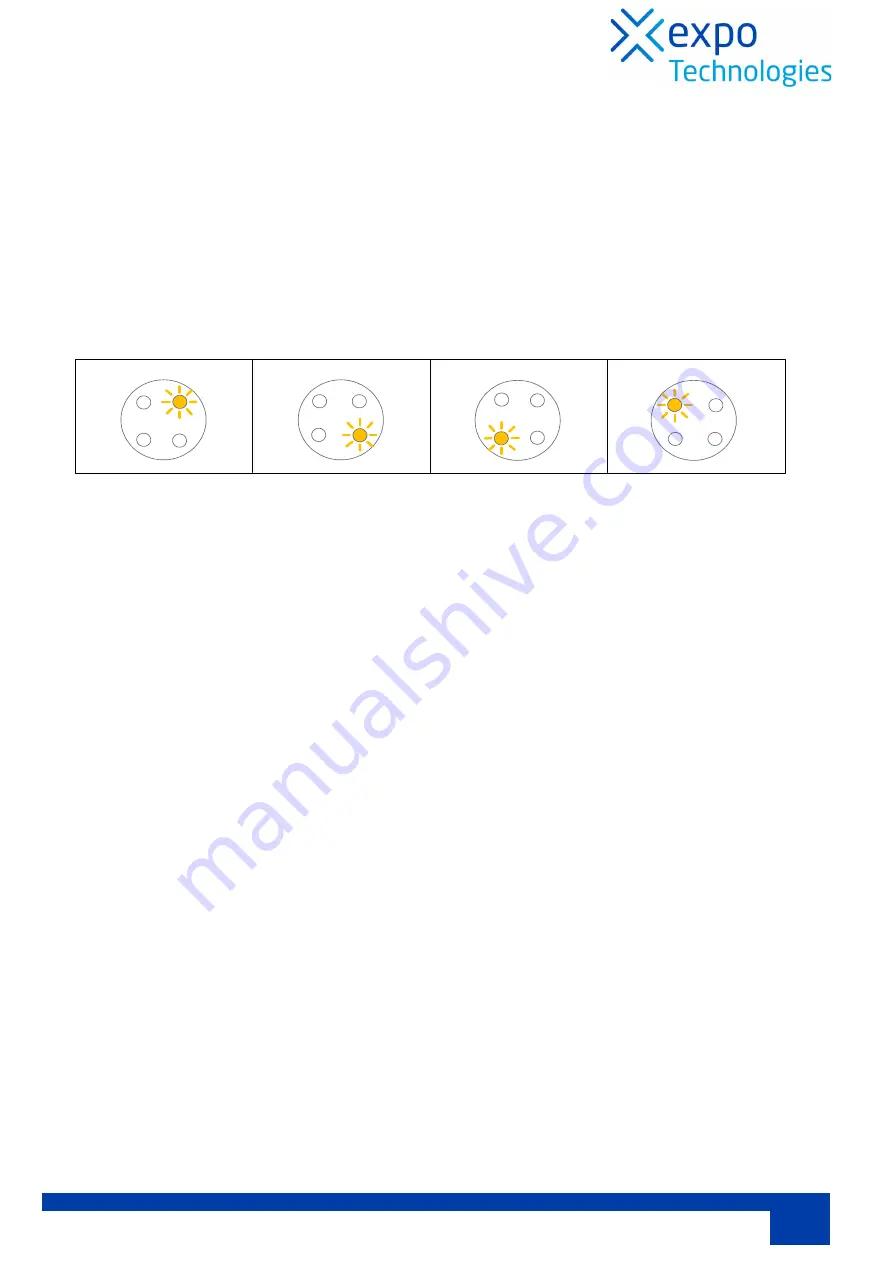
ML548_ES | v3
Page
8
Expo Technologies UK
T: +44 (0) 20 8398 8011
E: [email protected]
Expo Technologies US
T: +1 (440) 247 5314
E:[email protected]
Expo Technologies China
T: +86 532 8906 9858
E: [email protected]
High Pressure Sensor
This sensor monitors the pressure inside the pressurized enclosure. When the pressure reaches the pressure
setting, this sensor sends a signal to cut the pilot signal operating the volume booster until the pressure falls
below the setting of the sensor.
Electronic Purge Timer
When both the enclosure pressure and the purge flow rate are correct, the Purge Flow Sensor activates the
timer and the electronic timer starts. The timing period is selected using switches mounted on the timer
module.
Note: Setting the timer to 00 minutes will cause infinite purging; the cycle will never complete.
During timing, the percentage of the purge cycle is indicated by four LEDs which flashes sequentially while
the timer is running.
The Electronic Timer is powered by an EPPS (Electro-Pneumatic Power Supply.) Supply air must be available
for the EPPS to operate.
EPPS (Electro-Pnuematic Power Supply)
The EPPS is a flameproof/explosion proof and dust-tight module, which uses a limited amount of air from the
logic system to generate sufficient intrinsically safe power to drive the Electronic Timer.
When the Electronic Timer is powered by an EPPS up to 30 seconds delay is expected once the flow sensor
signal is received for the timer to start.
Purge Complete Valve
This valve receives a signal from the purge timer that indicates the completion of the purge cycle and verifies
that the pressurization signal is still present. If both conditions are satisfied a signal is sent to indicate that
the purge is complete. This performs two functions: to turn on the electrical supply to the pressurized
enclosure and to reduce the high purge flow rate to leakage compensation mode. It also provides a hold-on
signal that maintains the leakage compensation mode with the power switch on, even when the purge timer
has reset ready for the next purge cycle.
OR Gate
This device provides the Purge Complete Valve with the hold-on function referred to previously. When either
the timed-out signal or the purge complete signal is present it allows the pilot signal to be sent to the purge
complete valve.
Alarm Only Circuit (/AO)
If the pressure in the pressurized enclosure is too low the system will normally cut off electrical power to it. In
certain circumstances, where local codes of practice allow, the system can be altered to provide a hold-on
circuit that will maintain the electrical power supply to the pressurized enclosure while also providing a
pressure failure alarm. The user must respond to the alarm and either restore the pressure to the pressurized
enclosure or otherwise make the installation safe; for example, cut off the electrical supply. The decision to
use the Alarm Only facility, and the allowable length of time for non-pressurized operation, is the responsibility
LED 1
LED 2
LED 3
LED 4
LED 1
LED 2
LED 3
LED 4
LED 1
LED 2
LED 3
LED 4
LED 1
LED 2
LED 3
LED 4
0 to 25%
of purge time
26 to 50%
of purge time
51 to 75%
of purge time
76 to 100%
of purge time