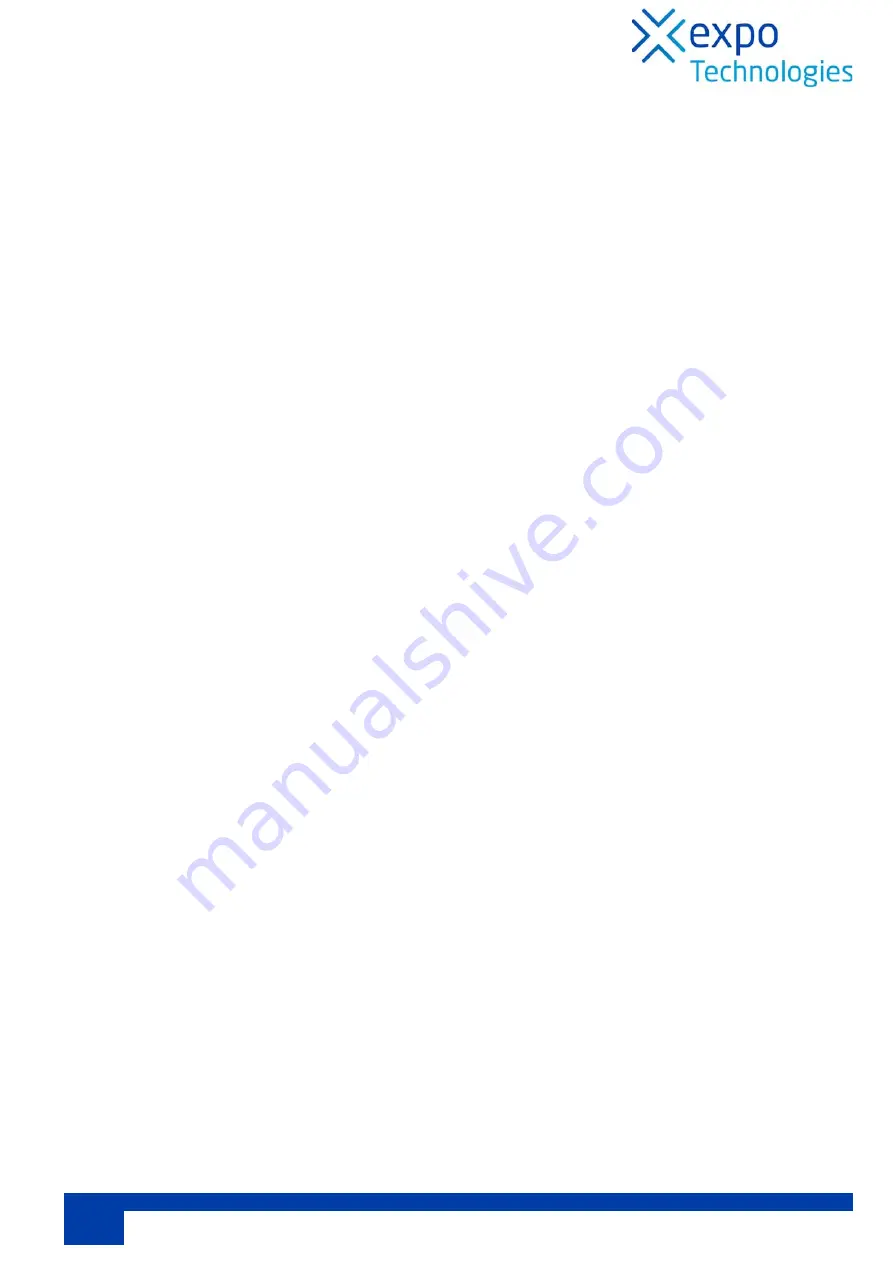
Page
11
ML548 | v11
Expo Technologies UK
T: +44 (0) 20 8398 8011
Expo Technologies US
T: +1 (440) 247 5314
Expo Technologies China
T: +86 532 8906 9858
Section 6: Installation of the System
The MiniPurge
®
is designed for use under normal industrial conditions of ambient temperature, humidity and
vibration. Please consult Expo before installing this equipment in conditions that may cause stresses beyond
normal industrial conditions.The MiniPurge
®
system must be installed by a competent person in accordance
with relevant standards, such as IEC / EN 60079-14, and any local codes of practice.
The MiniPurge
®
control unit should be installed either directly on, or close to the pressurized enclosure. It
should be installed such that the system indicators and certification labels are in view.
All parts of the system carry a common serial number. If installing more than one system, ensure that this
commonality is maintained within each system installed.
Relief Valve Unit
To achieve effective purging, the points where air enters and exits the pressurized enclosure should normally
be at opposite ends of the enclosure. The RLV unit must be mounted vertically and there should be a minimum
clearance of 300 mm (12") around the spark arrestor (purge outlet).
It is important that the interior and exterior of the spark arrestor is kept clean and debris is not allowed to
accumulate; this might affect the calibration of the device. In particular, the exterior of the spark arrestor
should not be painted or blocked in any way.
Air Supply Quality
The MiniPurge
®
system should be connected to a protective gas supply, which is suitable for purging and
pressurization.
The supply pipe connection to the MiniPurge
®
must be appropriate for the maximum input flow rate for the
application.
The air supply must be regulated at a pressure less than the maximum stated inlet pressure.
The air supply must be: clean, non-flammable and from a non-hazardous location. The air should be of
Instrument Air Quality. Although the purge control system will operate with lower air quality, its operational
life will be adversely affected. The equipment that is being protected by the MiniPurge
®
may also suffer
because of poor air quality.
With reference to BS ISO 8573-1: 2010, Instrument Air is typically specified as:
Particle Class 1
In each cubic metre of compressed air, the particulate count should not exceed 20,000 particles in the 0.1 to
0.5 micron size range, 400 particles in the 0.5 to 1 micron size range and 10 particles in the 1 to 5 micron size
range.
Humidity or pressure dew point
The dew point, at line pressure, shall be at least 10 °C below the minimum local recorded ambient temperature
at the plant site. In no case, should the dew point at line pressure 3 °C.
Oil Class 2
In each cubic metre of compressed air, not more than 0.1mg of oil is allowed. This is a total level for liquid oil,
oil aerosol and oil vapour.
When an inert gas is being used to supply the purge system, risk of asphyxiation exists. Refer to Application
Suitability section.
Summary of Contents for D760-ET MiniPurge
Page 32: ......
Page 33: ......
Page 34: ......
Page 35: ......
Page 36: ......
Page 37: ......
Page 38: ......
Page 39: ......
Page 40: ......
Page 41: ......
Page 42: ......
Page 43: ...2...
Page 44: ...2...
Page 45: ......
Page 46: ......
Page 47: ......
Page 48: ......
Page 49: ......
Page 50: ......