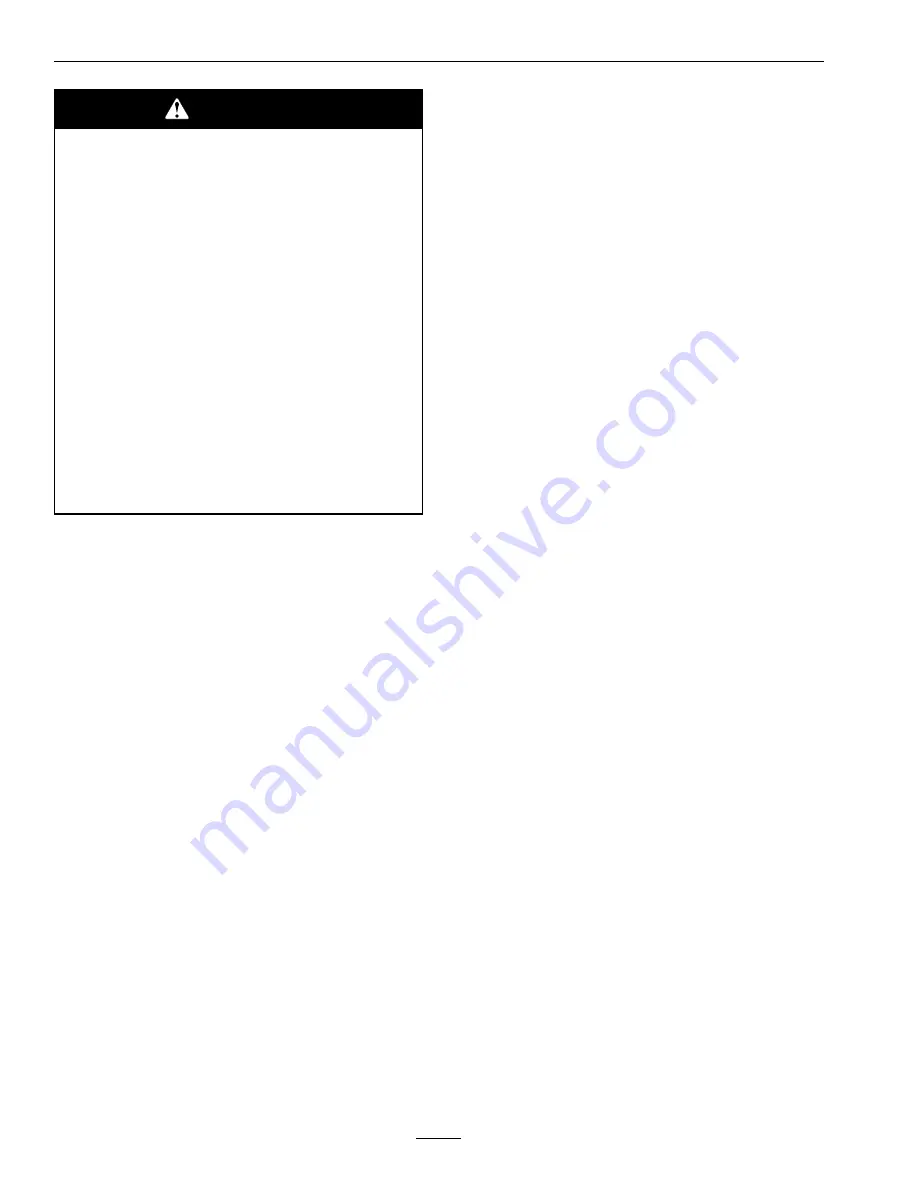
Safety
DANGER
Operating on wet grass or steep slopes can
cause sliding and loss of control. Loss of
control and/or loss of operator’s footing
could result in a fall with an arm or leg
getting under the mower or engine deck
which may result in serious injury, death or
drowning.
•
Mow across slopes, never up and down.
•
Do Not mow slopes when grass is wet.
•
Do Not mow near drop-offs or near water.
•
Do Not mow slopes greater than 20
degrees.
•
Reduce speed and use extreme caution
on slopes.
•
Avoid sudden turns or rapid speed
changes.
•
See inside the back cover to determine the
approximate slope angle of the area to be mowed.
•
Remove or mark obstacles such as rocks, tree
limbs, etc. from the mowing area. Tall grass can
hide obstacles.
•
Watch for ditches, holes, rocks, dips and rises that
change the operating angle, as rough terrain could
overturn the machine.
•
Avoid sudden starts when mowing uphill because
the mower may tip backwards.
•
Be aware that operating on wet grass, across steep
slopes or downhill may cause the mower to lose
traction. Loss of traction to the drive wheels may
result in sliding and a loss of braking and steering.
•
Always avoid sudden starting or stopping on a
slope. If tires lose traction, disengage the blades
and proceed slowly off the slope.
•
Follow the manufacturer’s recommendations for
wheel weights or counter weights to improve
stability.
•
Use extreme care with grass catchers or
attachments. These can change the stability of the
machine and cause loss of control.
Maintenance and Storage
•
Disengage drives, lower implement, set parking
brake, stop engine and remove key or disconnect
spark plug wire. Wait for all movement to stop
before adjusting, cleaning or repairing.
•
Keep engine and engine area free from
accumulation of grass, leaves, excessive grease
or oil, and other debris which can accumulate
in these areas. These materials can become
combustible and may result in a fire.
•
Let engine cool before storing and do not store
near flame or any enclosed area where open pilot
lights or heat appliances are present.
•
Shut off fuel while storing or transporting. Do
Not store fuel near flames or drain indoors.
•
Park machine on level ground. Never allow
untrained personnel to service machine.
•
Use jack stands to support components when
required.
•
Carefully release pressure from components with
stored energy.
•
Use care when checking blades. Wrap the blade(s)
or wear gloves, and use caution when servicing
them. Only replace damaged blades. Never
straighten or weld them.
•
Keep hands and feet away from moving parts.
If possible, do not make adjustments with the
engine running.
•
Keep all guards, shields and all safety devices in
place and in safe working condition.
•
Check all bolts frequently to maintain proper
tightness.
•
Frequently check for worn or deteriorating
components that could create a hazard.
•
All replacement parts must be the same as
or equivalent to the parts supplied as original
equipment.
8
Summary of Contents for Vikingtm Hydro
Page 1: ...VIKING HYDRO For Serial Nos 790 000 Higher Part No 4500 355 Rev A ...
Page 11: ...Safety 103 1798 103 2076 103 2103 103 2196 103 2242 11 ...
Page 12: ...Safety 103 2243 103 4935 103 5626 48 inch Deck Units Only 116 0404 12 ...
Page 40: ...Schematics 40 ...
Page 42: ...42 ...
Page 43: ...43 ...