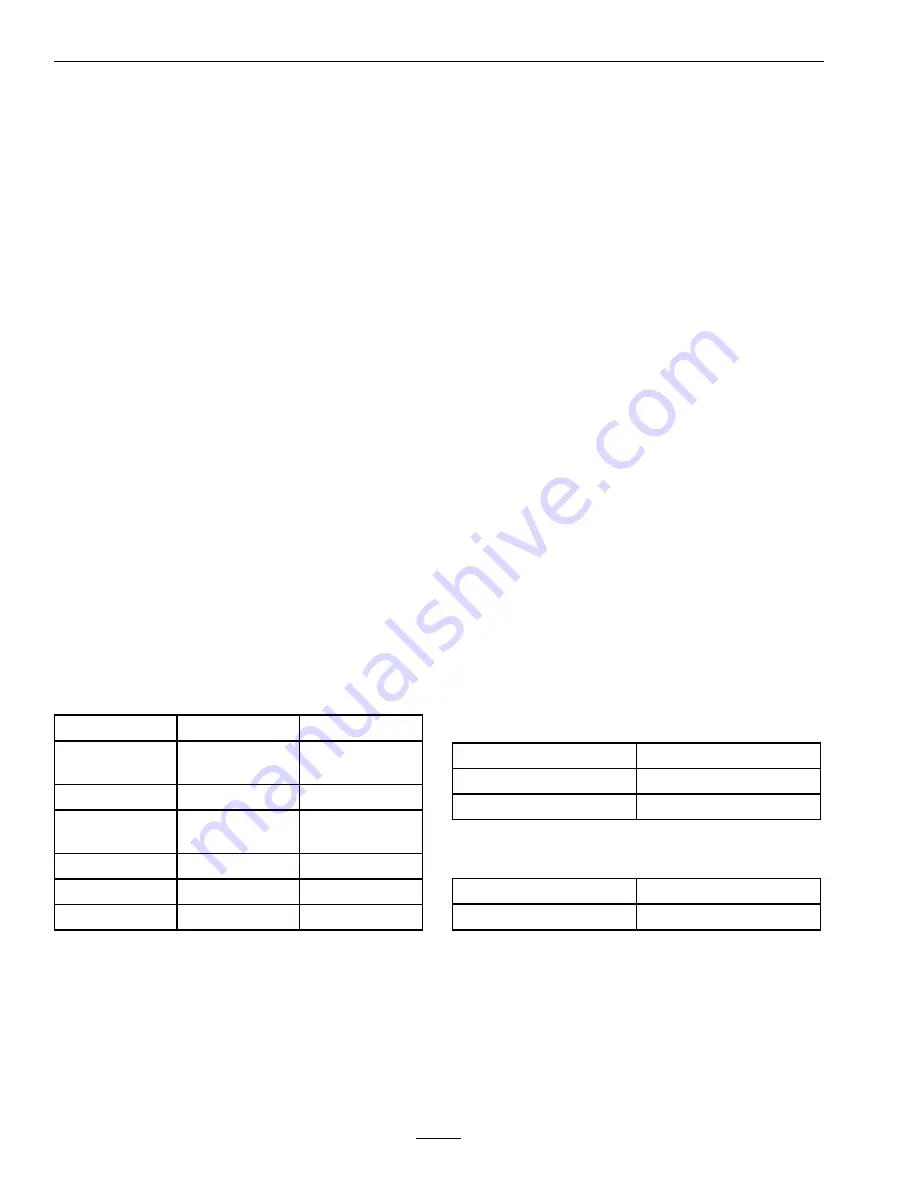
Specifications
– Optional suspension seat: molded adjustable
flip-up armrests.
•
Seat Safety Switch: Incorporated into the
Safety Interlock System. Time delay seat switch
eliminates rough ground cut-outs.
Hydrostatic Ground Drive System
•
Hydrostatic Pumps: Two Hydro Gear variable
displacement piston pumps.
•
Wheel Motors: Two Parker with 1 1/4 inch
tapered shafts.
•
Hydraulic Oil Type: Use Mobil 1 15W-50
Synthetic motor oil.
•
Hydraulic Oil Capacity: 2.1 qt. (2.0 L)
•
Hydraulic Filter: Replaceable cartridge type.
– Summer use above 32°F (0°C)
P/N 109-4180: 25 microns, 10 psi bypass
– Winter use below 32°F (0°C)
P/N 1-523541: 40 microns, 18 psi bypass
•
Speeds:
– 0–9.8 mph (15.8 km/hr) forward.
– 0-6.3 mph (10.1 km/hr) reverse.
•
Drive wheel release valves allow machine to be
moved when engine is not running.
Tires & Wheels
Drive
Front Caster
Pneumatic
(Air-Filled)
Semi-Pneumatic
Quantity
2
2
Tread Size
“Multi- Trac
C/S”
Smooth
Size
24 x 12.00-12
13 x 6.50-6
Ply Rating
4
Pressure
13 psi (90 kPa)
Cutting Deck
•
Cutting Width: 60 inch (152.4 cm)
•
Discharge: Side
•
Blade Size: (3 ea.) 20.50 inches (52.1 cm)
•
Blade Spindles: Solid steel spindles with 1 inch
(25.4 mm) I.D. bearings.
•
Deck Drive:
– Electric clutch mounted on horizontal engine
shaft. “B” Section belt (with self-tensioning
idler) from electric clutch to transfer shaft
mounted on deck.
– Blades are driven by one “B” Section belt
(w/self-tensioning idler) from transfer shaft
on deck to blade spindles.
•
Deck:
Full floating deck is attached to out-front support
frame. Six anti-scalp rollers provide maximum
turf protection. Deck design allows for bagging,
mulching or side discharge.
•
Deck Depth: 5.5 inches (14.0 cm)
•
Cutting Height Adjustment:
An extra-long cushioned lever is used to adjust
the cutting height from 1 1/2 inch (3.8 cm) to 5
inches (12.7 cm) in 1/4 inch (6.4 mm) increments.
The cutting height adjustment handle has a
transport position and all adjustments can be
made while the operator remains seated. Units
also have a foot operated deck lift assist lever to
aid in raising the deck.
•
Mulching Kit: Optional.
Dimensions
Overall Width:
Without Deck
53.5 inches (135.9 cm)
Deflector Up
61.4 inches (156.0 cm)
Deflector Down
72.2 inches (183.4 cm)
Overall Length:
Roll Bar - Up
81.9 inches (208.0 cm)
Roll Bar - Down
92.6 inches (235.2 cm)
16
Summary of Contents for LAZER Z LZ27KC604
Page 12: ...Safety 1 633922 1 643222 1 643339 98 5954 103 1798 103 3270 103 4474 12 ...
Page 13: ...Safety 103 4930 103 5881 103 6319 107 2102 107 2112 13 ...
Page 14: ...Safety 109 1214 109 1215 109 3148 109 7949 103 9255 14 ...
Page 44: ...Schematics Hydraulic Diagram 44 ...
Page 46: ...Service Record Date Description of Work Done Service Done By 46 ...
Page 47: ...47 ...