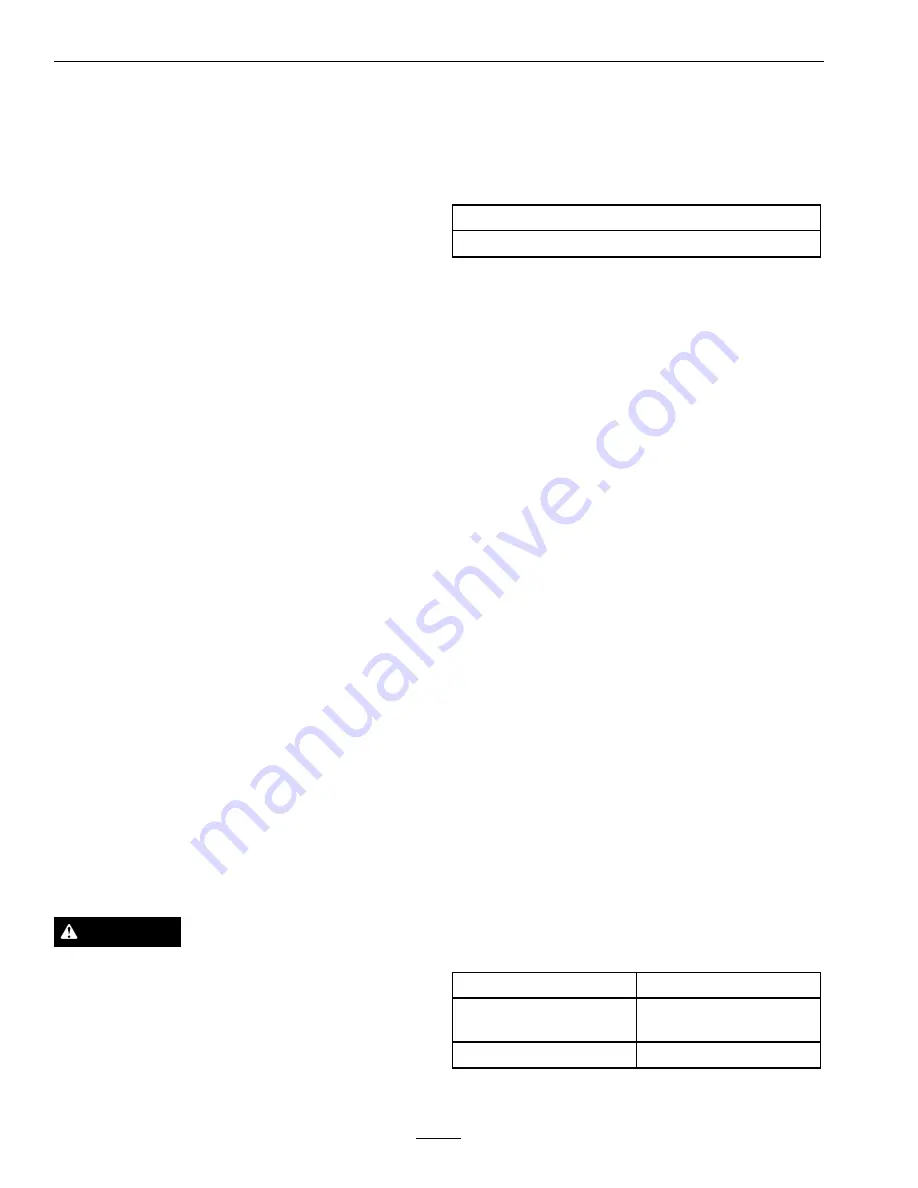
Maintenance
(bushings are located to the inside of the flange
bearings).
Lubricate Motion Control
Bronze Bushings
Service Interval: Every 160 hours
1. Stop engine, wait for all moving parts to stop, and
remove key. Engage parking brake.
2. Unhook seat latch and tilt seat up.
3. Lubricate bronze bushings on flange bearings
securing the motion control arm shafts with a
light oil or a spray type lubricant.
Drain Fuel Filter/Water
Separator
Service Interval: Every 40 hours
1. Stop engine, wait for all moving parts to stop, and
remove key. Engage parking brake.
2. Place a drain pan under the fuel filter and loosen
the drain plug approximately 1 turn.
3. Water should drain.
4. When fuel begins to flow from the filter, tighten
the drain plug.
Important:
Water or other contaminants in fuel
can severely damage fuel pump and/or the other
engine components.
Change Fuel Filter/Water
Separator
Service Interval: Every 400 hours/Yearly
(whichever comes first)
(more often in dirty or
dusty conditions).
DANGER
Use of improper components can result in system
failure, fuel leakage and possible explosion.
•
Ensure that an Authorized Service Dealer
replace the fuel filter and any components for
the fuel system.
•
Use only approved fuel lines, hose clamps
and fuel filters for high pressure systems.
Change Inline Fuel Filter
Service Interval: As required
An inline fuel filter is installed between the fuel tank
and the fuel pump. Replace when necessary.
Replacement Filters
Exmark
P/N 112-7836
Change Hydraulic System
Filter
Service Interval: After the first 250 hours
Every 500 hours/Yearly
(whichever comes
first) thereafter
(Every 250 hours/Yearly if
using Mobil 1 15W50)
Note:
Use only Exmark P/N 103-2146.
1. Stop engine, wait for all moving parts to stop, and
remove key. Engage parking brake.
2. Raise seat.
3. Carefully clean area around filter. It is important
that no dirt or contamination enter hydraulic
system.
4. Unscrew filter to remove and allow oil to drain
from reservoir.
Important:
Before reinstalling new filter, fill
it with Exmark Premium Hydro oil and apply
a thin coat of oil on the surface of the rubber
seal.
Turn filter clockwise until rubber seal contacts the
filter adapter, then tighten the filter an additional
2/3 to 3/4 turn.
5. Fill reservoir as stated in
Check Hydraulic Oil
Level
section.
Exmark Premium Hydro Oil is recommended.
Refer to the chart for an acceptable alternative:
Hydro Oil
Change Interval
Exmark Premium Hydro
Oil (Preferred)
500 Hours
Mobil 1 15W50
250 Hours
36
Summary of Contents for LAZER Z D-SERIES Operators
Page 1: ...LAZER Z D SERIES For Serial Nos 920 000 Higher Lazer Z LZD Units Part No 4500 919 Rev A ...
Page 12: ...Safety 103 0223 103 0261 103 1798 103 2076 103 7218 107 2102 12 ...
Page 13: ...Safety 109 0872 109 1214 109 1215 109 1399 109 2219 109 2263 13 ...
Page 14: ...Safety 109 2264 109 2478 109 2951 109 3148 14 ...
Page 16: ...Safety 19426 87881 19426 87903 107 9866 1 Fast 3 Neutral 2 Slow 4 Reverse 16 ...
Page 52: ...Schematics Schematics Electrical Diagram 52 ...
Page 53: ...Schematics Electrical Schematic 53 ...
Page 55: ...Notes 55 ...
Page 56: ...Notes 56 ...
Page 57: ...Service Record Date Description of Work Done Service Done By 57 ...
Page 58: ...58 ...