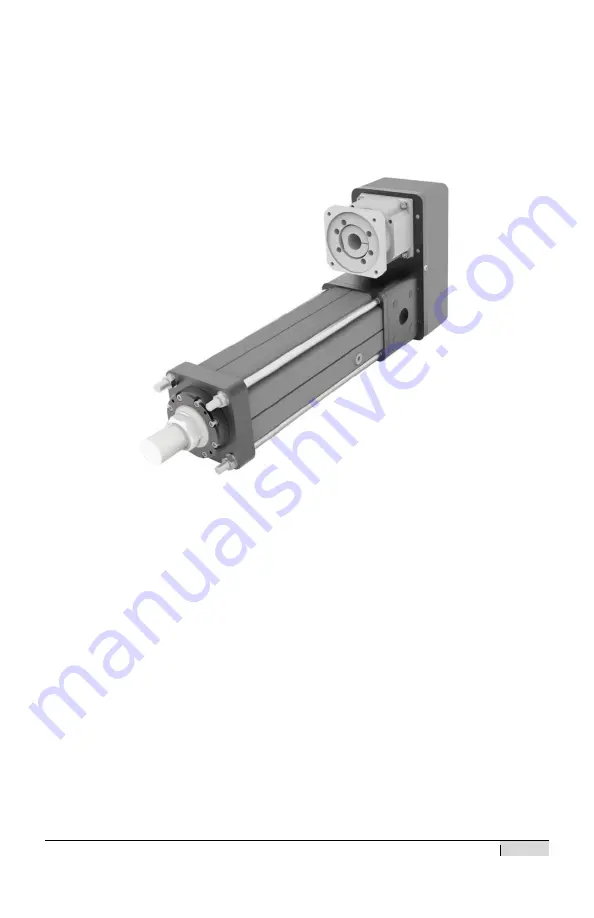
Curtiss-Wright | FTX Series Rev. C PN71855 5/26/17
1
FTX and FTP Series
Installation and Service Manual
Information furnished by Curtiss-Wright, Exlar Corporation, is believed to be accurate and
reliable. However, no responsibility is assumed by Curtiss-Wright for its use. Curtiss-Wright
reserves the right to change the design and operation of the equipment described herein
and any associated motion products that may appear in this document. Information in this
document pertaining to equipment not furnished by Curtiss-Wright should be confirmed by
that equipment manufacturer. Curtiss-Wright assumes no responsibility for changes to
information by other manufacturers or errors in that information or the description of that
information. Information in this document is subject to change without notice.
This document does not contain any export controlled technical data.