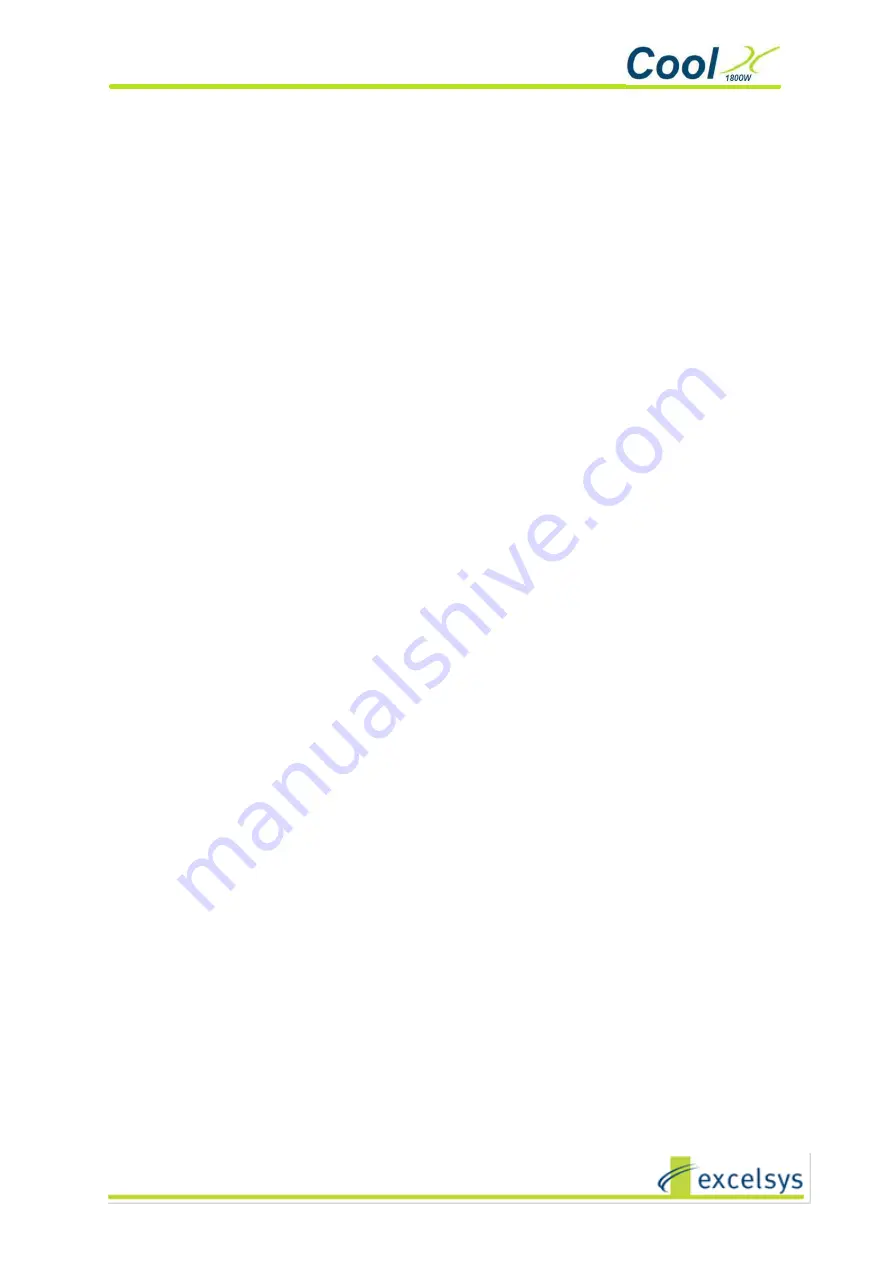
5
Section 3: Configuration Considerations
•
Do not unplug CoolMods while input power is applied to the CoolPac. The CoolMods are
not designed for hot-plug insertion.
•
Always ensure that input and output screw terminals are properly torqued before
applying power to the CoolX
•
Positive and negative power cables should be arranged as a twisted pair to minimise
inductance.
•
Wait 4 minutes after shutting off power before inserting or removing CoolMods.
•
CoolX assemblies do not have user serviceable components. They must be returned to
the factory for repairs. Contact Customer Service for an RMA number before returning
the unit. Do not attempt to repair or modify the power supply in any manner other than
the exchange of CoolMod
s as described in this Designers’ Manual.
•
Use proper size wires to avoid overheating and excessive voltage drop.
•
Take appropriate precautions when touching the CoolX after it has been operating for a
period of time. Due to the excellent conduction cooling methods to the chassis, the
chassis will remain hot for some time after power has been removed.
•
If a CmE or CmF module is to be configured in the CoolX1800, it must be used in Slot 6.
This leaves Slot 1, Slot 2 and Slot 3 free for other modules or another CmE or CmF module.
Summary of Contents for CoolX1800
Page 29: ...29 ...
Page 71: ...71 CoolX1800 2 x Bulk Modules ...