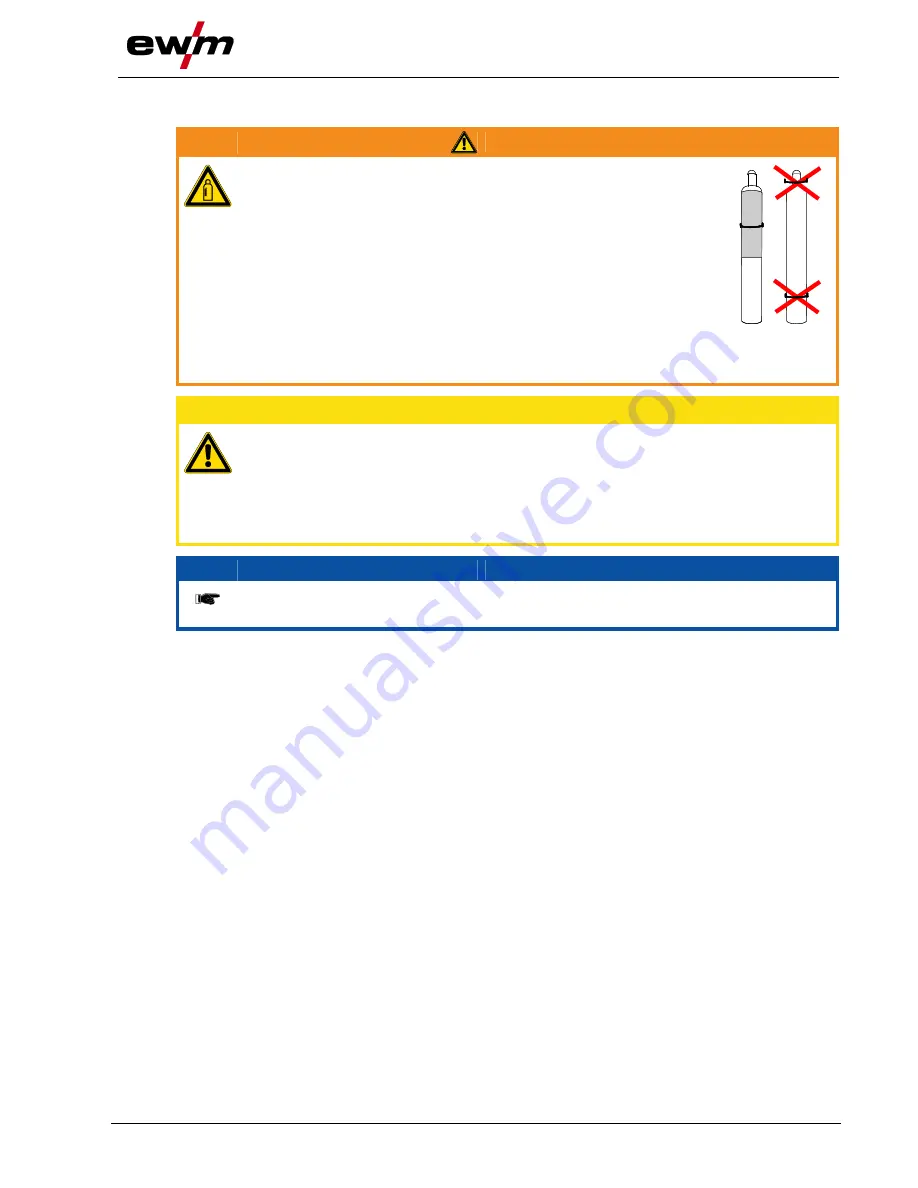
Design and function
Shielding gas supply (shielding gas cylinder for welding machine)
099-004934-EW501
13.06.2013
31
5.8
Shielding gas supply (shielding gas cylinder for welding machine)
WARNING
Risk of injury due to improper handling of shielding gas cylinders!
Improper handling and insufficient securing of shielding gas cylinders
can cause serious injuries!
• Secure shielding gas cylinders using the standard fastening elements on
the unit (chain/belt)!
• The fastening elements must tightly enclose the shielding gas cylinder!
• Attach the fastening elements within the upper half of the shielding gas
cylinder!
• Do not attach any element to the shielding gas cylinder valve!
• Observe the instructions from the gas manufacturer and any relevant
regulations concerning the use of compressed air!
• Avoid heating the shielding gas cylinder!
CAUTION
Faults in the shielding gas supply.
An unhindered shielding gas supply from the shielding gas cylinder to the welding
torch is a fundamental requirement for optimum welding results. In addition, a blocked
shielding gas supply may result in the welding torch being destroyed.
• Always re-fit the yellow protective cap when not using the shielding gas connection.
• All shielding gas connections must be gas tight.
NOTE
Before connecting the pressure regulator to the gas cylinder, open the cylinder valve
briefly to expel any dirt.