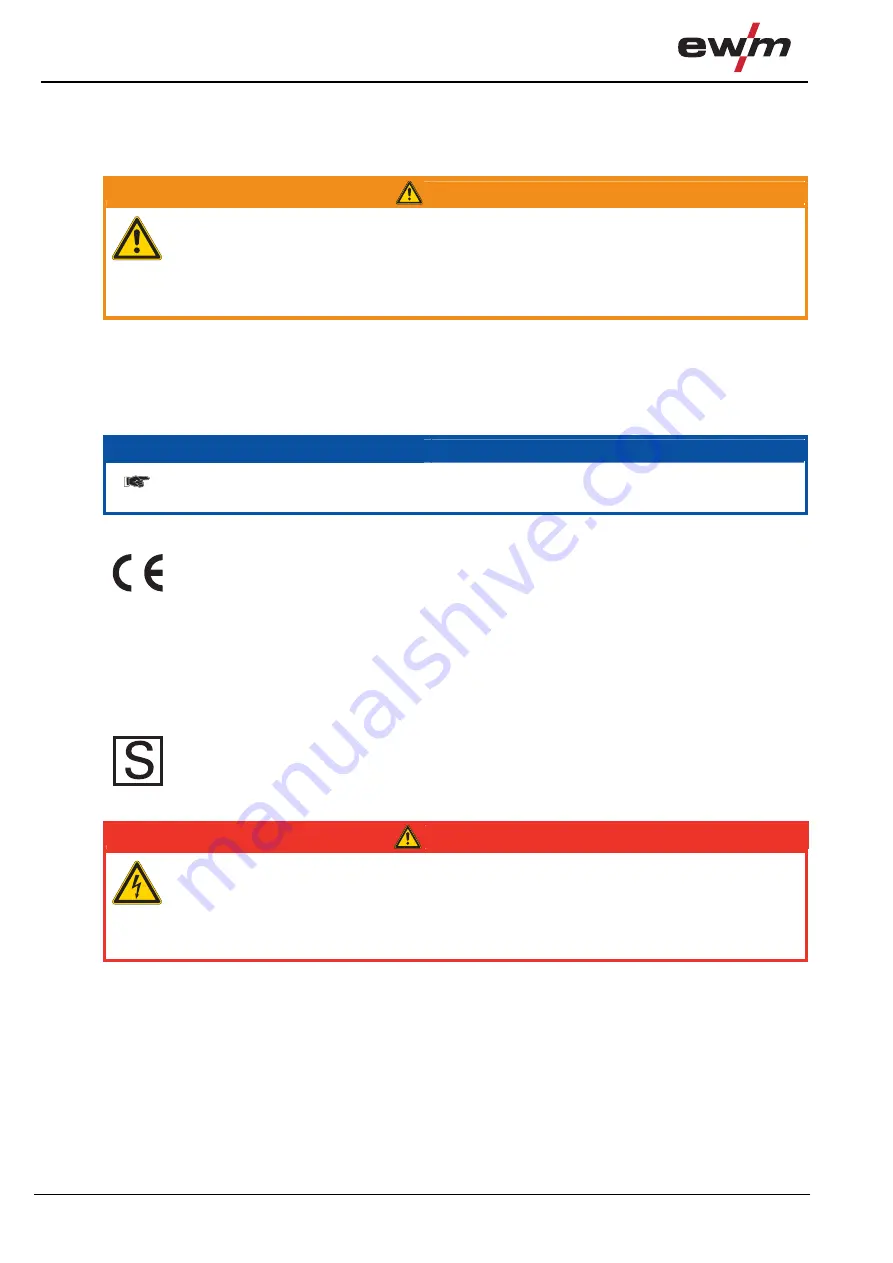
Intended use
Applications
8
099-010253-EW501
26.11.2010
3
Intended use
This machine has been manufactured according to the latest developments in technology and current
regulations and standards. It must only be operated in line with the instructions on correct usage.
WARNING
Hazards due to improper usage!
Hazards may arise for persons, animals and material objects if the equipment is not used
correctly. No liability is accepted for any damages arising from improper usage!
• The equipment must only be used in line with proper usage and by trained or expert staff!
• Do not modify or convert the equipment improperly!
3.1
Applications
This machine is only suitable for the mechanised production of circumferential welds.
3.2
Documents which also apply
3.2.1
Warranty
NOTE
For further information, please see the accompanying supplementary sheets "Machine
and Company Data, Maintenance and Testing, Warranty"!
3.2.2
Declaration of Conformity
The designated machine conforms to EC Directives and standards in terms of its design
and construction:
• EC Low Voltage Directive (2006/95/EC),
• EC EMC Directive (2004/108/EC),
This declaration shall become null and void in the event of unauthorised modifications, improperly
conducted repairs, non-observance of the deadlines for the repetition test and / or non-permitted
conversion work not specifically authorised by the manufacturer.
The original copy of the declaration of conformity is enclosed with the unit.
3.2.3
Welding in environments with increased electrical hazards
In compliance with IEC / DIN EN 60974, VDE 0544 the machines can be used in
environments with an increased electrical hazard.
3.2.4
Service documents (spare parts and circuit diagrams)
DANGER
Do not carry out any unauthorised repairs or modifications!
To avoid injury and equipment damage, the unit must only be repaired or modified by
specialist, skilled persons!
The warranty becomes null and void in the event of unauthorised interference.
• Appoint only skilled persons for repair work (trained service personnel)!
Original copies of the circuit diagrams are enclosed with the unit.
Spare parts can be obtained from the relevant authorised dealer.