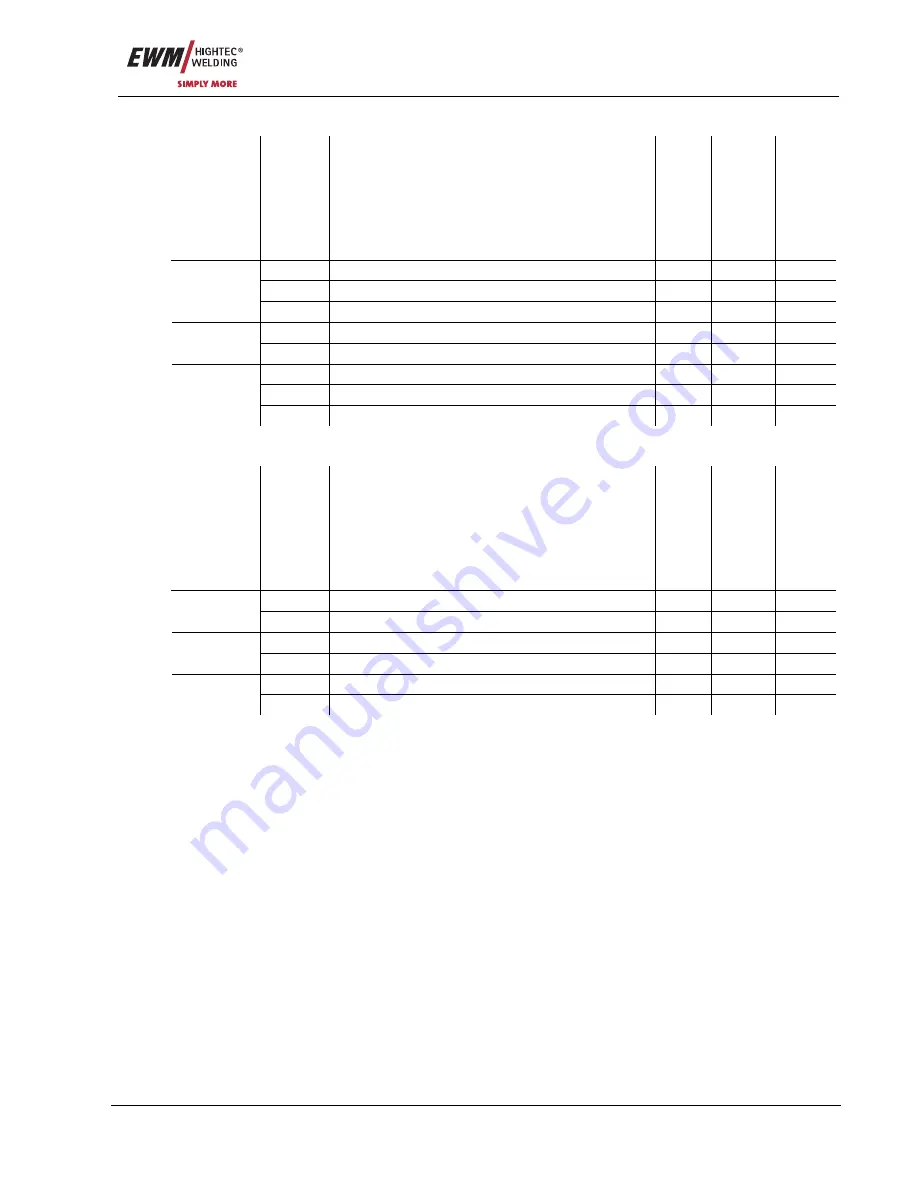
Functional characteristics
TIG welding
Item No.: 099-004877-EWM01
41
Setting instructions for spotArc for CrNi panels
Seam shape
Panel thickn
ess
Pulse type/
welding type
Spot time
Welding curr
ent
Down
-sl
o
p
e
tim
e
1mm Automated
pulses
0.3s
100A
0.5s
1mm
Fast pulsing (2.5kHz)
0.3s
100A
0.5s
Butt weld
2mm
Fast pulsing (2.5kHz) with activArc
0.35s
180A
0.7s
1mm
Automated pulses with activArc
0.5s
150A
0.1s
Fillet weld
2mm
Fast pulsing (2.5kHz) with activArc
0.5s
250A
0.3s
1mm
Automated pulses with activArc
0.4s
200A
0.1s
1mm
Fast pulsing (2.5kHz)
0.4s
200A
0.1s
Lap weld
2mm
Fast pulsing (2.5kHz) with activArc
0.5s
270A
0.5s
spotArc setting instructions for C-steel panels
Seam shape
Panel thickn
ess
Pulse type/
welding typ
e
Spot time
Welding curr
ent
Down
-sl
o
p
e
tim
e
1mm Automated
pulses
0.3s
165A
0.5s
Butt weld
2mm Automated
pulses
0.35s
245A
0.5s
1mm
Automated pulses with activArc
0.5s
170A
0.5s
Fillet weld
2mm
Fast pulsing (2.5kHz) with activArc
0.45s
270A
0.5s
1mm
Fast pulsing (2.5kHz)
0.3s
250A
0.5s
Lap weld
2mm
Fast pulsing (2.5kHz) with activArc
0.5s
270A
0.5s