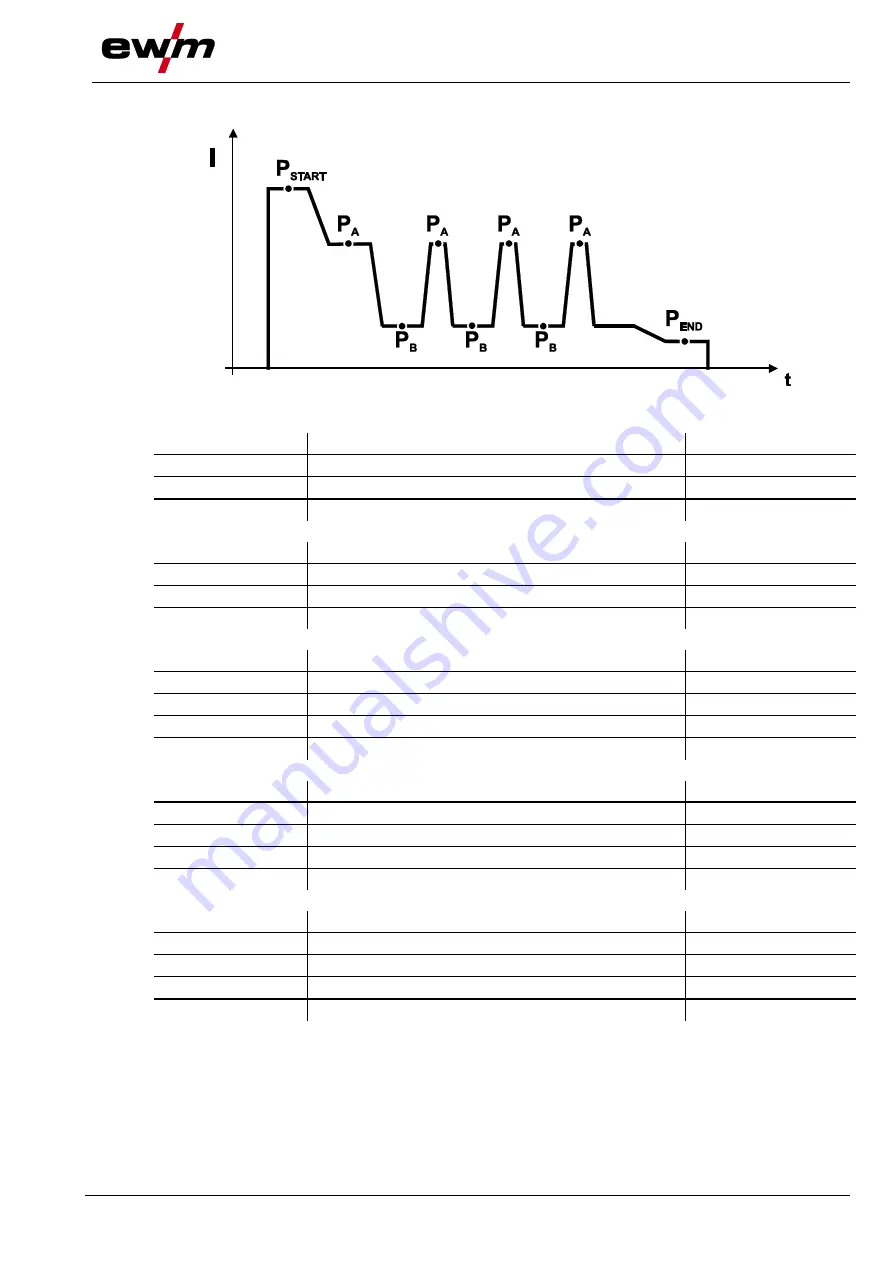
Design and function
MIG/MAG welding
099-005407-EW501
8.2.2022
59
5.3.11.6 Example, visible seams (latched super pulse)
Figure 5-45
Basic parameters
Welding parameter Meaning / explanation
Setting range
GASstr
Gas pre-flow time
0.0s to 20.0s
GASend:
Gas post-flow time
0.0s to 20.0s
RUECK
Wire burn-back length
2 to 500
"P
START
" start program
Welding parameter Meaning / explanation
Setting range
DVstart
Wire speed
0% to 200%
ustart
Arc length correction
-9.9V to +9.9V
tstart
Duration
0.0s to 20s
"P
A
" main program
Welding parameter Meaning / explanation
Setting range
tS1
Slope duration from P
START
to P
A
0.0s to 20s
DV3
Setting the wire speed
0% to 200%
t2
Duration
0.1s to 20s
tS3
Slope duration from P
B
to P
A
0.0s to 20s
"P
B
" reduced main program
Welding parameter Meaning / explanation
Setting range
tS2
Slope duration from P
A
to P
B
0.0s to 20s
DV3
Wire speed
0% to 200%
U3
Arc length correction
-9.9V to +9.9V
t3
Duration
0.1s to 20s
"P
END
" end-crater program
Welding parameter Meaning / explanation
Setting range
tSend
Slope duration from P
A
or P
B
to P
END
0.0s to 20s
DVend
Wire speed
0% to 200%
Uend
Arc length correction
-9.9V to +9.9V
tend
Duration
0.0s to 20s