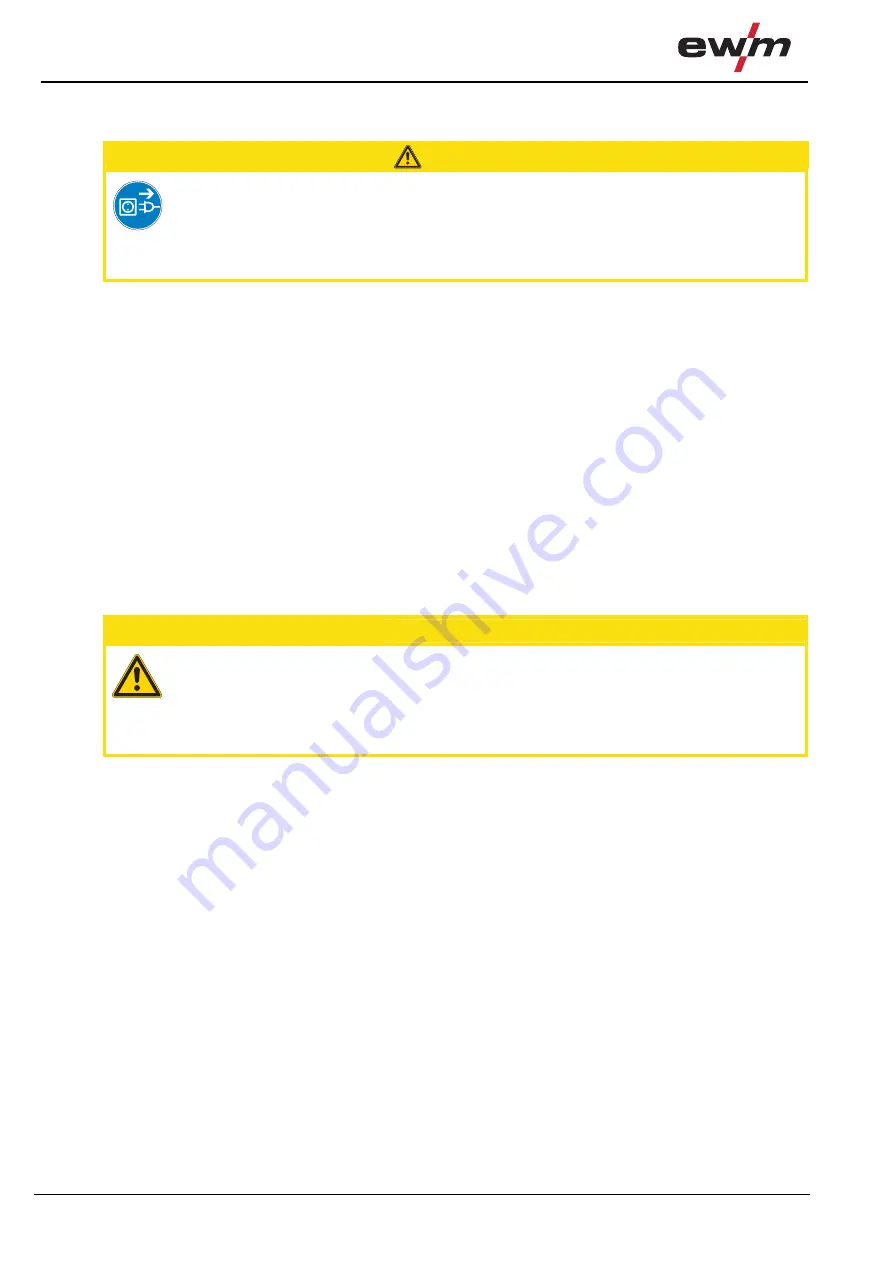
Safety instructions
Transport
8
099-500046-EW501
14.06.2011
2.4
Transport
CAUTION
Damage due to supply lines not being disconnected!
During transport, supply lines which have not been disconnected (mains supply leads,
control leads, etc.) may cause hazards such as connected equipment tipping over and
injuring persons!
• Disconnect
supply
lines!
2.4.1
Scope of delivery
The delivery is checked and packaged carefully before dispatch, however it is not possible to exclude the
possibility of damage during transit.
Receiving inspection
• Check that the delivery is complete using the delivery note!
In the event of damage to the packaging
• Check the delivery for damage (visual inspection)!
In the event of complaints
If the delivery has been damaged during transport:
• Please contact the last haulier immediately!
• Keep the packaging (for possible checking by the haulier or for the return shipment).
Packaging for returns
If possible, please use the original packaging and the original packaging material. If you have any queries
on packaging and protection during transport, please contact your supplier.
2.5
Ambient conditions
CAUTION
Equipment damage due to dirt accumulation!
Unusually high quantities of dust, acid, corrosive gases or substances may damage the
equipment.
• Avoid high volumes of smoke, vapour, oil vapour and grinding dust!
• Avoid ambient air containing salt (sea air)!
2.5.1
In operation
Temperature range of the ambient air:
• -10 °C to +40 °C
Relative air humidity:
• Up to 50% at 40 °C
• Up to 90% at 20 °C
2.5.2
Transport and storage
Storage in an enclosed space, temperature range of the ambient air:
• -25 °C to +55 °C
Relative air humidity
• Up to 90% at 20 °C