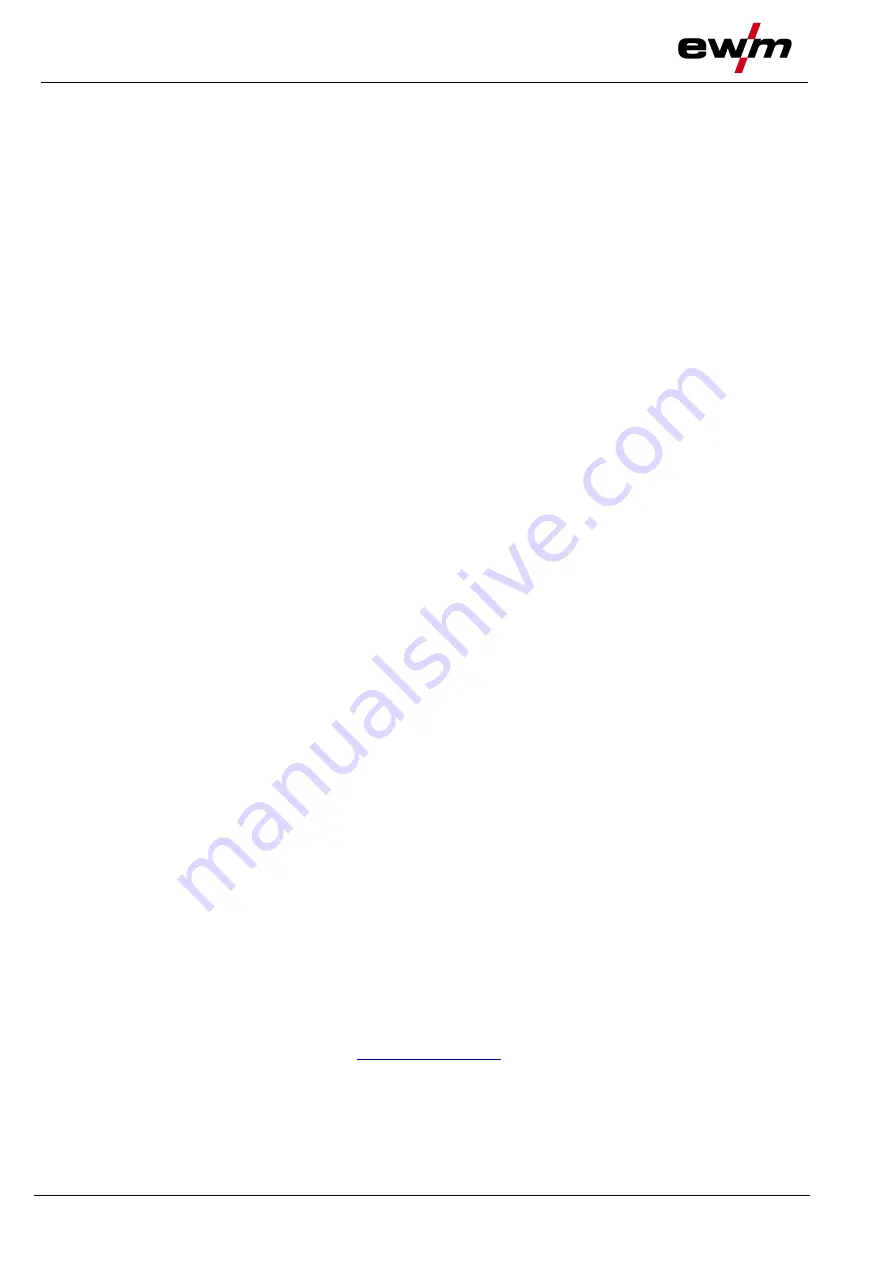
Maintenance, care and disposal
Maintenance work, intervals
44
099-002061-EW501
05.05.2020
6.2 Maintenance work, intervals
6.2.1 Daily maintenance tasks
Visual inspection
• Mains supply lead and its strain relief
• Gas cylinder securing elements
• Check hose package and power connections for exterior damage and replace or have repaired by
specialist staff as necessary!
• Gas tubes and their switching equipment (solenoid valve)
• Check that all connections and wearing parts are hand-tight and tighten if necessary.
• Check correct mounting of the wire spool.
• Wheels and their securing elements
• Transport elements (strap, lifting lugs, handle)
• Other, general condition
Functional test
• Operating, message, safety and adjustment devices (Functional test)
• Welding current cables (check that they are fitted correctly and secured)
• Gas tubes and their switching equipment (solenoid valve)
• Gas cylinder securing elements
• Check correct mounting of the wire spool.
• Check that all screw and plug connections and replaceable parts are secured correctly, tighten if ne-
cessary.
• Remove any spatter.
• Clean the wire feed rollers on a regular basis (depending on the degree of soiling).
6.2.2 Monthly maintenance tasks
Visual inspection
• Casing damage (front, rear and side walls)
• Wheels and their securing elements
• Transport elements (strap, lifting lugs, handle)
• Check coolant tubes and their connections for impurities
Functional test
• Selector switches, command devices, emergency stop devices, voltage reducing devices, message
and control lamps
• Check wire guide elements (wire feed roll holder, wire feed nipple, wire guide tube) for tight fit.
Recommendation for replacing the wire feed roll holder (eFeed) after 2000 hours of operation, see re-
placement parts).
• Check coolant tubes and their connections for impurities
• Check and clean the welding torch. Deposits in the torch can cause short circuits and have a negative
impact on the welding result, ultimately causing damage to the torch.
6.2.3 Annual test (inspection and testing during operation)
A periodic test according to IEC 60974-4 "Periodic inspection and test" has to be carried out. In addition
to the regulations on testing given here, the relevant local laws and regulations must also be observed.
For more information refer to the "Warranty registration" brochure supplied and our information regarding
warranty, maintenance and testing at