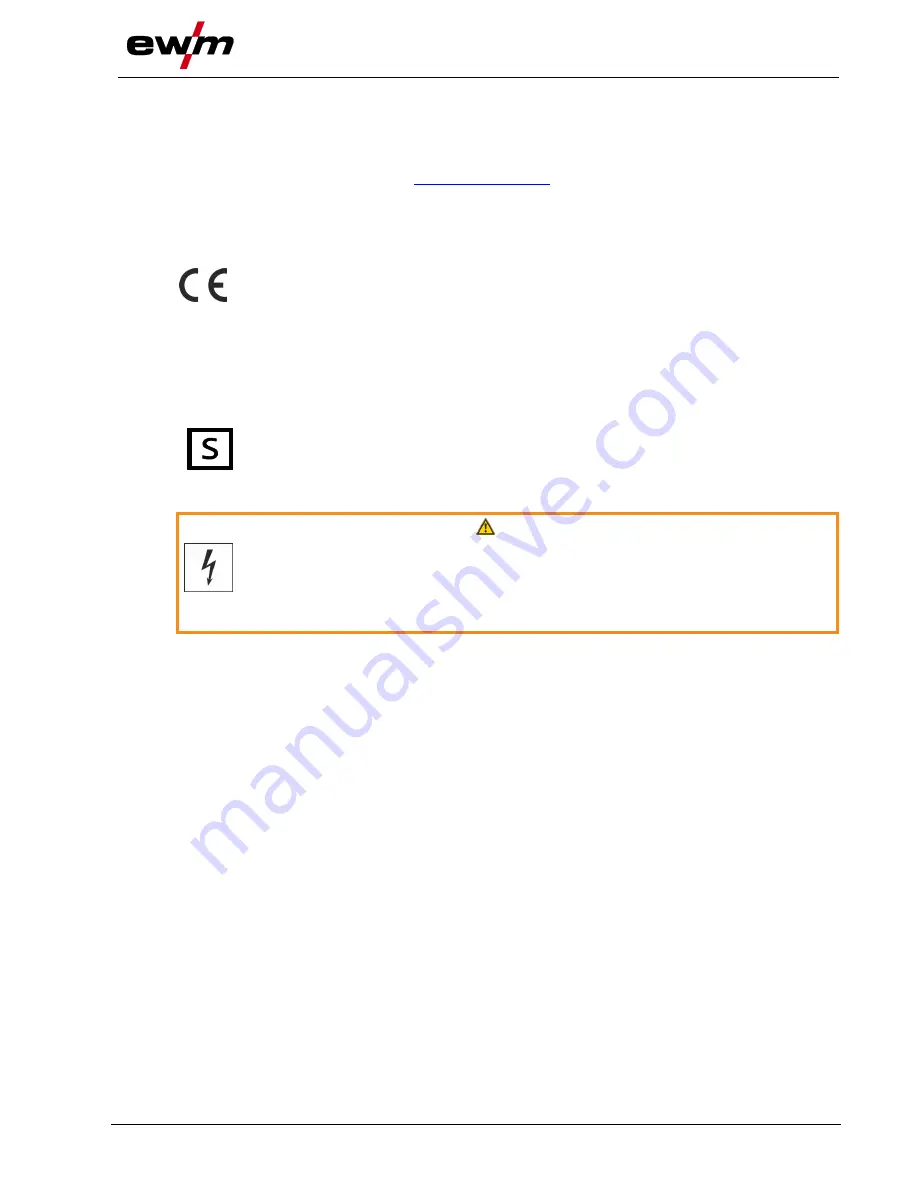
Intended use
Documents which also apply
099-002032-EW501
15.10.2018
15
3.3
Documents which also apply
3.3.1
Warranty
For more information refer to the "Warranty registration" brochure supplied and our information regarding
warranty, maintenance and testing at
www.ewm-group.com
!
3.3.2
Declaration of Conformity
The labelled product complies with the following EC directives in terms of its design and
construction:
• Low Voltage Directive (LVD)
• Electromagnetic Compatibility Directive (EMC)
• Restriction of Hazardous Substance (RoHS)
In case of unauthorised changes, improper repairs, non-compliance with specified deadlines for "Arc
Welding Equipment
– Inspection and Testing during Operation," and/or prohibited modifications which
have not been explicitly authorised by the manufacturer, this declaration shall be voided. An original
document of the specific declaration of conformity is included with every product.
3.3.3
Welding in environments with increased electrical hazards
In compliance with IEC / DIN EN 60974, VDE 0544 the machines can be used in
environments with an increased electrical hazard.
3.3.4
Service documents (spare parts and circuit diagrams)
WARNING
Do not carry out any unauthorised repairs or modifications!
To avoid injury and equipment damage, the unit must only be repaired or modified by
specialist, skilled persons!
The warranty becomes null and void in the event of unauthorised interference.
• Appoint only skilled persons for repair work (trained service personnel)!
Original copies of the circuit diagrams are enclosed with the unit.
Spare parts can be obtained from the relevant authorised dealer.
3.3.5
Calibration/Validation
We hereby confirm that this product was tested with calibrated measuring equipment according to the
applicable standards IEC/EN 60974, ISO/EN 17662, EN 50504 and complies with the permissible
tolerances. Recommended calibration interval: 12 months.