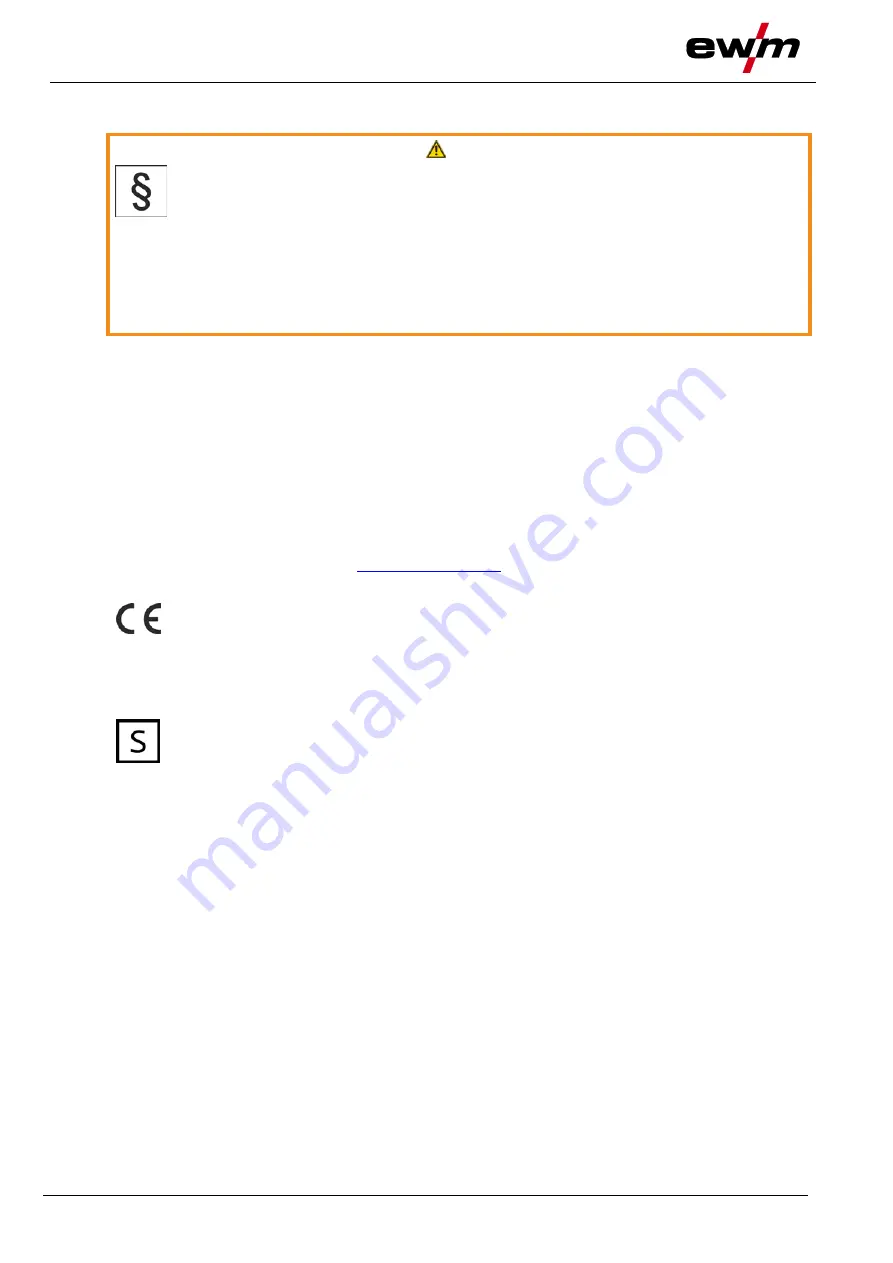
Intended use
Applications
8
099-002129-EW501
15.10.2020
3
Intended use
WARNING
Hazards due to improper usage!
The machine has been constructed to the state of the art and any regulations and stand-
ards applicable for use in industry and trade. It may only be used for the welding proce-
dures indicated at the rating plate. Hazards may arise for persons, animals and material
objects if the equipment is not used correctly. No liability is accepted for any damages
arising from improper usage!
• The equipment must only be used in line with its designated purpose and by trained or
expert personnel!
• Do not improperly modify or convert the equipment!
3.1 Applications
Arc welding machine for MMA DC welding with TIG DC welding with lift arc (touch starting) as secondary
process.
3.1.1 Demagnetize function (degaussing)
The degaussing of ferromagnetic workpieces in welding technology is intended to reduce arc deflection,
arc instability, uneven droplet detachment, spatter and irregular flank connections.
3.2 Documents which also apply
3.2.1 Warranty
For more information refer to the "Warranty registration" brochure supplied and our information regarding
warranty, maintenance and testing at
3.2.2 Declaration of Conformity
This product corresponds in its design and construction to the EU directives listed in the decla-
ration. The product comes with a relevant declaration of conformity in the original.
The manufacturer recommends carrying out the safety inspection according to national and in-
ternational standards and guidelines every 12 months.
3.2.3 Welding in environments with increased electrical hazards
Power sources with this marking can be used for welding in an environment with increased
electrical hazard (e.g. boilers). For this purpose, appropriate national or international regulations
must be followed. The power source must not be placed in the danger zone!
3.2.4 Calibration/Validation
An original certificate is enclosed with the product. The manufacturer recommends calibration / validation
at intervals of 12 months.