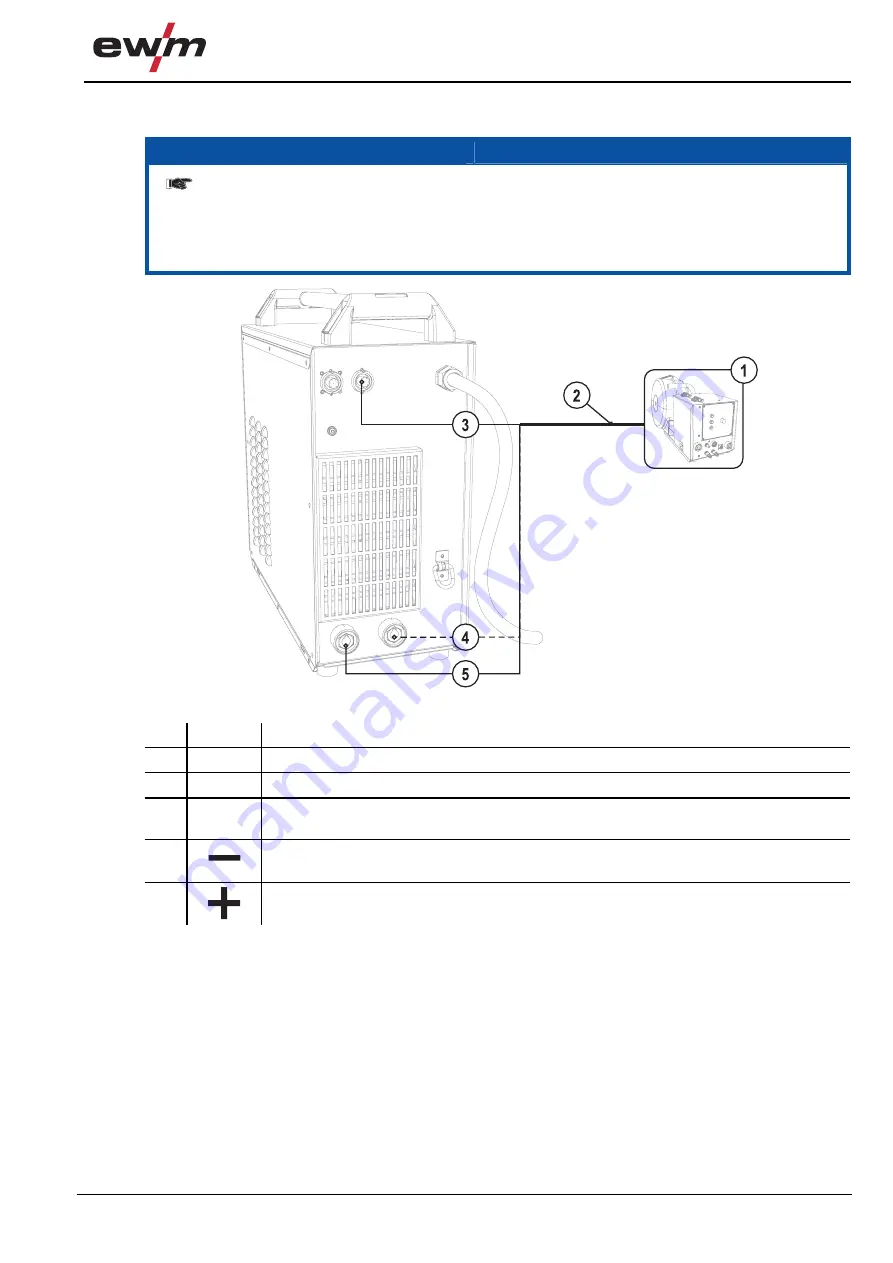
Design and function
Connecting the intermediate tube package to the power source
099-008717-EW501
24.03.2011
21
5.6.2
Intermediate tube package connection
NOTE
Note the polarity of the welding current!
Some wire electrodes (e.g. self-shielding cored wire) are welded using negative polarity.
In this case, the welding current lead should be connected to the "-" welding current
socket, and the workpiece lead should be connected to the "+" welding current socket.
• Observe the information from the electrode manufacturer!
Figure 5-3
Item Symbol Description
0
1
Wire feed unit
2
Intermediate tube package
3
Connection socket, 7-pole
Connection for peripheral devices with digital interface
"-" welding current connection socket
4
• MIG/MAG cored wire welding:
Welding current to central connection/torch
Connection socket, "+" welding current
5
• MIG/MAG welding:
Welding current to central connection/torch
• Insert the end of the tube package through the strain relief of the tube package and lock by turning to
the right.
• Insert the plug on the welding current lead into the welding current connection socket "+" and lock.
• Insert cable plug on the control lead into the 7-pole connection socket and secure with crown nut (the
plug can only be inserted into the connection socket in one position).