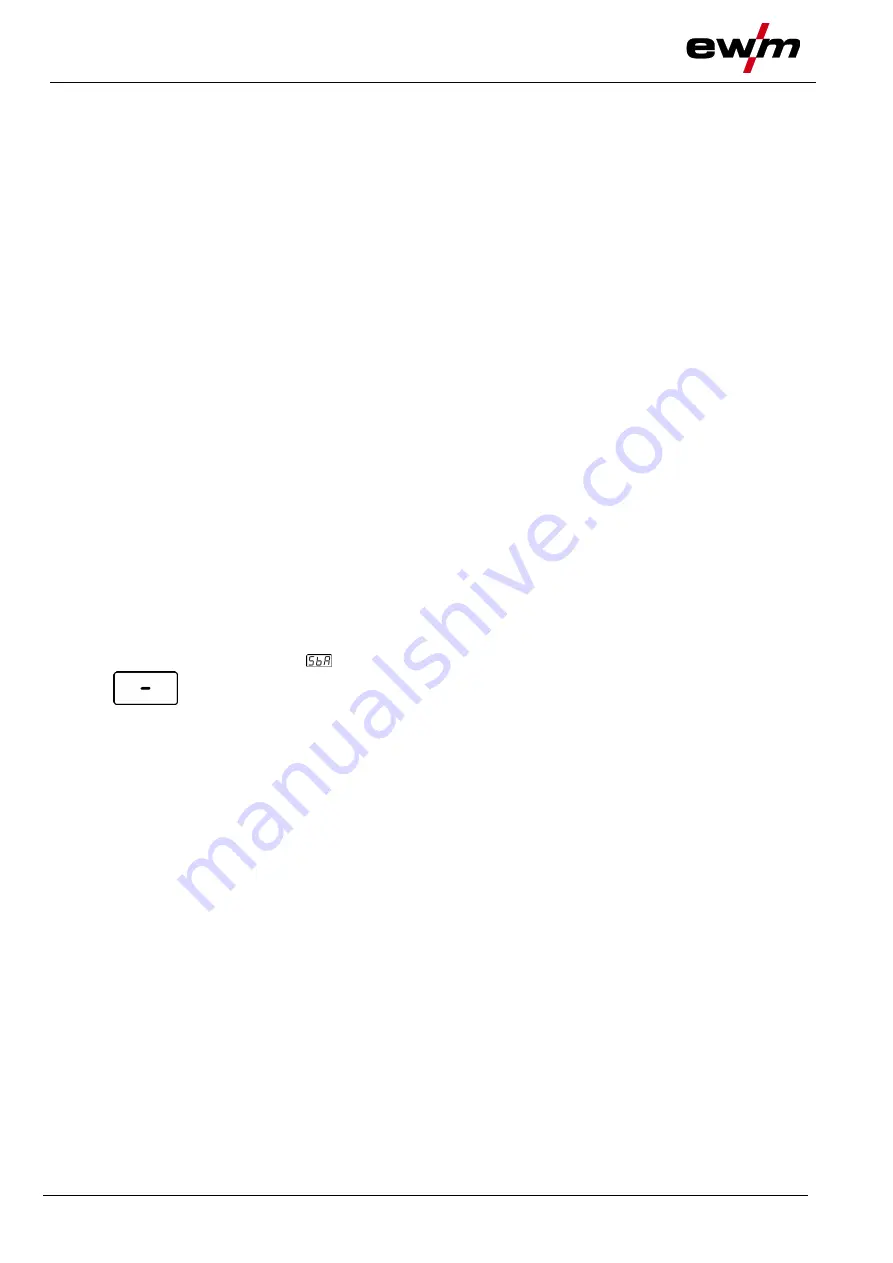
Functional characteristics
Power-saving mode (Standby)
54
099-5TLPXQ-EW501
29.01.2021
1 Preparation
• Switch off the welding machine.
• Unscrew the gas nozzle from the welding torch.
• Trim the welding wire so that it is flush with the contact tip.
• Retract the welding wire a little (approx. 50 mm) on the wire feeder. There should now be no more
welding wire in the contact tip.
2 Configuration
• Press and hold "Welding power rotary knob", at the same time switch on the welding machine (at least
2 s). Release rotary knob (device changes after a further 5 s to the first parameter cable resistance 1).
• Turn the "Welding power rotary knob" to select the appropriate parameter. Parameter rL1 must be ad-
justed for all machine combinations. In case of welding systems with a second power circuit – if two
wire feeders are to be operated from a single power source, for example – a second adjustment with
parameter rL2 must be performed.
3 Alignment/Measurement
• Applying slight pressure, put the welding torch in place with the contact tip on a clean, purged location
on the workpiece and then press the torch trigger for approx. 2 seconds. A short-circuit current will
flow briefly, which is used to determine and display the cable resistance. The value can be between
0 mΩ and 40 mΩ. The new value is immediately saved without requiring further confirmation. If no va-
lue is shown on the right-hand display, then measurement failed. The measurement must be repeated.
4 Restoring welding standby mode
• Switch off the welding machine.
• Screw the gas nozzle onto the welding torch.
• Switch on the welding machine.
• Insert the welding wire.
5.9 Power-saving mode (Standby)
You can activate the power-saving mode by setting a parameter in the machine configuration menu (time-
controlled power-saving mode
)
> see 5.8 chapter
.
When power-saving mode is activated, the machine displays show the horizontal digit in the
centre of the display only.
Pressing any operating element (e.g. turning a rotary knob) deactivates power-saving mode and the ma-
chine is ready for welding again.
5.10 Special parameters (advanced settings)
Special parameters (P1 to Pn) are applied for customer-specific configuration of machine functions. This
allows the user maximum flexibility in optimising their requirements.
These settings are not configured directly on the machine control since a regular setting of the parame-
ters is generally not required. The number of selectable special parameters can deviate between the ma-
chine controls used in the welding system (also see the relevant standard operating instructions).
If required, the special parameters can be reset to the factory settings
> see 5.10.2 chapter
.