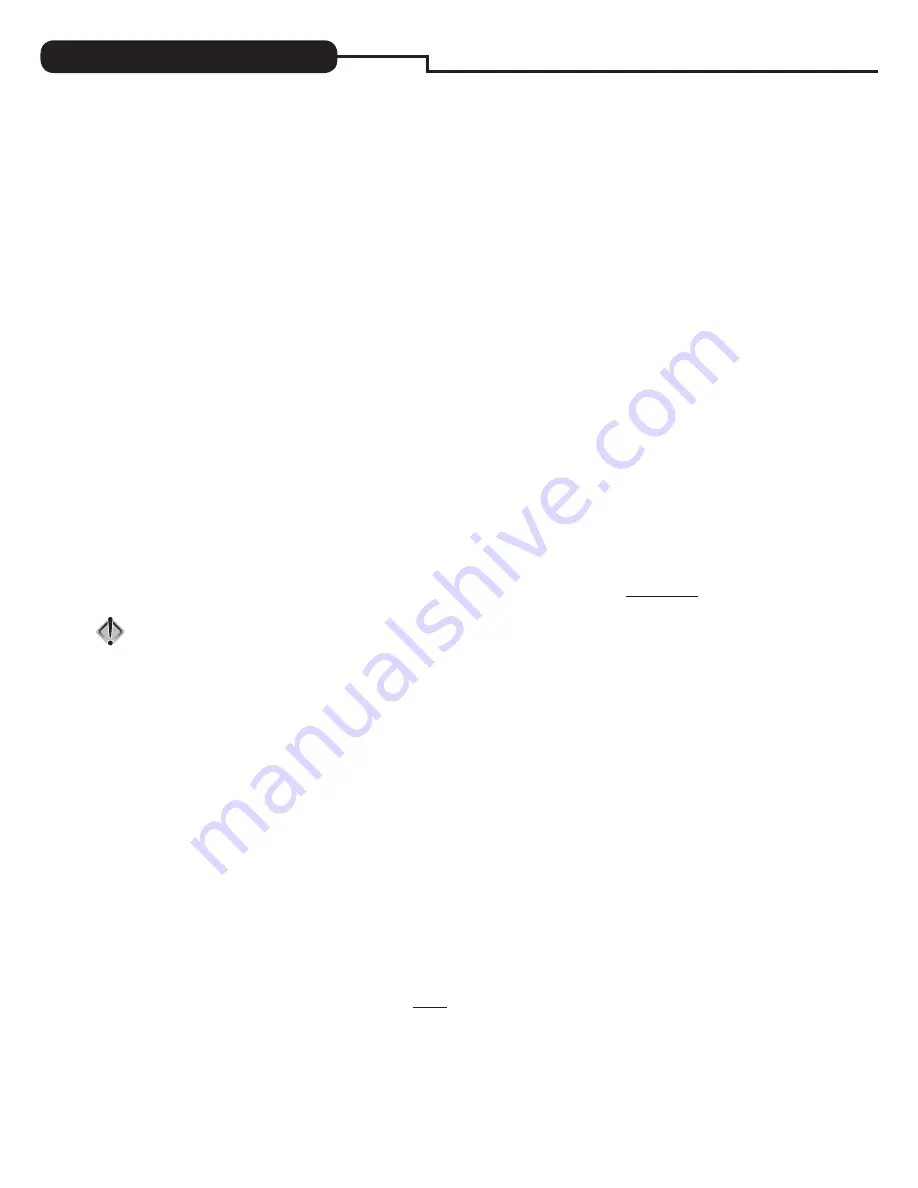
8
9
STARTUP INSTRUCTIONS
FLUSHING OF SYSTEM:
To flush the system of any debris and air after installation is complete, please perform the following steps:
1. Rotate bypass handles to the bypass mode
(Fig. 2 on page 4)
.
2. Turn on inlet water and check for leaks in the newly installed plumbing.
3. Fully open a cold water faucet, preferable at a laundry sink or bathtub without an aerator.
4. Wait two to three minutes or until water runs clear, then turn water off and follow start-up instructions.
Below is the name of each cycle as it appears on the screen with a description of the cycle position. The timing of each cycle will
vary depending on the unit size as set from the factory.
Name of Cycle
Description
FILL
BRINE
TANK
FILL
SOFTENING
SOFT
WATER
BRINE
MAKING
BACKWASH
BACKWASH
REGENERANT DRAW DN (DOWN)
BRINE DRAW AND SLOW RINSE
RINSE
FAST
RINSE
The system is now ready for filling with water and for testing.
1. With the softener in the bypass mode
(Fig. 2 on page 4)
and the control valve in normal operation where the display
shows either the time of day or the gallons remaining, manually add 3” of water to the brine tank.
NOTE:
If too much water is put into the brine tank during softener start up, it could result in a “salty water”
complaint after the first regeneration.
During the first regeneration the unit will draw out the initial volume of brine/regenerant and refill it with the correct preset amount.
2. With the softener in bypass mode, press and hold the
REGEN
button until the motor starts. Release button. The display reads
“FILL” and the remaining time in this step is counting down. Since the brine tank was already filled in Step 1, press
REGEN
again and the display will read SOFTENING 240 (During a full regeneration this will be a 4 hour period for salt to dissolve).
Press
REGEN
again to put the valve into “BACKWASH.” Once valve has stopped in position, unplug the transformer so that
the valve will not cycle to the next position. Open the inlet handle of the bypass valve very slightly allowing water to fill the
tank
slowly
in order to expel air.
CAUTION:
If water flows too rapidly, media will be lost to the drain.
3. When the water is flowing steadily to the drain without the presence of air, slowly open the inlet valve.
Restore power and momentarily press the
REGEN
button to advance the control to the “BRINE” position.
4. With the bypass now in diagnostic mode
(Fig. 3 on page 4)
, check to verify that water is being drawn from brine tank with no
air leaks or bubbles in the brine line. There should be a slow flow to the drain. Disconnect brine line from the safety float valve in
the brine tank and check for a vacuum. After proper confirmation, reconnect brine line, making sure to tighten securely.
5. Momentarily press
REGEN
again until the display reads “RINSE.” There should be a rapid flow to the drain. Unplug
transformer to keep the valve in the “RINSE” position. Allow to run until steady, clear and without air. While the unit is rinsing,
load the brine tank with water softener salt
(Refer to Brine Tank Maintenance and Salt Section)
. Restore power.
6. Place bypass valve in the normal operating mode
(Fig. 1 on page 4)
by opening the outlet bypass handle.
Press
REGEN
and the unit will return to the service position with time of day being displayed.
7.
CONDITIONING OF MEDIA:
To flush any remaining debris and air from the system again:
1. Full open a cold water faucet, preferably at a laundry sink or bathtub without an aerator.
2. Wait two to three minutes or until water runs clear, then turn water off.
3. Turn on hot water and check for air, then turn water off after air is discharged.
8.
SANITIZING OF UNIT UPON INSTALLATION AND AFTER SERVICE:
At this time, it is advised to sanitize the softener:
1. Open brine tank and remove brine well cover.
2. Pour 1 oz. of household bleach into the brine well.
NOTE:
Avoid pouring bleach directly onto the safety float components in the brine well.
3. Replace brine well cover.
Unit sanitizing will be complete when the first cycle is run and the bleach is flushed from the unit.
9. Check time of day. Start-up is now complete.
FOR DOWNFLOW REGENERATING UNITS