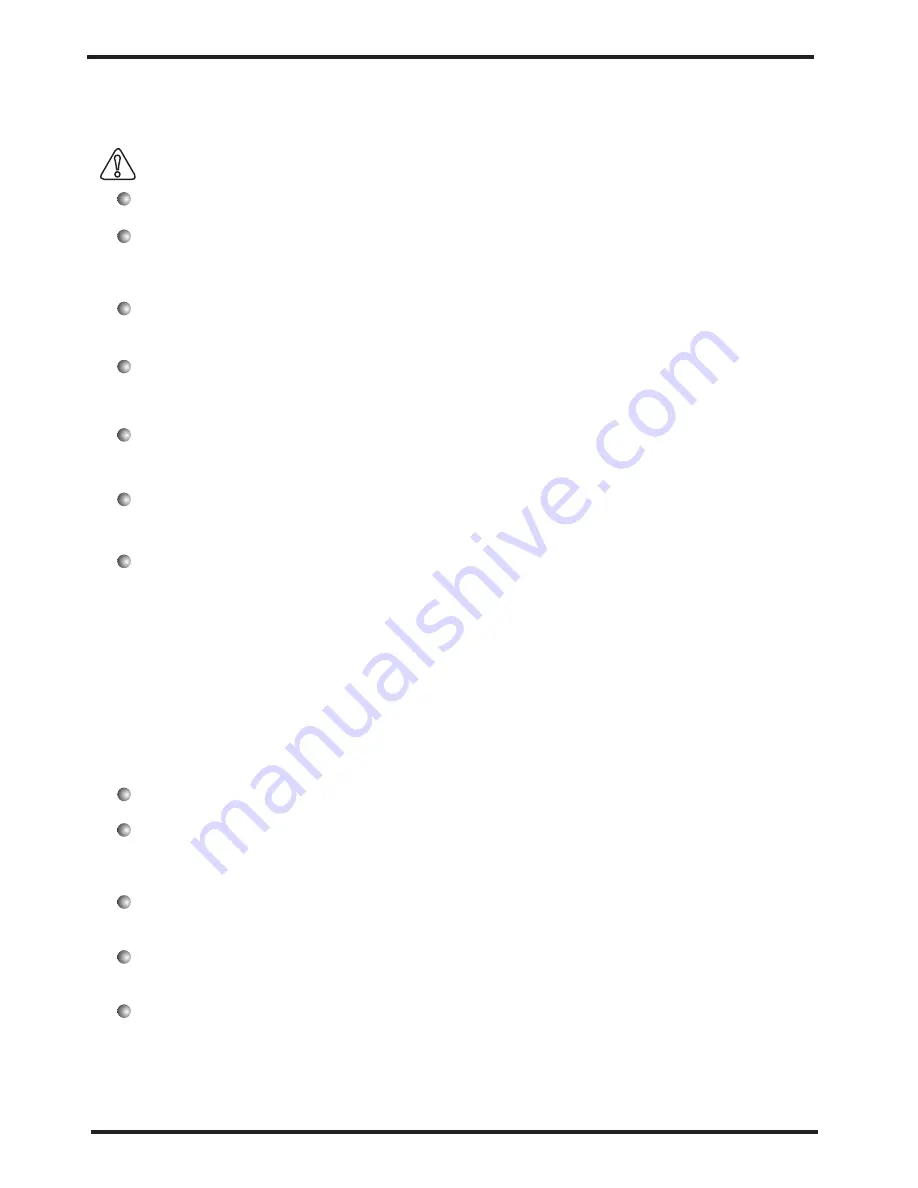
10
5.Installation
5.5 Installation Mode
The unit is directly secured to the cement base with the expansion bolts.
Use channel steel to make the installation base, place shockproof rubber pads on
the ground or the roof, and ensure that the unit is placed levelly.
Air-out direction
1
5
0
0
m
m
Figure 1 Installation Schematic Diagram of Snow Shed
To ensure the proper functioning of the unit in cold
areas in winter, the snow shed must be installed
during the engineering installation.
Caution
5.6 Water Pipe Connection
Note the following items during connection of water inlet and outlet pipes:
`
Minimize the resistance of the water pipe outside the unit.
The entire piping system should be clean and free of dirt and rust to prevent pipe
clogging. Test for leakages after the pipes are installed to ensure that the entire
piping system is free of leakage, and then coat with the insulating layer.
The pipeline should be conducted with a pressure test separately, rather than
together with the air conditioning main engine.
An expansion water tank should be installed at the highest point of the water
distribution pipeline, where the highest point of the water level in the expansion water
tank is at least 0.5 meters higher than the water distribution pipe.
Flexible joints should be used between the unit interface and the field piping to
reduce the vibration spread to both buildings and equipment. Both the pipe and the
fittings must be independently supported, but should not be supported by the unit.
The thermometer and the pressure gauge should be installed at the water inlet and
outlet pipes of the unit to facilitate the inspection during operation.
Drainage interfaces should be installed at all low positions of the water system (the
unit has a drain port to facilitate drainage; interfaces will be added in other positions
on site) so that the water in the system will be completely drained if it is not used in
winter; automatic exhaust valves should be installed at all high positions so as to
facilitate to exhaust the air from the pipeline. No insulation is provided for both the
exhaust valves and the drain port for easy maintenance.
5.7 Electrical Wiring
Open the panel, and open the power line hole
Thread the power line through the hole and connect it to the power line terminal; and
the three-core control line of the remote controller shall be plugged with the three-core
signal line on the main board according to the wiring diagram.
For an external water pump, thread the power line of the water pump through the hole
and connect it to the water pump terminals.
If it is necessary to automatically control the auxiliary heat source, connect the control
output signal of the auxiliary heat source to the start switch of the auxiliary heat source.
If it is necessary to automatically control mode of the air conditioning terminal, connect
the mode control signal to the mode control switch on each indoor air conditioning
terminal.
5.Installation
11
Summary of Contents for ALLHT1170R134
Page 35: ...Note...
Page 36: ...Code 20170803 0003...