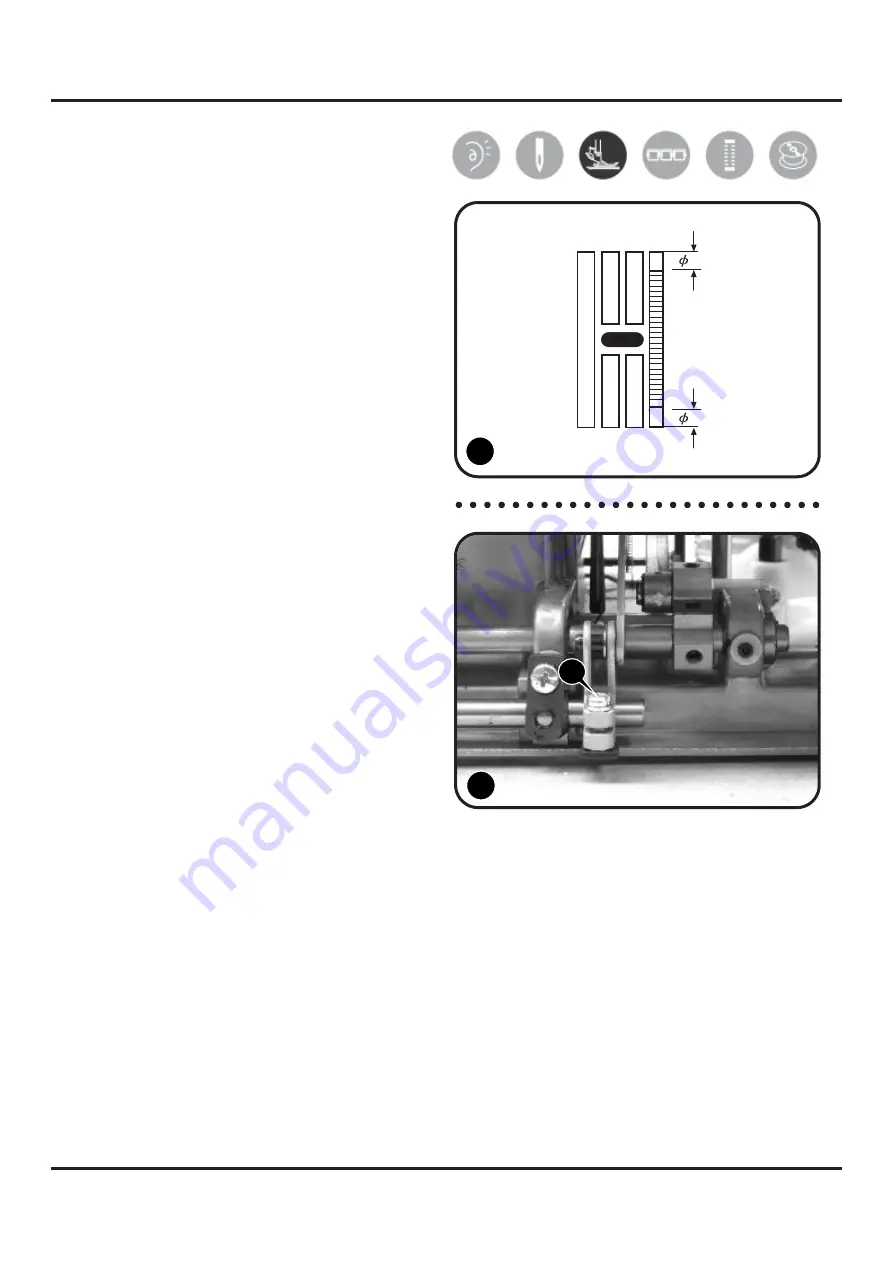
21
5-18 Position of the feed-dog in
relation to the needle plate
(front to back)
1) Remove the free arm cover, base plate
and set the stitch length dial to "4".
2) Turn hand wheel to move feed-dog
forward and backward.
3) Feed-dog must have clearance along
the whole length of feeding movement.
It must at no time touch the needle plate.
(1)
4) Otherwise, adjust feed rock crank screw.
1
5) Loosen screw (a) of feed rock crank.
Moving feed-dog forward/backward until
reaching to the center position. (2)
6) Tighten screw (a) after adjustment.
a
2
a
1
2
Summary of Contents for sew&go 1
Page 1: ...Repair Manual sparrow 15 series...
Page 4: ...3 2 Out Look...
Page 31: ...Voltage 230V Voltage 120V...