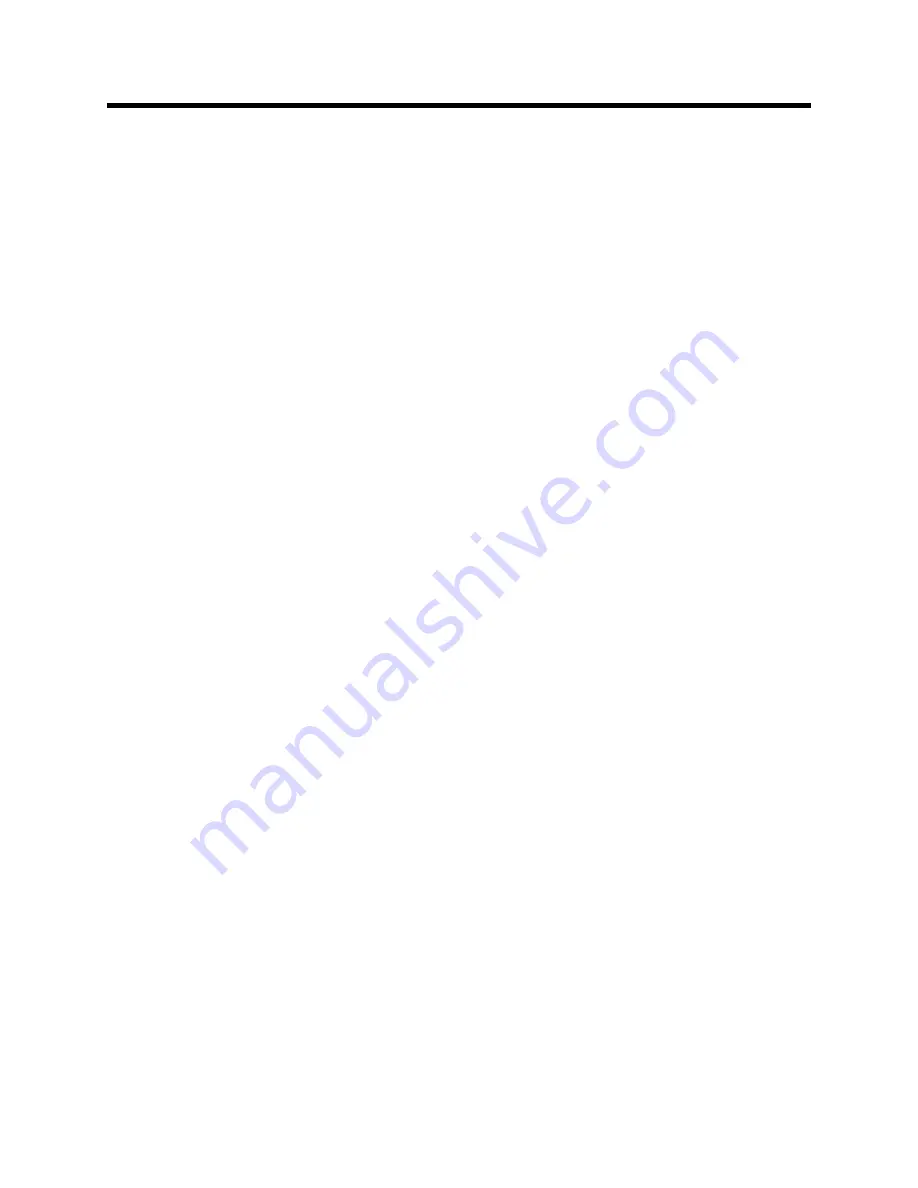
10
1.1
General Description, Purpose and Features.
The Power i
-
MIG 200E is a portable MIG (GMAW) welder
designed for light repair and fabrication. The unit oper-
ates on 120V or 240V V single phase input and comes
equipped with a standard 120V NEMA 6
-
50P plug for
convenient use in almost any standard 240V outlet. The
unit includes a 240V to 120V pigtail adapter. The Power
i
-
MIG 200E
’
s IGBT inverter design is rated for 25% duty
cycle at 200 amps operating on 240V and at 115 amps
operating on 120V. It is designed to consume less pow-
er, provide better arc stability and offer better duty cycle
over transformer and inverter input class. There are no
tapped settings which prevent fine adjustment of either
voltage or wire speed. Both amps (wire speed) and
voltage are infinitely adjustable within their ranges.
1.2
Basic Design and Construction.
The Power i
-
MIG
200E features an advanced IGBT inverter design, with
plug and play circuits and controls for maximum service-
ability and lifespan. The unit has a full time high speed
fan which maintains temperature levels providing in-
creased duty cycle and performance. A heavy duty wire
feeder mechanism features cast aluminum and steel
construction for long life. The unit will accommodate
4”
(1
-
2lb) and
8”
(10
-
12lb) rolls of wire and features
rapid tool
-
free, wire spool installation. Gun connection
is quick with the tool
-
free design of the Euro quick con-
nect fitting. The Work clamp is equally easy to install,
and features a 25 series DINSE style connector. For
transport or storage both MIG gun and work clamp can
be disconnected in less than 15 seconds. The standard
drive rolls included with the unit are designed for use
with
.023”
-
.030”
solid wire. The smaller groove (.6mm)
should be used with
.023
-
.027”
wire. The larger groove
(.8mm) should be used with
.030”
wire. For general
purpose use, Everlast recommends that
.030”
ER70S
-
6
wire be used for most general purpose welding. This
diameter wire and class is designed to work well with
the amp output range that the Power i
-
MIG 200E deliv-
ers. The unit can weld with wire up to .9 mm in diameter
with optional drive roll. In a pinch the
.030”
roll will work
to feed the
.035”.
But if
.035”
wire is to be used regular-
ly, purchase the optional
.035”
drive roll for best results.
The limitations of the gun liner prevents the use of any
larger diameter wires. Flux
-
core drive rolls are optional.
The recommended flux core drive roll to be used with
this unit is
.035”.
The flux core drive roll has serrated
edges to the groove which grip the soft wire. The stand-
ard V
-
groove wire will not feed smoothly with flux
-
core
wire. Special applications like aluminum may be welded
with the optional spool gun. It is possible to weld alumi-
num with the main feeder and gun, but a special gun
liner must be purchased and a harder wire such as 5356
should be used to prevent
“
bird
’
s nesting
”
of the wire.
The best spool gun for this unit is the Everlast SM
-
3035
gun. Use
.035”
diameter wire for best results. Stainless
can be welded with either the spool gun or the standard
gun. Using a spool gun may be a more practical choice if
welding smaller projects with stainless or aluminum
since both stainless and aluminum wires are expensive.
Either coated (copper or other coatings) or uncoated steel
wire may be used for welding steel as long as it remains
rust
-
free and clean.
NOTE: For flux core use, special
.035”
drive rolls with a
serrated design may be purchased from Everlast. U
-
groove rolls, along with a polymer gun liner may be used
to feed aluminum with the main feeder, and are optional.
.035”
wire diameter is the maximum wire diameter rec-
ommended for feeding of steel and stainless wires.
.045”
is the maximum wire recommended for aluminum
(main gun). In the spool gun use
.035”
wire for alumi-
num.
1.3
Installation.
The design of the Power i
-
MIG 200E is
compact and able to travel almost anywhere 120V or 240V
single phase service is available. For maximum output
capability on 240V, a minimum of 30 amp circuit breaker is
recommended. Up to 50A 240V circuit is permitted. Use a
minimum of a 20 amp slow trip circuit breaker when oper-
ating on 120V. For best results, operate this unit on a 30
amp breaker if using on 120V. If this unit is on a 15 amp
circuit operating at or near the maximum amp/volt settings
of the welder the circuit breaker may trip. If this happens,
reduce the settings on the welder.
Care and common sense should be taken to make sure
that the welder offers the safest and best performance.
Please note the following items regarding safe operation:
1)
Do not use the welder in damp or wet areas. Perspira-
tion and other forms of water in contact with the body
can increase the risk of electrocution.
2)
Do not use the welder in extremely corrosive environ-
ments. To maintain optimum power transfer, check
main connections, clamps and cables frequently to
ensure that components are not corroded. Excessive
dirt, corrosion and oxidation can result in an unstable
arc and excessive heat build
-
up.
3)
Do not kink or tightly coil the MIG gun or the wire may
not feed properly. Coiling tightly may even damage
the liner or cable if the cable becomes kinked.
Always
use the MIG gun with the cable running as straight as
possible. Gentle, natural curves are acceptable. Do
not stand on or roll objects over the welder cables.
Pay close attention if the welder is on a rolling cart so
that the cables are not accidentally rolled over when
moving it around.
4)
Do not pull, hold, or suspend the welder by the gun or
cables. Pick up the welder from the handle only.
5)
Due to the light weight and compact size, strap or tie
the welder down (over the top) to prevent accidental
overturning while in use on a table or cart.
1.4
Duty Cycle.
Duty Cycle is expressed as the percent-
age of time out of 10 minutes at the rated amps/volts that
the welder can weld without an interruption or break. Af-
ter this the welder should be allowed to rest the remainder
of the 10 minutes. If the duty cycle light is triggered, the
Introduction and Specifications
Section 1