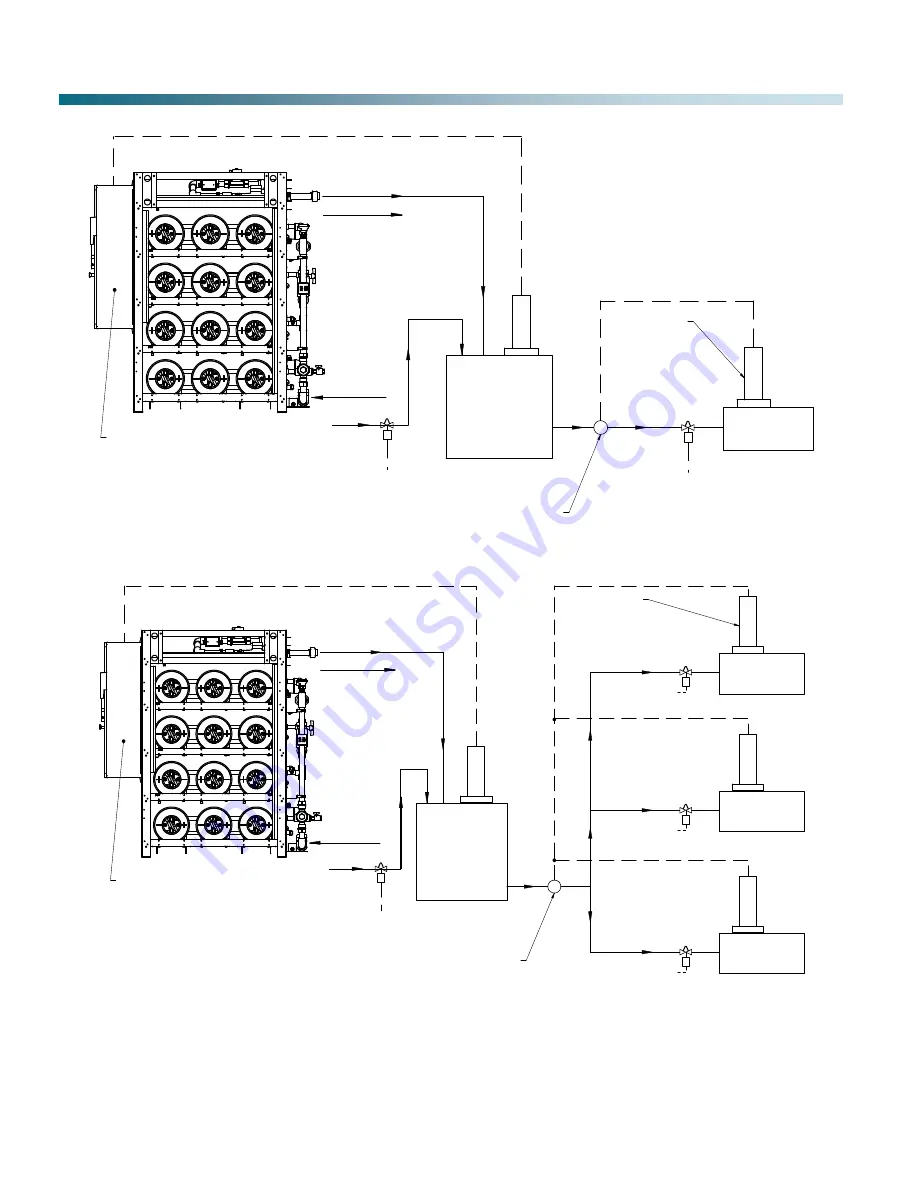
7
Design Considerations (Continued)
Figure 7: EWS Field Piping/Wiring for Multiple Evaporative Units with Makeup Tank
BOOSTER PUMP REQUIRED
(BY OTHERS)
S
EWS
MAKE UP TANK
MAKE UP
BYPASS
CLEAN OUTLET, PIPE TO PROCESS
FLUSH OUTLET, PIPE TO DRAIN
(NOT IN VIEW)
EWS CONTROL
PANEL
P
E
W
L
C
POWER AND CONTROL WIRING
EWLC REQUIRED
EVAPORATIVE UNIT
S
E
W
L
C
POWER AND CONTROL WIRING
WIRE TO EWLC
ON UNIT
EVAPORATIVE UNIT
BOOSTER PUMP REQUIRED
(BY OTHERS)
EWLC REQUIRED
(TYPICAL)
S
EWS
MAKE UP TANK
MAKE UP
BYPASS
CLEAN OUTLET, PIPE TO PROCESS
FLUSH OUTLET, PIPE TO DRAIN
(NOT IN VIEW)
EWS CONTROL
PANEL
WIRE TO EWLC
ON TANK
P
S
E
W
L
C
POWER AND CONTROL WIRING
E
W
L
C
S
E
W
L
C
S
E
W
L
C
WIRE TO UNIT EWLC
POWER AND CONTROL WIRING
POWER AND CONTROL WIRING
POWER AND CONTROL WIRING
EVAPORATIVE UNIT
EVAPORATIVE UNIT
WIRE TO UNIT EWLC
WIRE TO UNIT EWLC
Figure 6: EWS Field Piping/Wiring for Single Evaporative Unit with a Makeup Tank
WIRE TO EWLC
ON TANK