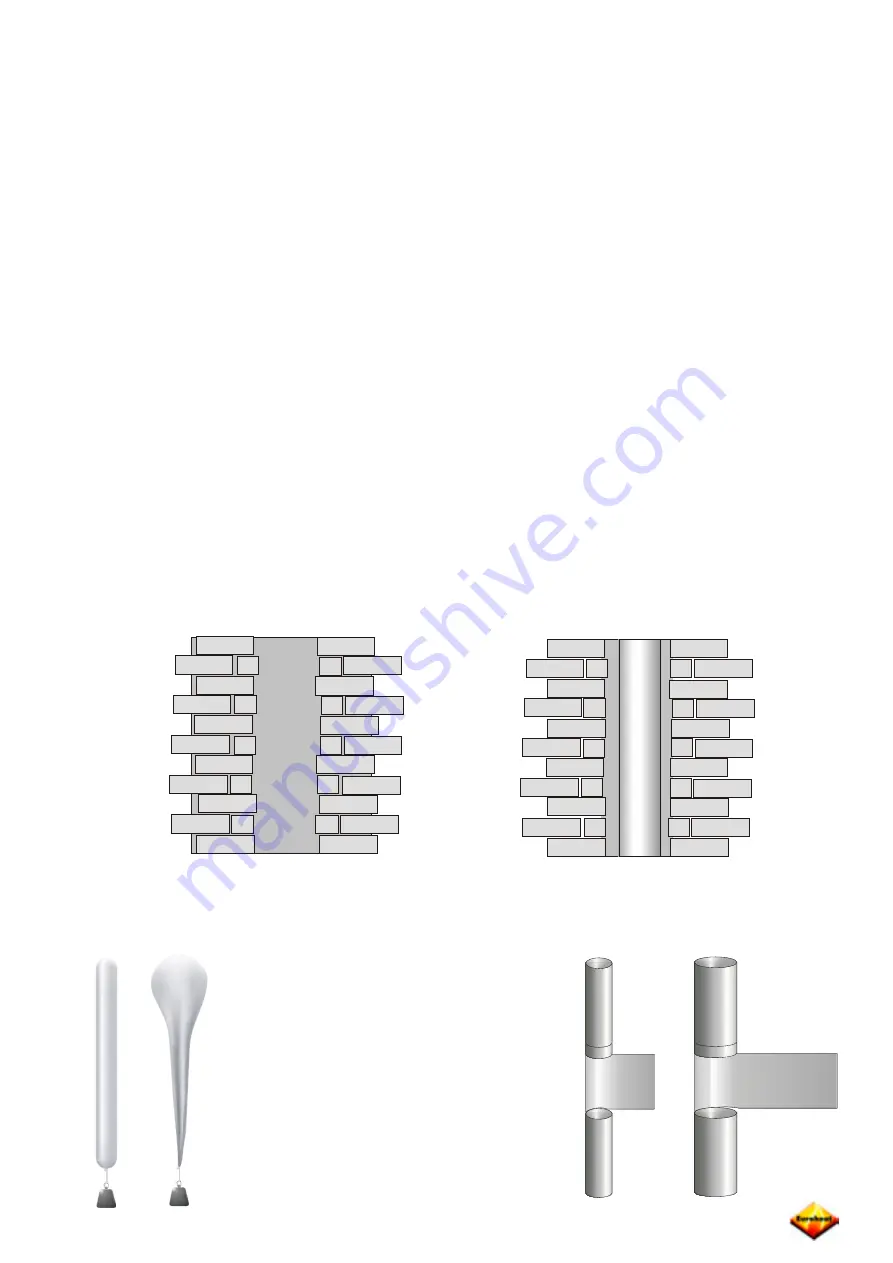
©
EUROHEAT
DISTRIBUTORS (H.B.S) LTD. March 2006
Technical Guide IN1087 Edition C
4
A flue system for an open fire has an enormous margin for design error because it receives so much
of the heat generated by the fire, and the fire is not expected to be controlled beyond the rate at which
it is refueled. The efficiency of a stove is achieved because less of the heat generated by the fire is
lost to the flue, and that the flue design allows consistent control of the fire. These impose design
constraints which become progressively more restrictive as the stove’s efficiency increases. With
less motivation the flue route taken must provide the smoothest path possible to retain as much of
the heat in the gases as possible.
If we look at the flue’s prime function, which is to remove the harmful products of combustion, we find
that even the chemicals themselves become more difficult to deal with at reduced flue temperatures.
One of the more important chemicals formed by the combustion process is oxygen dihydrate, a
chemical better known as water. The ability of the gases to “absorb” water is dependent on their
temperature and when the gases are “saturated”, the water will begin to condense out as the
temperature falls. The point at which the water will be shed by the gases is known as the “dew
point”, but unlike the picturesque dew covered image of dawn, this condensate will combine with
all the nasty acidic chemicals in the flue gases as it runs down the flue wall. Evidence of this can be
seen on the walls of old properties where this acidic water has been absorbed by the masonry flue
and has eaten away the lime mortar. This will be worse where the flue has been for a range or oven
which take out more heat from the fire. If the fire has been primarily fueled with wood, the creosote
and resinous tars may even reach the internal plaster not only staining them but posing a fire risk
because these tars are combustible. The flue needs to maintain the gases above the dew point
and this is achieved by making the flue as smooth as possible to reduce any friction between the
wall and the gases which will allow the smallest possible diameter to be used and so minimize the
surface area through which heat may be lost. A flue constructed from stainless steel satisfies all the
requirements because it is smooth, impervious to the chemicals, its low mass allows rapid warming
and it can be easily cleaned. Flexible metal flue liners should be installed in one unbroken length.
Other than the sealing at the top and bottom the void between the flue and the chimney should be
left empty except in circumstances where the void is deamed to be large.
Existing chimneys should have a stainless steel liner fitted. If the void between the liner and masonry
is large it may be filled with vermiculite to provide insulation it will then reach its operating temperature
more rapidly. Where no chimney exists, a twin walled, interlocking stainless steel system should be
used. The walls are separated by an insulating material.
An appliance produces a known quantity
of hot gases, capable of generating a
flue draught, whatever the flue size, if
its temperature difference is maintained.
All flues allow heat loss and reduce the
potential available. To reduce heat lost from
the flue the most basic design consideration
is to ensure its surface area is kept to a
minimum, by fitting the smallest diameter
recommended for the appliance.