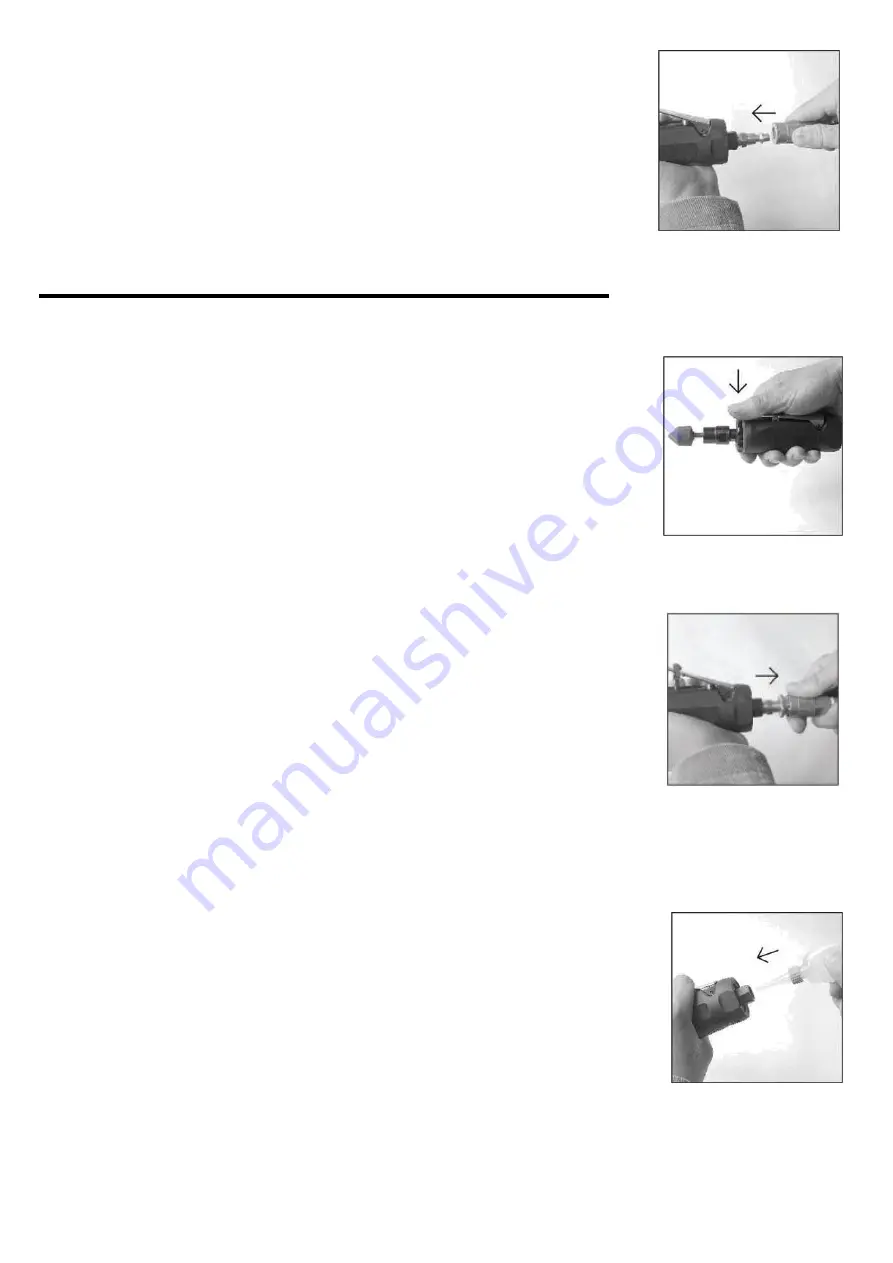
7
5.
Remove the
air
cap
from the
tool air
inlet
and connect
the
air
supply hose to
the
tool. Set the air pressure at
90
PSI
.
(See Figure
4)
6.
Push forward the lever block (Part #4)and press down on the
lever trigger (Part #3). How far the lever trigger is
pressed
determines
the
tool rotation speed. Then the tool starts to
work. (See Figure 5)
CARE AND MAINYENANCE
The tool should be lubricated daily (or before each use) with air
tool oil (not included).
Air tool oil is available at major tool hardware stores. SAE
#10 weight oil or sewing machine lubricant or any other
high grade turbine oil containing moisture absorbent,
rust inhibitors, metal wetting agents and an EP (extreme
pressure) additive may be used as a substitute. Do not
use detergent oil.
During continuous operation, the tool should be oiled
every 1 to 2 hours. This may be done using an in-line oiler,
or manually. If done manually, proceed as follows:
1.
Disconnect the tool from air supply. (See Figure 6)
2.
Place a few drops of air tool oil into the air inlet.
(See Figure 7)
Avoid the misuse of thicker oil which may lead to the reduced
performance or malfunction.
3.
Connect the tool to the air supply. Run the tool without load for
a few seconds to distribute the oil through the tool.
Any excess oil may be propelled from the exhaust area. So
keep the tool away in a safe direction.
4.
After operating the tool and before storing the tool,
disconnect the air hose and place 4 or 5 drops of air tool oil into
the air inlet, then re-connect the air hose and run the tool to
evenly distribute the oil throughout the tool for 30 seconds
approximately. This will prolong the tool life.
5.
Avoid storing the tool in a humid environment which
promotes rusting of internal mechanisms. Always oil the tool
before storage.
6.
When the tool is seriously damaged or out of life, it should be
left in a resource recycling can. Never drop it into fire.
Figure 4
Figure
5
Figure 6
Figure 7