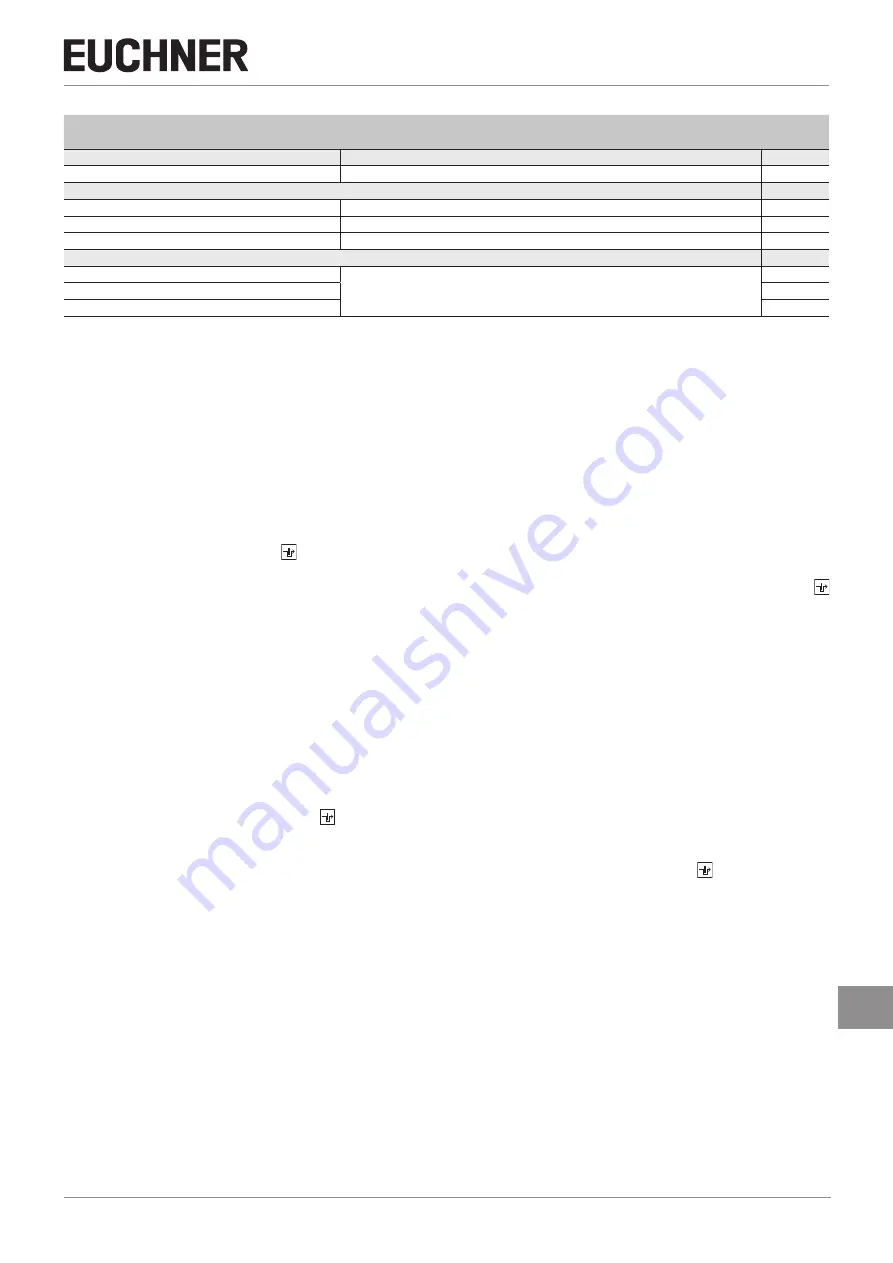
39
2527246-01-08/19 (Translation of the original operating instructions)
Operating Instructions
Safety System MGBS-P-L.-AR…
EN
Parameter
Value
Unit
min.
typ.
max.
Reliability values acc. to EN ISO 13849-1
Mission time
20
years
Monitoring of guard locking and the guard position
Category
4
Performance Level (PL)
e
PFH
D
4.1 x 10
-9
/h
Control of guard locking
Category
Depends on external control
Performance Level (PL)
PFH
D
1) Dependent on the handle module used.
2) Trip characteristic medium slow-blow.
3) Values at a switching current of 50 mA without taking into account the cable lengths.
4) Corresponds to the actuation frequency.
14.1.1. Typical system times
Please refer to the technical data for the exact values.
Ready delay
: After switch-on, the device carries out a self-test. The system is ready for operation only after this time.
Switch-on time of safety outputs
: The max. reaction time t
on
is the time from the moment when the guard is locked to
the moment when the safety outputs switch on.
Simultaneity monitoring of safety inputs FI1A/FI1B
: If the safety inputs have different switching states for longer than
a specific time, the safety outputs (FO1A and FO1B) will be switched off. The device switches to fault state.
Risk time according to EN 60947-5-3
: If a handle module moves outside the operating distance, the safety outputs
(FO1A and FO1B) are deactivated at the latest after the risk time.
If several devices are operated in a series connection, the risk time of the overall device chain will increase with each device
added. Use the following calculation formula:
t
r
= t
r, e
+ (n x t
l
)
t
r
= Total risk time
t
r, e
= Risk time, single device (see technical data)
t
l
= Risk time delay per device
n = Number of additional devices (total number -1)
Discrepancy time
: The safety outputs
(FO1A and FO1B) switch with a slight time offset. They have the same signal
state no later than after the discrepancy time.
Test pulses at the safety outputs
: The device generates its own test pulses on the safety outputs (FO1A and FO1B).
A downstream control system must tolerate these test pulses.
This can usually be set up in the control systems by parameter assignment. If parameter assignment is not possible for your
control system or if shorter test pulses are required, please contact our support organization.
The test pulses are also output when the safety outputs are switched off.