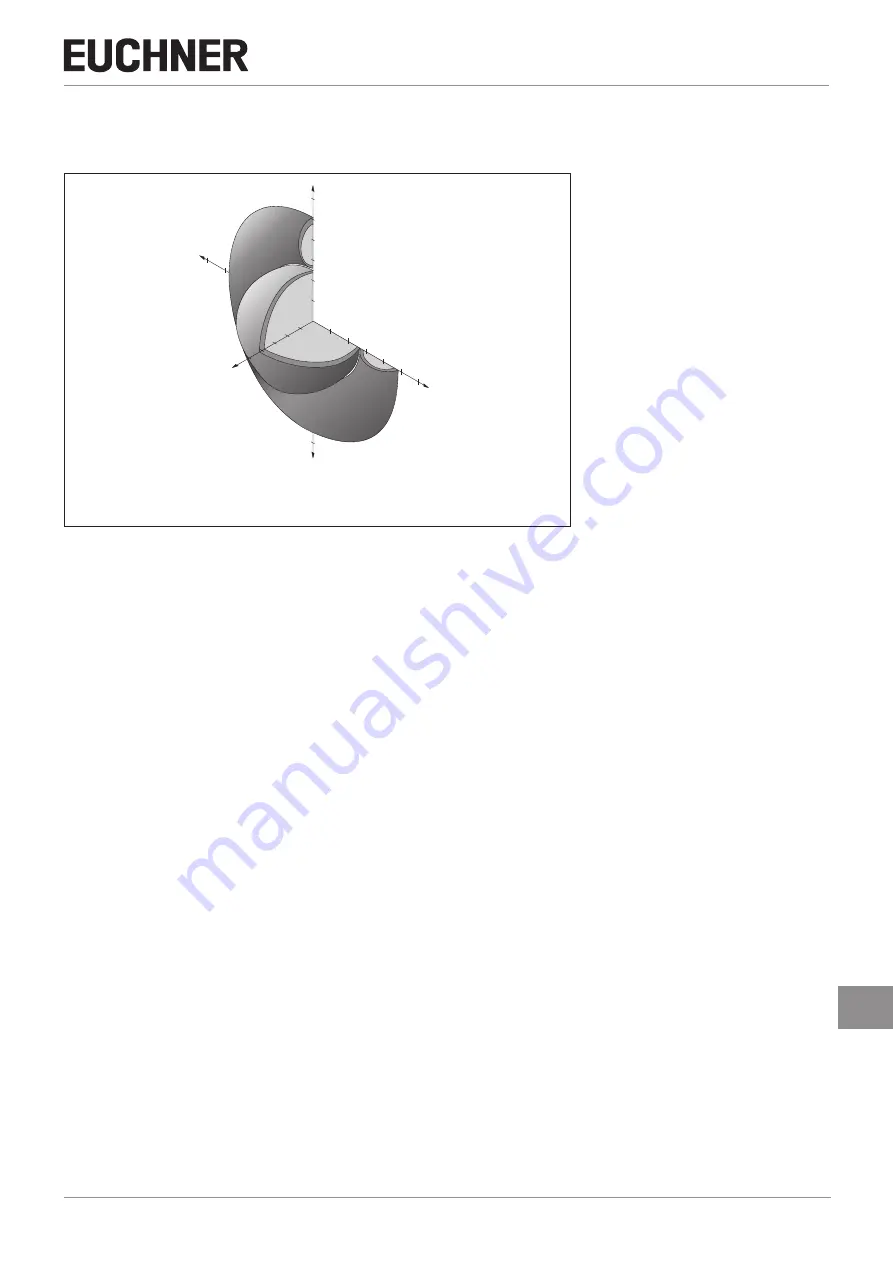
29
2098039-20-02/20 (Translation of the original operating instructions)
Operating Instructions
Non-Contact Safety Switch CES-AR-C01-…
EN
12.3.3. Typical actuating range
(only in combination with actuator CES-A-BDA-18 on surface mounting)
Y
30
25
20
15
10
5
-30
-30
-25
30
Z
15
20
25
10
5
X
25
20
15
10 5
For a side approach direction for the actuator and read head, a minimum
distance of s = 8 mm must be maintained so that the actuating range of the
side lobes is not entered.
Figure 7:
Typical actuating range