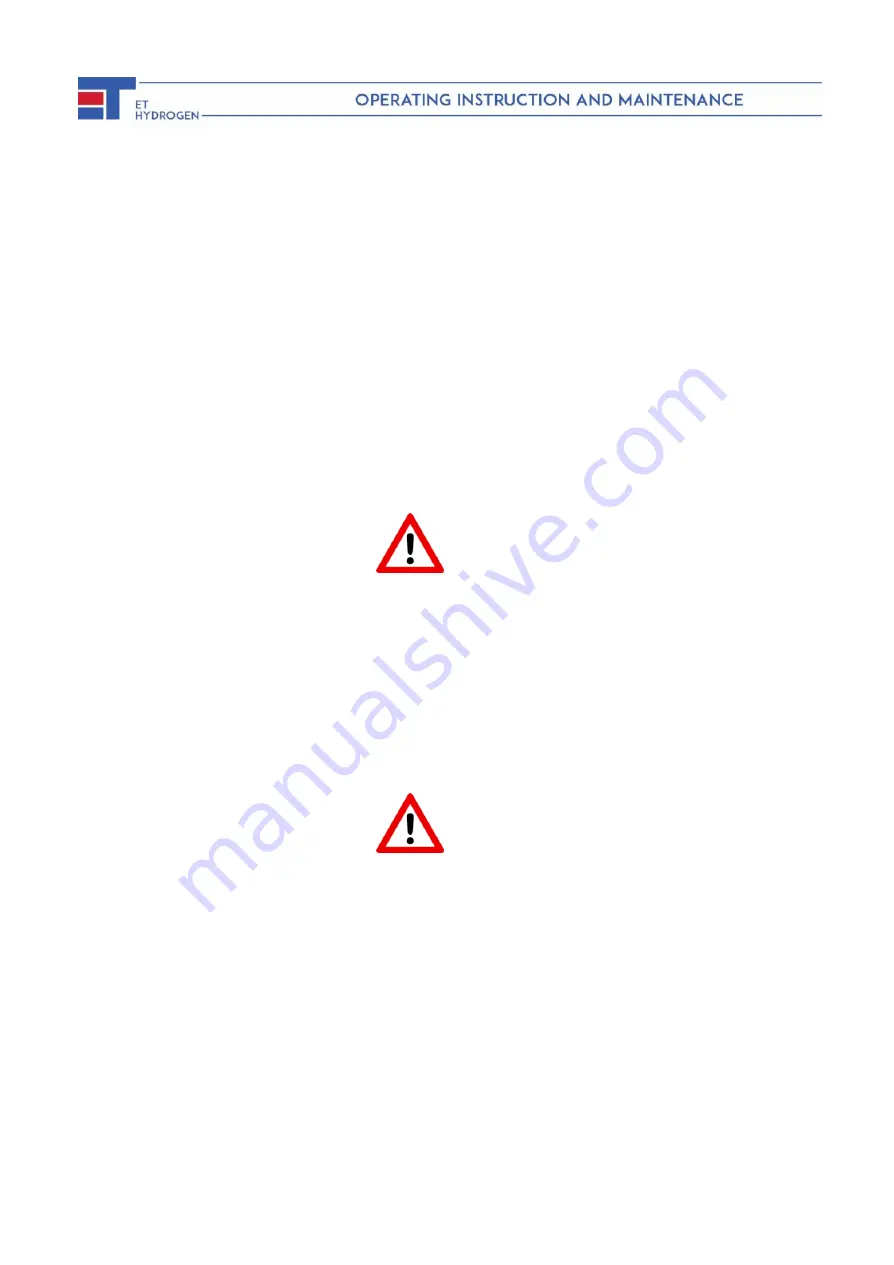
4
SECTION 1
Description and main features of the welder
1.1 PRESENTATION
This manual gives information regarded as necessary to know, use correctly and carry out normal
maintenance operations on this welder «
L/45
» (hereinafter referred to as machine) fabricated by
«
Elettronica Todescato S.r.l.
» di Arcugnano (Vicenza) Italy (hereinafter referred to as Manufacturer).
The material in this manual is not intended to be a complete description of the parts nor a detailed
explanation of their option. The user, however, will find the kind of information normally required to
operate the machine correctly and safely and also to keep in good working condition.
Compliance with and observance of what is described in the manual is an essential condition for the
trouble-free operation, long life and cost effective performance of the machine.
ATTENTION
Failure to observe the instructions in this manual, negligence, incorrect or improper use of the
machine can be cause of machine warranty coverage cancellation by manufacturer.
Manufacturer therefore declines any and all liability for injury to people or damage to property
caused by failure to follow the instructions given in this manual.
Service work or overhauls involving complex operations must be entrusted to an authorized Technical
Service Center which has the necessary specialized personnel, or directly to the Manufacturer who is at
your complete disposal to ensure fast and complete technical assistance and anything else that can
promote improved operation and optimal performance by the machine.
DANGER
This manual must be kept in a safe place at the disposal of the operator and service engineer,
for consultation at any time during the machine’s entire working life. It should be delivered with
the machine if the latter is sold.
The manual must be kept in a safe place that is familiar to the assigned personnel. It is the
responsibility of the personnel to keep the manual complete to allow for a consultation for the
entire life of the machine. If the manual is damaged or lost, a copy must be immediately
requested to the Manufacturer.
Summary of Contents for L/350
Page 1: ...1 ...
Page 2: ...2 ...
Page 28: ...28 FIG 5 SPARE PARTS ...
Page 29: ...29 ...
Page 30: ...30 ...
Page 31: ...31 ...