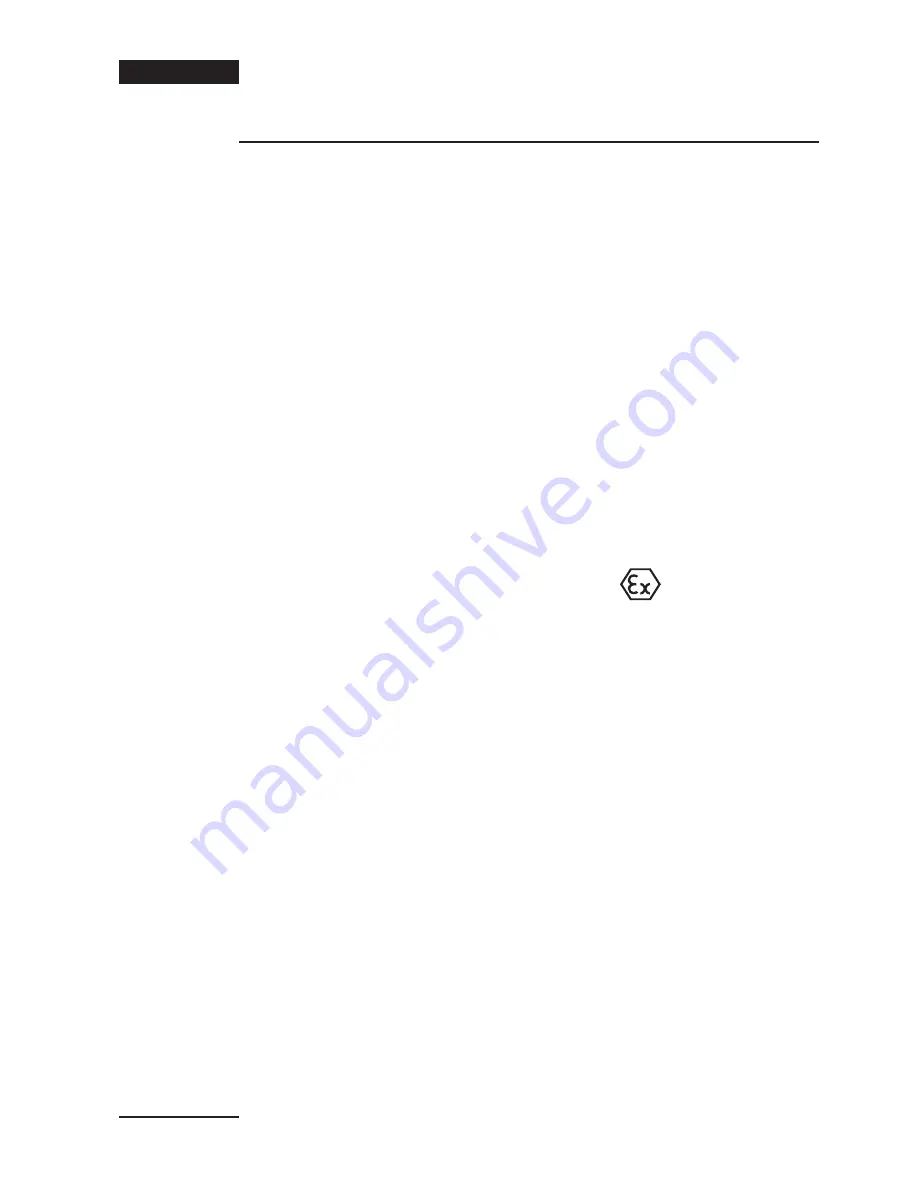
6
EST 651
TECHNICAL PARAMETERS
Maximum gun power (acc. to the nozzle used)
.
30 ÷ 250 l/h
Max. NH operating pressure ..................................
300 bar
Recommended control air pressure
............................
5 bar
(Control) Air quality:
– Max. due point
.....................................................+3°C
– Max. oil content
.............................................
25 mg/m
3
– Max. size of solid particles
....................................
40 μm
NH connecting thread size
..................................
M 14x1,5
Control air connecting size (insertion coupling)
...................
.......................................... to connect the ø 6.0x4.0 hose
Max. gun control rate
...........................
3-times per second
Gun weight (without nozzle)
....................................563 g
Connecting threads in the gun body
.........................
G 1/8“
Noise level
.........................................................
75 dB(A)
Ambient temperature
................................
+5°C až +40°C
Environment classification
Noise Level
The noise level depends on the nozzle system size and on the inlet
pressure value. The noise level of the gun reaches up to 75 dB(A).
Acc. to the act no. 272/2011 Coll., the maximum allowed noise level
is 85 dB(A).
II 2 GX
Summary of Contents for 651
Page 16: ...16 EST 651 DISPLAY OF COMPONENTS 96 162 2 5 81 40 82 5 29 1 0 40 161 80 2 5 ...
Page 18: ...18 EST 651 ...
Page 19: ...19 EST 651 ...