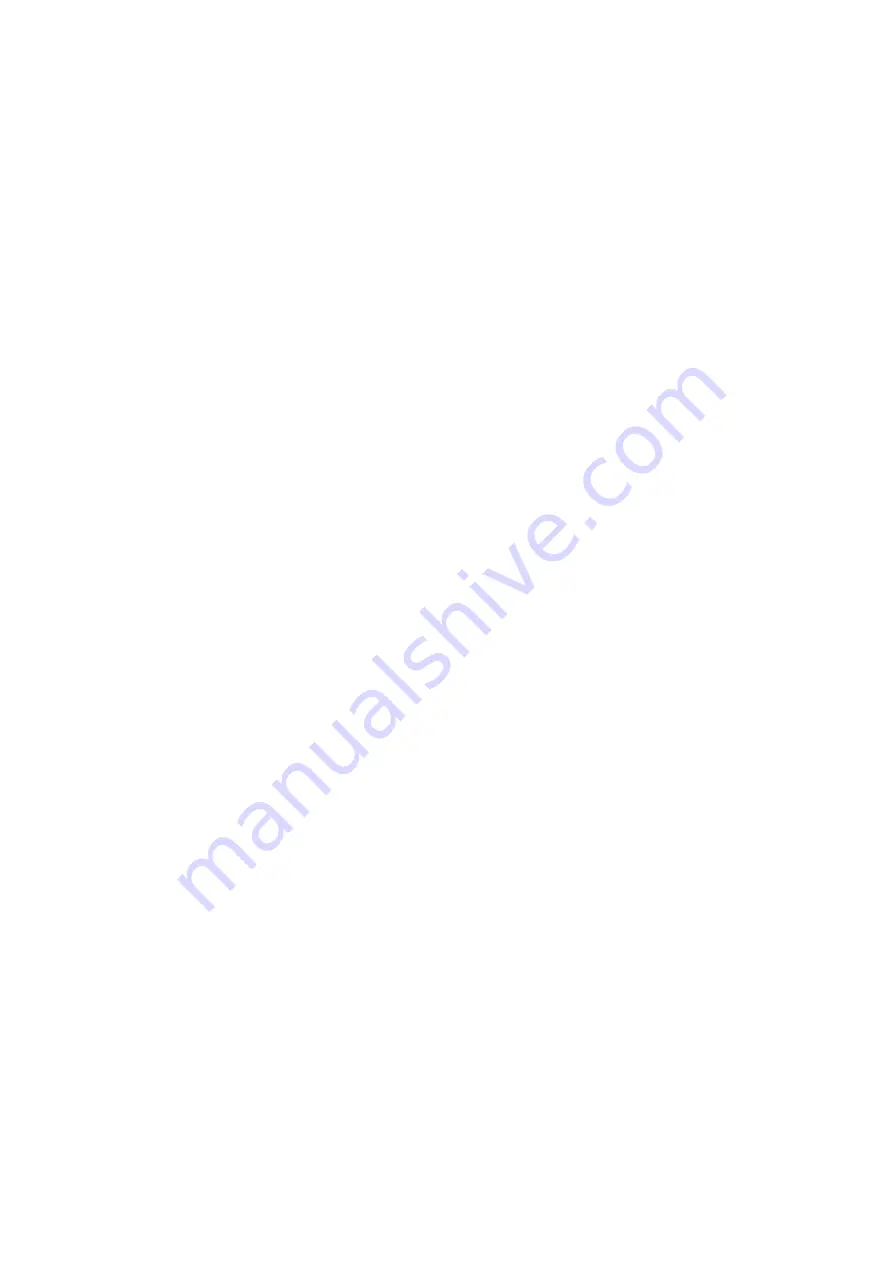
If the gas pressure regulator is shut down during operation for some reason; the inlet valve must be shut down, the
problem must be detected, and it must be re-setup according to the rules explained above.
On the ERG-SE series products, the outlet pressure may increase while operating due to the abrupt stopping of the
boiler or an internal leak originating from unclean air or the foreign substances on the line. When this happens, the
product's high pressure safety shut-off device may be turned off and the gas on the outlet side of the regulator may
be cut off. The position of the safety shut-off can be observed via the lever number 8 which is inside the transparent
cap number 9. In this case, the setup procedure must be carried out once again.
During operation, if there's an increase in capacity by 101% to 160% of the maximum capacity specified on the
regulator, the capacity restriction system is activated and the gas flow is cut off. In this case, the setup procedure must
be repeated. (In this case, the shut-off lever number 8 on the ERG-SE products remains in the locked position and is
not turned off, but the gas has been cut off by the regulator)
6- SETTINGS
If necessary for a variety of reasons, the product's outlet pressure and safety shut-off pressure settings (for ERG-SE
series products) must be carried out as follows. Under normal conditions, there's no need to change these settings.
These settings must be changed if the authorized people think it's necessary.
The settings must not be changed more than ± 10% and outside the restrictions on the label.
The seals on the adjustment parts of the product must be removed if they exist. While carrying out the pressure
settings, the adjustment mechanisms and the springs must not be pressed or forced. Connect the pressure gauge or
the manometer on an appropriate test valve between the regulator and the outlet pipe in order to see the setting
values. During all adjustments, turning it clockwise leads to pressure increase and turning it counterclockwise leads to
pressure decrease. When the outlet pressure is increased, the safety pressure must be increased as well.
In order to change the outlet adjustment pressure: manually turn the cap number 1 on Figure 8 counterclockwise to
remove it. Turn the adjustment ring number 2 towards the appropriate direction with a 27mm hexagonal wrench.
Mark the adjustment pressure. Manually turn the cap number 1 clockwise to reattach it.
Note: While setting the appropriate pressure for the product, it's recommended that you set the capacity value on the
outlet side to 0,5xQmax. This value must not be below 0,1xQmax under any circumstances.
In order to change the high pressure safety pressure on the ERG-SE series products: manually turn the cap number 9
on Figure 8 counterclockwise to remove it. Turn the adjustment ring number 10 on Figure 8 towards the appropriate
direction with a 13mm hexagonal wrench. Mark the adjustment pressure. Manually turn the cap number 9 clockwise
to reattach it.
In order to change the release system release adjustment pressure if it exists: manually turn the cap number 1 on
Figure 8 counterclockwise to remove it. Turn the adjustment ring in the internal part on Figure 4 towards the
appropriate direction with a 16mm hexagonal wrench. Mark the adjustment pressure. Manually turn the cap number
1 clockwise to reattach it.
After changing the settings; check and verify with appropriate methods that the technical properties and the
restrictions on this manual and on the product are complied, the product does not continuously release gas into the
atmosphere, the outlet pressure is at the desired level, and all procedures are carried out safely and correctly. After
making the pressure adjustments in question, it's recommended that the adjustment equipment is sealed on the
products that are being used in the field so that the adjustments cannot be changed. For this procedure, the seal inside
the box may be used if it exists.
Note: When the outlet adjustment pressure of the product is changed, taking into consideration the changes in the
working conditions, it must be verified that the pressure values are not close to the release adjustment pressures (if it
exists) and safety adjustment pressures, and that they are not within this range. Otherwise, the product continuously
releases gas into the atmosphere or the product's safety shut-off mechanism may get activated and unexpectedly cut
off the gas, which may lead to dangerous situations. It must be made sure that these situations do not occur after the
settings are changed.