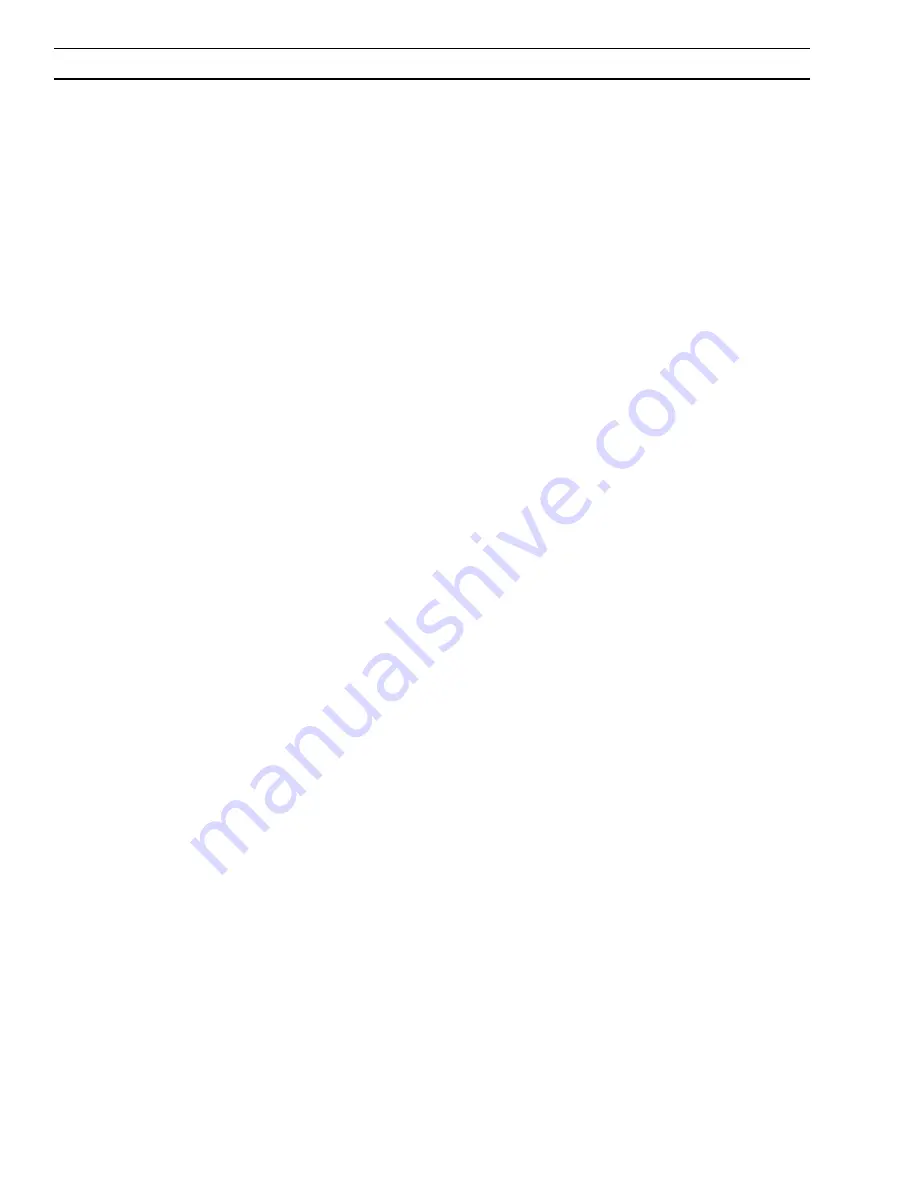
8
. Check to assure high frequency is present at the torch. If not, then listen for high frequency at the high frequency
generator. It is located on the bottom/right side of the unit. The high frequency gap is set to 0.040”. Disconnect HI
FReQueNCY leads. Check for 115 volt supply to the high frequency unit between P-1 & P-1 of the control board
with torch switch closed.
4. With HI FREQUENCY leads disconnected, measure open circuit voltage. It should be 75 VDC between “Work” and “Torch”
terminals. If it is not present then any one of the following may not be working properly:
a. Check the operation of the Thermal Switch. See D..a. above.
b. Check Air Check switch operation. It might be stuck in On position. Pilot arc will not initiate if this switch is in the
ON position. (safety reasons)
c. Check air flow switch. There may be internal short. See D..c above.
d. Measure voltage across C1 or C capacitor. It should be as follows:
approx. 5 VDC with 0 V supplied to the 08/0 volt unit.
approx. 94 VDC with 08 V supplied to the 08/0 volt unit
approx. 80 VDC with 400 V supplied to the 400 volt unit.
approx. 5 VDC with 460 V supplied to the 460 volt unit
approx. 400 VDC with 575 V supplied to the 575 volt unit
If not, one of following could be malfunctioning:
1). Check the capacitors C1 and C for any damage.
.) Check input bridge/SCR Module (IBR) This can be checked without taking it out of the circuit using an
volt/ohmeter. Replace it if found malfunctioning. Follow bridge installation instructions.
.) Check Inrush current resistor, R10 and SCR1. Both are located on the input bridge heat sink. Replace it if
malfunctioning.
e. IGBTs ( on 0 V, and 1 on the 460 V & 575 V units) may be damaged. See IGBT installation procedure. Before re-
placing IGBTs, make sure to check the zener diodes and pico fuses on the IGBT driver boards.
F. High Frequency and Pilot Arc are on but Main Arc does not transfer.
1. Make sure work clamp is connected to work material.
. Check the torch. Replace consumables if necessary.
. Make sure the current setting potentiometer is set above 10 amps. If it is, set below 10 amps, then HI FREQUENCY will
go on and off at 5 sec intervals.
SeCTION 5
MAINTeNANCe
Summary of Contents for PCM-1125
Page 4: ... table of contents ...
Page 20: ...20 section 2 description ...
Page 26: ...26 section 3 installation ...
Page 30: ...30 section 4 operation ...
Page 44: ...44 section 5 maintenance ...
Page 56: ...56 notes ...
Page 57: ...57 notes ...
Page 58: ...58 notes ...
Page 61: ......
Page 62: ......
Page 63: ......
Page 64: ......
Page 65: ......
Page 66: ......
Page 67: ......
Page 68: ......
Page 69: ......
Page 70: ......
Page 71: ......
Page 72: ......