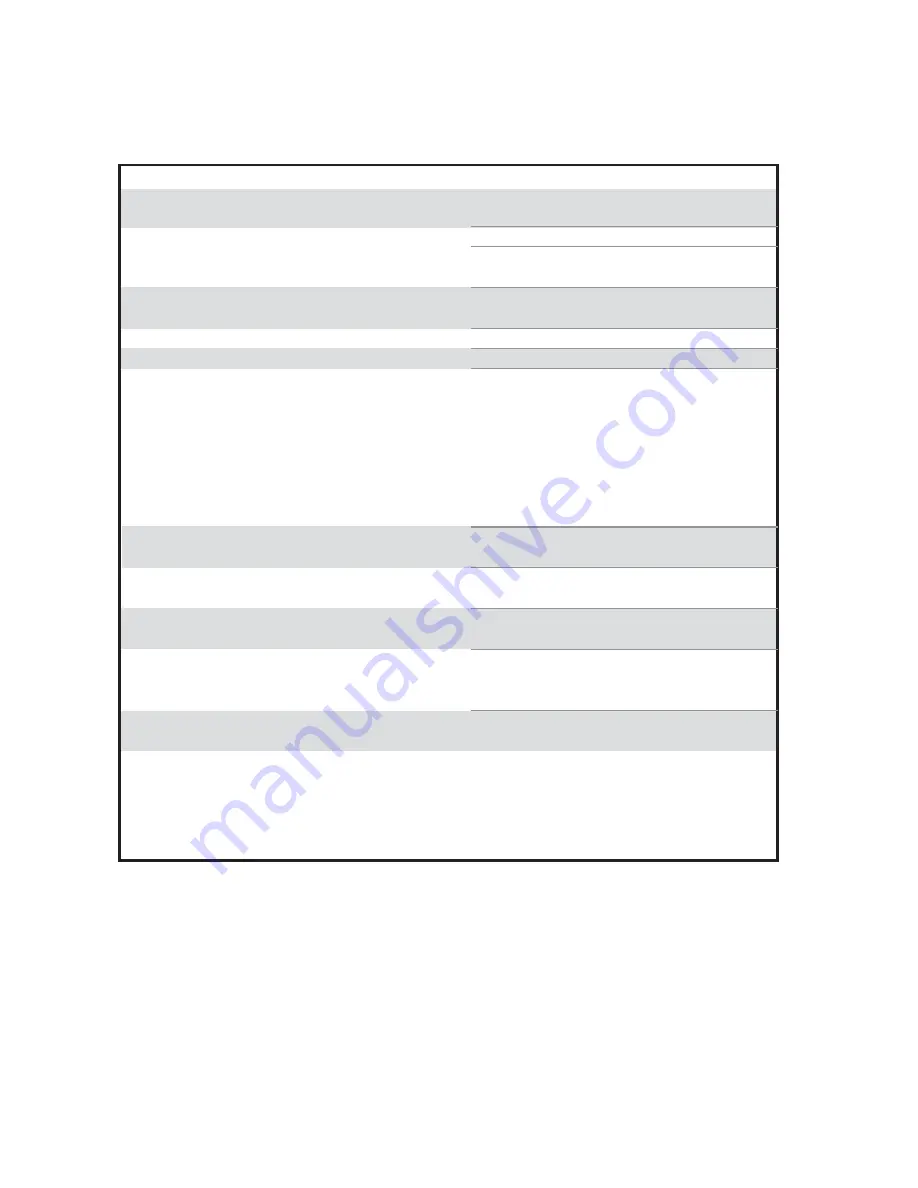
14
Note! Faults in the electrical parts such as the control circuits, relays, switches,
transformers, etc. This should only be attended to by a qualified service technician.
Common Welding Faults
Faults
Wire does not move forward
despite rotation of feed rollers.
Irregular wire feed.
Arc will not strike.
Arc too long and irregular.
Arc to short.
Porosity
Inadequate joint fill.
Lack of fusion.
Spatter.
Uneven joint
Poor Penetration
Possible Causes
1. Pressure roller inadequately loaded.
2. Dirt in wire guide or contact nozzle.
1. Faulty worn contact tip.
2. Dirt in groove of feed roller.
3. Feed roller groove worn.
1. Poor contact between return clamp and workpiece.
2. Voltage switch in the wrong (gas purge) position.
Voltage too high.
Voltage too low
1. Incorrect gas flow.
(Recommend 8-10 l/min).
2. Inadequate gas shielding due to spatter in the
nozzle.
3. Breezy workplace.
4. Welding distance too long.
5. Incorrect gun angle.
6. Damp, oily or rusty workpiece.
1. Welding speed too high.
2. Voltage too low relative to welding speed.
1. Irregular movement of gun.
2. Voltage too low.
1. Voltage too high or too low.
2. Gas nozzle dirty.
1. Wire tip too long.
2. Current too high relative to voltage.
3. Welding speed too low.
Current too low relative to voltage.