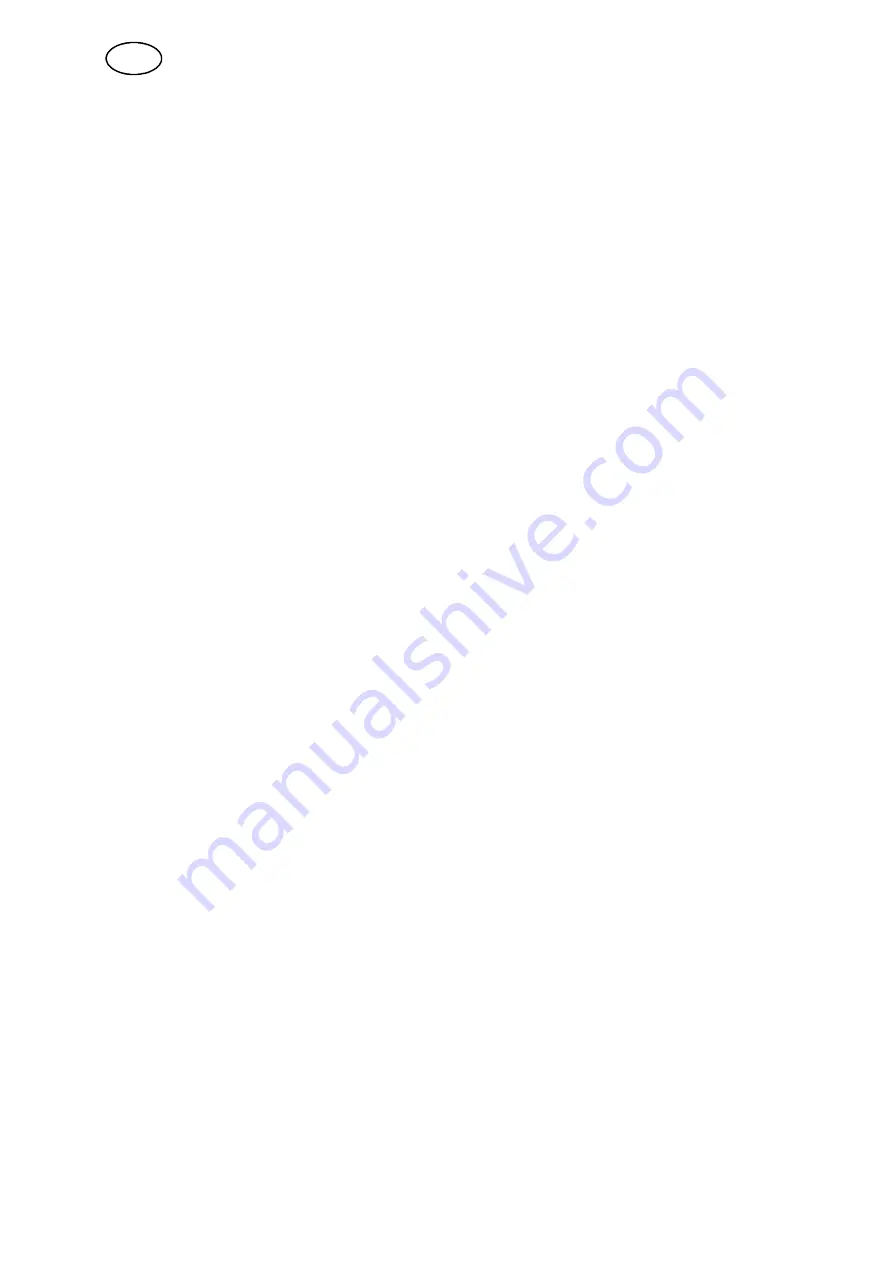
- 8 -
hga7d1ea
2.2
Connection instructions for two parallel-connected welding
power sources and one PEK control box
1. Emergency stop coil
W01
, is connected together with the enclosed contact block,
which in turn has been fitted on
KM2
, in accordance with the diagram on page
14 (automatic welding machine) or page 15 (automation).
2. On the welding power source defined as Slave
CN18
(pin 1 and 2), on
AP1
, shall
be clamped for analogue control.
3. Start up both welding power sources and connect
ESAT
to the
Master
welding
power source.
4. Set parameter
762
to
1
, Master searches for the welding power source selected
as Slave.
5. Set parameter
767
to
10
, Node address on the welding power source selected
as Slave.
6. Move the
ESAT
connection to the welding power source defined as
Slave
.
7. Set parameter
10
to
16
, Slave function.
8. Set parameter
67
to
0
, with value 1 so the welding power source expects an
analogue signal.
9. Set parameter
712
to
0
, the wire feed is not controlled by the welding power
source defined as Slave.
10. Set parameter
713
to
0
, the travel motor is not controlled by the welding power
source defined as Slave.
11. Set parameter
762
to
0
, Slave does not search for another power source.
12. Set parameter
767
to
2
, Node address on the welding power source defined as
Master.
13. Set parameter
9000
to
10
, Node address for the welding power source defined
as Slave.
14. Switch off the voltage to both welding power sources.
15. Remove the clamp on
CN18
(pin 1 and 2) on the Slave welding power source.
16. Remove the clamp on
CN11
on the Master welding power source.
17. Connect cable
W02
to the welding power sources.
18. Switch on the voltage to the Slave welding power source.
19. Switch on the voltage to the Master welding power source.
20. Check that the emergency stop coil is working, both the welding power sources
(emergency stop relay/emergency stop contactors) are switched off. After
resetting, the welding power sources start up normally and are ready for use.
21. Check that the parallel current value can be set in
PEK
.
For more information on component location on the circuit board, see the service
manual for the LAF welding power source.
GB
Summary of Contents for LAF 631
Page 1: ...0449 546 001 110217 Parallel connection of LAF welding power source Instruction manual...
Page 2: ...2 Rights reserved to alter specifications without notice ENGLISH 3...
Page 9: ...9 hga7d2ea 3 Location Drawing 3 1 Location drawing Welding Power Source LAF 631 GB...
Page 10: ...10 hga7d2ea 3 2 Location drawing Welding Power Source LAF 1001 GB...
Page 11: ...11 hga7d2ea 3 3 Location drawing Welding Power Source LAF 1251 1601 GB...
Page 14: ...DIAGRAM 14 hga7diag Tractor variant...
Page 15: ...15 hga7diag Automation variant...
Page 16: ...16 sida...
Page 18: ...18 sida...