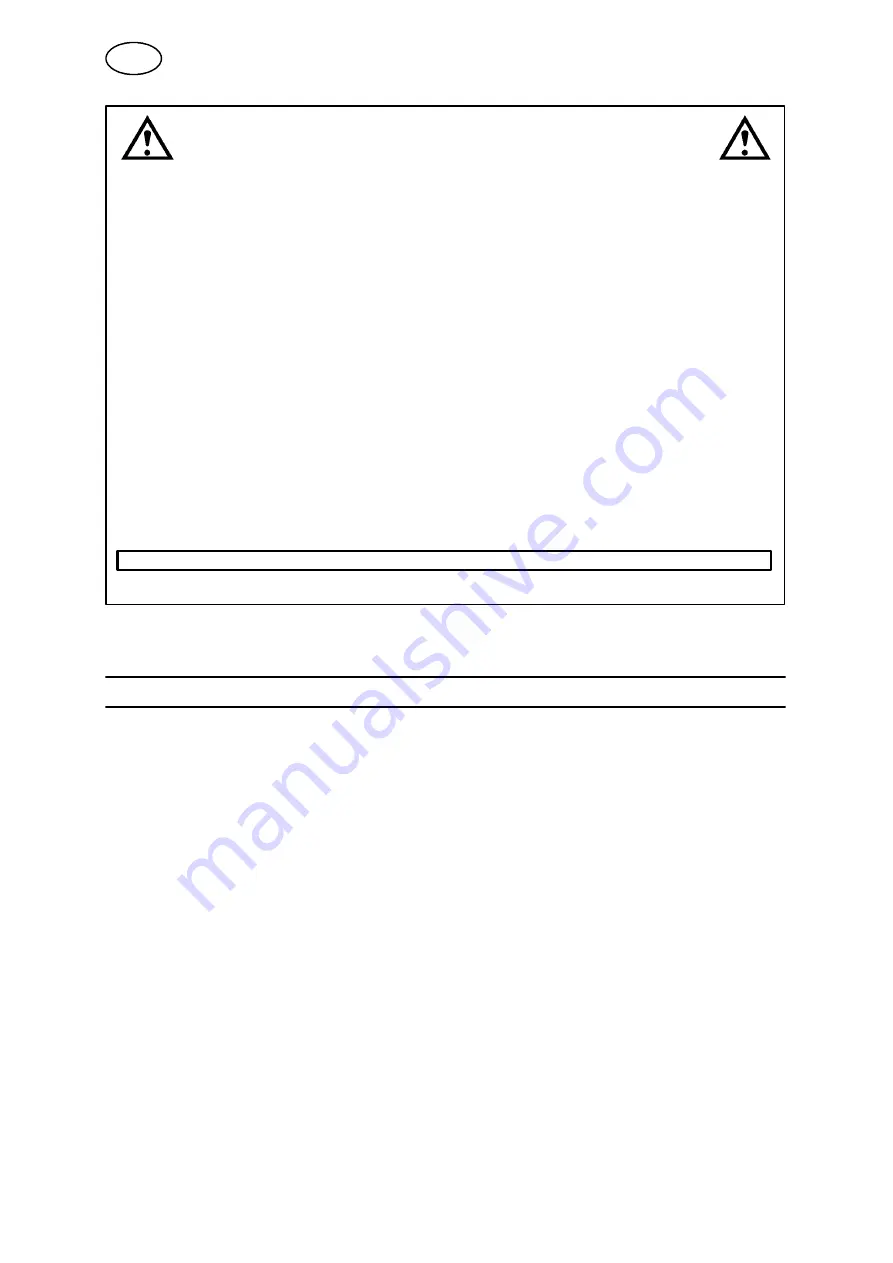
-- 13 --
ba22d12e
WARNING
READ AND UNDERSTAND THE INSTRUCTION MANUAL BEFORE INSTALLING OR OPERATING.
ARC WELDING AND CUTTING CAN BE INJURIOUS TO YOURSELF AND OTHERS. TAKE PRECAU-
TIONS WHEN WELDING. ASK FOR YOUR EMPLOYER’S SAFETY PRACTICES WHICH SHOULD BE
BASED ON MANUFACTURERS’ HAZARD DATA.
ELECTRIC SHOCK -- Can kill
S
Install and earth the welding unit in accordance with applicable standards.
S
Do not touch live electrical parts or electrodes with bare skin, wet gloves or wet clothing.
S
Insulate yourself from earth and the workpiece.
S
Ensure your working stance is safe.
FUMES AND GASES -- Can be dangerous to health
S
Keep your head out of the fumes.
S
Use ventilation, extraction at the arc, or both, to keep fumes and gases from your breathing zone and
the general area.
ARC RAYS -- Can injure eyes and burn skin.
S
Protect your eyes and body. Use the correct welding screen and filter lens and wear protective
clothing.
S
Protect bystanders with suitable screens or curtains.
FIRE HAZARD
S
Sparks (spatter) can cause fire. Make sure therefore that there are no inflammable materials nearby.
NOISE -- Excessive noise can damage hearing
S
Protect your ears. Use ear defenders or other hearing protection.
S
Warn bystanders of the risk.
MALFUNCTION -- Call for expert assistance in the event of malfunction.
PROTECT YOURSELF AND OTHERS!
8
INTRODUCTION
LAF 800/1250/1600
are remote--controlled 3--phase welding power sources de-
signed for high--efficiency mechanical gas metal arc welding (MIG/MAG) or sub arc
welding (SAW). It is always to be used in combination with ESAB‘s control box
A2--A6 Process Controller (PEH).
LAF is fan--cooled and monitored by a thermal overload protection. When the protec-
tion enters into action a yellow indicating lamp on the front panel goes on and is
reset automatically as soon as the temperature has gone down to an acceptable
level.
The welding power sources and the control unit are linked together over a 2--wire
bus enabling precision control of the welding process.
All welding parameter settings for the power source can be made by the operator on
the front panel of the control unit. The operation of the power source is completely
controlled and monitored by this unit. Even the start and stop qualities can be set by
way of the control unit. The preset welding current parameters can also be moni-
tored in the course of welding.
For more detailed information regarding the settings and the working mode of the
welding power source, please refer to the A2--A6 Process Controller (PEH) instruc-
tion manual.
GB
Summary of Contents for LAF 1250 DC
Page 2: ...2 Rights reserved to alter specifications without notice 3 ENGLISH 11...
Page 3: ...TOCr 3 1 4 2 5 2 1 6 3 7 3 1 7 3 2 7 3 3 7 3 4 9 4 10 4 1 10 4 2 10 5 10 5 1 10 6 10 19 21 23...
Page 4: ...ba22d12r 4 1 1 S S S S S 2 S S 3 S S 4 S S 5 S S S S...
Page 7: ...ba22d12r 7 3 3 1 3 2 S 3 3 S 400 S S 1 S L1 L2 L3 S LAF 12 2 S 1 4 S 3...
Page 19: ...Connection instruction 19 conn...
Page 21: ...Diagram LAF 800 21 diag...
Page 22: ...LAF 1250 1600 22 diag...
Page 27: ...12 13 14 15 16 17 18 19 20 21 22 23 24 25 26 27 28 1 11 10 9 2 3 4 5 6 7 8 27 spare...