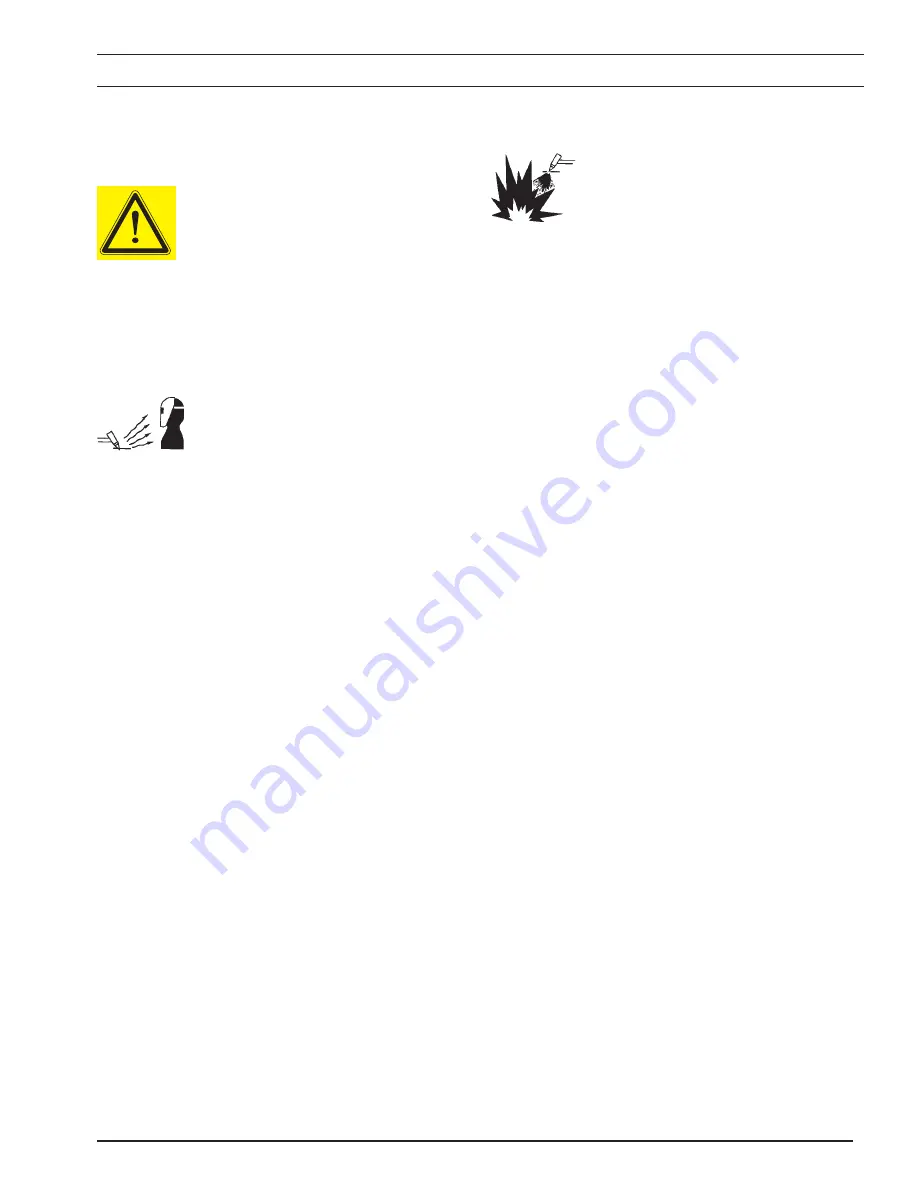
5
safety
Warning: these safety precautions are
for your protection. they summarize
precautionary information from the
references listed in additional safety
information section. Before performing
any installation or operating procedures, be sure
to read and follow the safety precautions listed
below as well as all other manuals, material safety
data sheets, labels, etc. failure to observe safety
precautions can result in injury or death.
protect Yourself anD others --
some welding, cutting, and gouging
processes are noisy and require ear
protection. the arc, like the sun, emits
ultraviolet (uv) and other radiation and can injure
skin and eyes. hot metal can cause burns. training
in the proper use of the processes and equipment
is essential to prevent accidents. therefore:
1. Always wear safety glasses with side shields in any
work area, even if welding helmets, face shields, and
goggles are also required.
2. Use a face shield fitted with the correct filter and
cover plates to protect your eyes, face, neck, and
ears from sparks and rays of the arc when operating
or observing operations. Warn bystanders not to
watch the arc and not to expose themselves to the
rays of the electric-arc or hot metal.
3. Wear flameproof gauntlet type gloves, heavy long-
sleeve shirt, cuffless trousers, high-topped shoes,
and a welding helmet or cap for hair protection, to
protect against arc rays and hot sparks or hot metal.
A flameproof apron may also be desirable as protec-
tion against radiated heat and sparks.
4. Hot sparks or metal can lodge in rolled up sleeves,
trouser cuffs, or pockets. Sleeves and collars should
be kept buttoned, and open pockets eliminated from
the front of clothing.
5. Protect other personnel from arc rays and hot sparks
with a suitable non-flammable partition or curtains.
6. Use goggles over safety glasses when chipping slag
or grinding. Chipped slag may be hot and can fly far.
Bystanders should also wear goggles over safety
glasses.
fires anD explosions -- heat from
flames and arcs can start fires. hot
slag or sparks can also cause fires and
explosions. therefore:
1. Remove all combustible materials well away from the
work area or cover the materials with a protective
non-flammable covering. Combustible materials
include wood, cloth, sawdust, liquid and gas fuels,
solvents, paints and coatings, paper, etc.
2. Hot sparks or hot metal can fall through cracks or
crevices in floors or wall openings and cause a hid-
den smoldering fire or fires on the floor below. Make
certain that such openings are protected from hot
sparks and metal.“
3. Do not weld, cut or perform other hot work until the
work piece has been completely cleaned so that there
are no substances on the work piece which might
produce flammable or toxic vapors. Do not do hot
work on closed containers. They may explode.
4. Have fire extinguishing equipment handy for instant
use, such as a garden hose, water pail, sand bucket,
or portable fire extinguisher. Be sure you are trained
in its use.
5. Do not use equipment beyond its ratings. For ex-
ample, overloaded welding cable can overheat and
create a fire hazard.
6. After completing operations, inspect the work area
to make certain there are no hot sparks or hot metal
which could cause a later fire. Use fire watchers when
necessary.
7. For additional information, refer to NFPA Standard
51B, "Fire Prevention in Use of Cutting and Welding
Processes", available from the National Fire Protection
Association, Battery march Park, Quincy, MA 02269.
section 1
safetY
Summary of Contents for Heliarc 281iAC/DC
Page 13: ...13 SECTION 4 ASSEMBLY SECTION 4 ASSEMBLY TROLLEY ASSEMBLY fig 4 1 15...
Page 14: ...14 SECTION 4 ASSEMBLY TROLLEY ASSEMBLY fig 4 2 15b SECTION 4 ASSEMBLY...
Page 15: ...15 SECTION 4 ASSEMBLY SECTION 4 ASSEMBLY POWER SOURCE TO TROLLEY ASSEMBLY fig 4 3 15c...
Page 47: ...47 SECTION 7 warranty...